On the right side of the Compliance is at the
Page 24
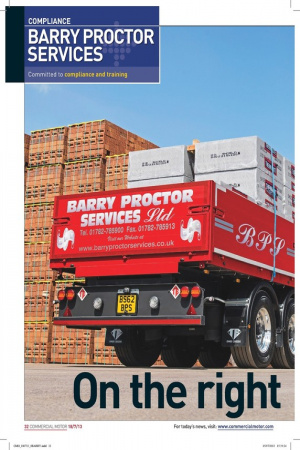
Page 25
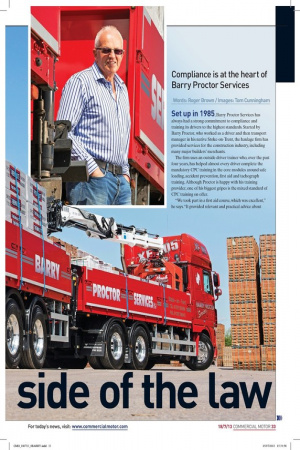
Page 26
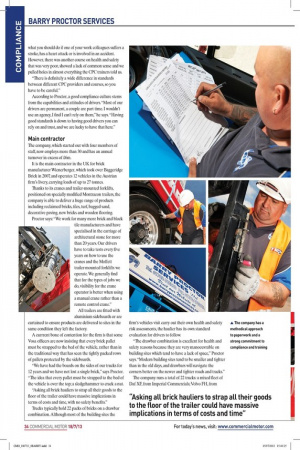
Page 27
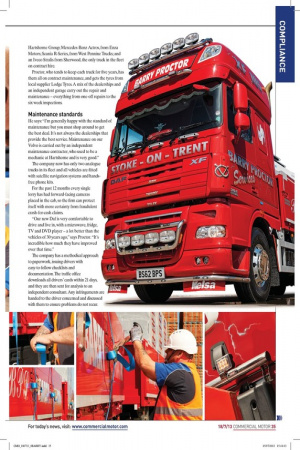
Page 28
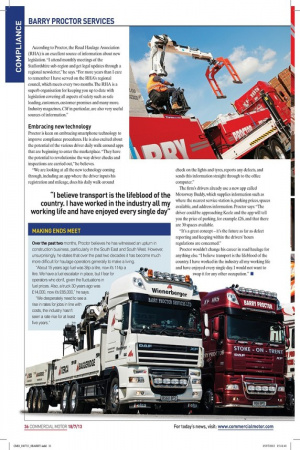
If you've noticed an error in this article please click here to report it so we can fix it.
heart of Barry Proctor Services Set up in 1985, Barry Proctor Services has always had a strong commitment to compliance and training its drivers to the highest standards. Started by Barry Proctor, who worked as a driver and then transport manager in his native Stoke-on-Trent, the haulage firm has provided services for the construction industry, including many major builders' merchants.
The firm uses an outside driver trainer who, over the past four years, has helped almost every driver complete the mandatory CPC training in the core modules around safe loading, accident prevention, first aid and tachograph training. Although Proctor is happy with his training provider, one of his biggest gripes is the mixed standard of CPC training on offer.
"We took part in a first aid course, which was excellent," he says. "It provided relevant and practical advice about what you should do if one of your work colleagues suffers a stroke, has a heart attack or is involved in an accident. However, there was another course on health and safety that was very poor, showed a lack of common sense and we pulled holes in almost everything the CPC trainers told us.
"There is definitely a wide difference in standards between different CPC providers and courses, so you have to be careful."
According to Proctor, a good compliance culture stems from the capabilities and attitudes of drivers. "Most of our drivers are permanent, a couple are part-time. I wouldn't use an agency, I find I can't rely on them," he says. "Having good standards is down to having good drivers you can rely on and trust, and we are lucky to have that here."
Main contractor The company, which started out with four members of staff now employs more than 30 and has an annual turnover in excess of ibm.
It is the main contractor in the UK for brick manufacturer Wienerberger, which took over Baggeridge Brick in 2007, and operates 12 vehicles in the Austrian firm's livery, carrying loads of up to 27 tonnes.
Thanks to its cranes and trailer-mounted forklifts, positioned on specially modified Montracon trailers, the company is able to deliver a huge range of products including reclaimed bricks, tiles, turf, bagged sand, decorative paving, new bricks and wooden flooring.
Proctor says: "We work for many more brick and block tile manufacturers and have specialised in the carriage of architectural stone for more than 20 years. Our drivers have to take tests every five years on how to use the cranes and the Moffett trailer-mounted forklifts we operate. We generally find that for the types of jobs we do, visibility for the crane operator is better when using a manual crane rather than a remote control crane."
All trailers are fitted with aluminium sideboards or are curtained to ensure products are delivered to sites in the same condition they left the factory.
A currrent bone of contention for the firm is that some Vosa officers are now insisting that every brick pallet must be strapped to the bed of the vehicle, rather than in the traditional way that has seen the tightly packed rows of pallets protected by the sideboards.
"We have had the boards on the sides of our trucks for 12 years and we have not lost a single brick," says Proctor. "The idea that every pallet must be strapped to the bed of the vehicle is over the top; a sledgehammer to crack a nut.
"Asking all brick hauliers to strap all their goods to the floor of the trailer could have massive implications in terms of costs and time, with no safety benefits."
Trucks typically hold 22 packs of bricks on a drawbar combination. Although most of the building sites the firm's vehicles visit carry out their own health and safety risk assessments, the haulier has its own standard evaluation for drivers to follow.
"The drawbar combination is excellent for health and safety reasons because they are very manoeuvrable on building sites which tend to have a lack of space," Proctor says. "Modern building sites tend to be smaller and tighter than in the old days, and drawbars will navigate the corners better on the newer and tighter roads and tracks."
The company runs a total of 22 trucks: a mixed fleet of Daf XF, from Imperial Commercials; Volvo FH, from Hartshorne Group; Mercedes-Benz Actros, from Enza Motors; Scania R-Series, from West Pennine Trucks; and an Iveco Stralis from Sherwood, the only truck in the fleet on contract hire.
Proctor, who tends to keep each truck for five years, has them all on contract maintenance, and gets the tyres from local supplier Lodge Tyres. A mix of the dealerships and an independent garage carry out the repair and maintenance — everything from one-off repairs to the six week inspections.
Maintenance standards He says: "I'm generally happy with the standard of maintenance but you must shop around to get the best deal. It's not always the dealerships that provide the best service. Maintenance on our Volvo is carried out by an independent maintenance contractor, who used to be a mechanic at Hartshorne and is very good."
The company now has only two analogue trucks in its fleet and all vehicles are fitted with satellite navigation systems and handsfree phone kits.
For the past 12 months every single lorry has had forward-facing cameras placed in the cab, so the firm can protect itself with more certainty from fraudulent crash-for-cash claims.
"Our new Daf is very comfortable to drive and live in, with a microwave, fridge, TV and DVD player — a lot better than the vehicles of 30 years ago," says Proctor. "It's incredible how much they have improved over that time."
The company has a methodical approach to paperwork, issuing drivers with easy-to-follow checklists and documentation. The traffic office downloads all drivers' cards within 21 days, and they are then sent for analysis to an independent consultant. Any infringements are handed to the driver concerned and discussed with them to ensure problems do not recur. According to Proctor, the Road Haulage Association (RHA) is an excellent source of information about new legislation. "I attend monthly meetings of the Staffordshire sub-region and get legal updates through a regional newsletter," he says. "For more years than I care to remember I have served on the RHA's regional council, which meets every two months. The RHA is a superb organisation for keeping you up to date with legislation covering all aspects of safety such as safe loading, customers, customer premises and many more. Industry magazines, CM in particular, are also very useful sources of information."
Embracing new technology Proctor is keen on embracing smartphone technology to improve compliance procedures. He is also excited about the potential of the various driver daily walk-around apps that are beginning to enter the marketplace. "They have the potential to revolutionise the way driver checks and inspections are carried out," he believes.
"We are looking at all the new technology coming through, including an app where the driver inputs his registration and mileage, does his daily walk-around check on the lights and tyres, reports any defects, and sends this information straight through to the office computer."
The firm's drivers already use a new app called Motorway Buddy, which supplies information such as where the nearest service station is, parking prices, spaces available, and address information. Proctor says: "The driver could be approaching Keele and the app will tell you the price of parking, for example £26, and that there are 30 spaces available.
"It's a great concept — it's the future as far as defect reporting and keeping within the drivers' hours regulations are concerned."
Proctor wouldn't change his career in road haulage for anything else. "I believe transport is the lifeblood of the country. I have worked in the industry all my working life and have enjoyed every single day. I would not want to swap it for any other occupation." •