Artic handling highlighted at Cran field equipment symposium
Page 45
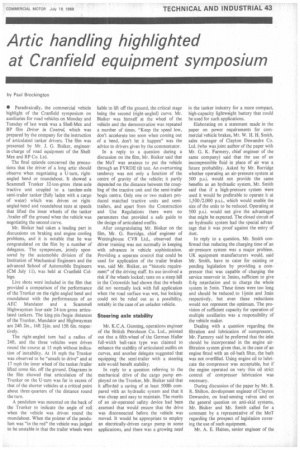
Page 46
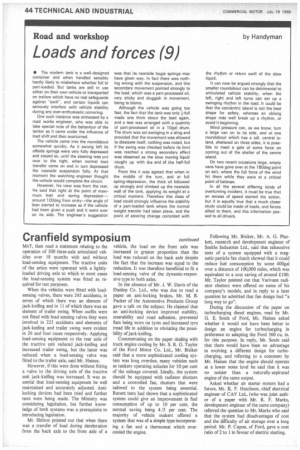
If you've noticed an error in this article please click here to report it so we can fix it.
by Paul Brockington
• Paradoxically, the commercial vehicle highlight of the Cran field symposium on auxiliaries for road vehicles on Monday and Tuesday of last week was a Shell-Mex and BP film Driver in Control, which was prepared by the company for the instruction of articulated tanker drivers. The film was presented by Mr. J. G. Bisiker, engineerin-charge of road equipment of the ShellMex and BP Co. Ltd.
The final episode concerned the precautions that the driver of a long artic should observe when negotiating a U-turn, rightangled bend or roundabout. It showed a Scam-tell Trunker 32-ton-gross three axle tractive unit coupled to a tandem-axle semi-trailer tanker (fully laden with a cargo of water) which was driven on rightangled-bend and roundabout tests at speeds that lifted the inner wheels of the tanker /trailer off the ground when the vehicle was negotiating the second curve.
Mr. Bisiker had taken a leading part in discussions on braking and engine cooling problems, and it is notable that he was congratulated on the film by a number of delegates. The symposium, jointly sponsored by the automobile division of the Institution of Mechanical Engineers and the advanced School of Automobile Engineers (CM July 11), was held at Cranfield College.
Live shots were included in the film that provided a comparison of the performance of the Trunker on the right-angled bend and roundabout with the performances of an AEC Mandator and a Scammell Highwayman four-axle 24-ton-gross articulated tankers. The king-pin /bogie distances of the Trunker, Mandator and Highwayman are 24ft 2in.. 16ft 2+n. and 1511 6in. respectively.
The right-angled turn had a radius of 2411, and the three vehicles were driven round the course at 15 mph without indication of instability. At 16 mph the Trunker was observed to be "unsafe to drive" and at 17 mph the inner wheel of the tanker /trailer lifted some 6in. off the ground. Diagrams in the film showed that articulation of the Trunker on the U-turn was far in excess of that of the shorter vehicles at a critical point about three-quarters of the distance round the turn.
A pendulum was mounted on the back of the Trunker to indicate the angle of roil when the vehicle was driven round the roundabout. When the pointer of the pendulum was "in the red" the vehicle was judged to be unstable in that the trailer wheels were liable to lift off the ground, the critical stage being the second (right-angled) curve. Mr. Bisiker was himself at the wheel of the vehicle and the demonstration was repeated a number of times. "Keep the speed low, don't accelerate too soon when coming out of a bend, don't let it happen" was the advice to drivers given by the commentator.
In a reply to a question during a discussion on the film, Mr. Bisiker said that the MoT was anxious to put the vehicle through an FVRDE tilt test. An overturning tendency was not only a function of the centre of gravity of the vehicle; it partly depended on the distance between the coupling of the tractive unit and the semi-trailer bogie centre. Only one or two makers produced matched tractive units and semitrailers, and apart from the Construction and Use Regulations there were no parameters that provided a safe guide to the design of articulated outfits.
After congratulating Mr. Bisiker on the film, Mr. G. Burridge, chief engineer of Westinghouse CVB Ltd., observed that driver training was not normally in keeping with advances in vehicle sophistication. Providing a separate control that could be used for application of the trailer brakes was, said Mr. Bisiker, an "historic requirement" of the driving staff. Its use involved a risk if the wheels locked; tests on a steep hill in the Cotswolds had shown that the wheels did not normally lock with full application when the road surface was wet, but locking could not be ruled out as a possibility, notably in the ease of an unladen vehicle.
Steering axle stability Mr. K.C.A. Gunning, operations engineer of the British Petroleum Co. Ltd., pointed out that a fifth-wheel of the German Haller full-width ball-race type was claimed to enhance the stability of articulated outfits on curves, and another delegate suggested that equipping the semi-trailer with a steering axle would benefit stability.
In reply to a question referring to the mechanical drive of the cargo pump employed on the Trunker, Mr. Bisiker said that it afforded a saving of at least 500th compared with an hydraulic system and that it was cheap and easy to maintain. The merits of an air-operated safety device had been assessed that would ensure that the drive was disconnected before the vehicle was moved. It would be appropriate to employ an electrically-driven cargo pump in some applications, and there was a growing need in the tanker industry for a more compact, high-capacity lightweight battery that could be used for such applications.
Elaborating on a statement made in the paper on power requirements for commercial vehicle brakes, Mr. W. H. H. Smith, sales manager of Clayton Dewandre Co. Ltd. (who was joint author of the paper with Mr. G. K. Farmery, chief engineer of the same company) said that the use of an incompressible fluid in place of air was a future probability. Asked by Mr. Burridge whether operating an air-pressure system at 500 p.s.L would not provide the same benefits as an hydraulic system, Mr. Smith said that if a high-pressure system were used it would be preferable to operate it at 1,500/2,000 p.s.i., which would enable, the size of the units to be reduced. Operating at 500 p.s.i. would not give the advantages that might be expected. The closed circuit of an hydraulic system had the special advantage that it was proof against the entry of dust.
In reply to a question, Mr. Smith confirmed that reducing the charging time of an air pressure system was a major problem. UK equipment manufacturers would, said Mr. Smith, have to cater for existing or pending legislation by providing a compressor that was capable of • charging the service reservoir in 3mins, sufficient to give 0.4g retardation and to charge the whole system in 5min. These times were too long and should be reduced to llmin and 3min respectively, but even these reductions would not represent the optimum. The provision of sufficient capacity for operation of multiple auxiliaries was a responsibility of the vehicle maker.
Dealing with a question regarding the filtration and lubrication of compressors, Mr. Farrnery said he preferred that the inlet should be incorporated in the engine airfiltration system given that, in the case of an engine fitted with an oil-bath filter, the bath was not overfilled. Using engine oil to lubricate the compressor was acceptable. but if the engine operated on very thin oil strict control of compressor lubrication was necessary.
During discussion of the paper by Mr. B. R. Shilton, development engineer of Clayton Dewandre, on load-sensing valves and on the general question on anti-skid systems, Mr. Bisiker and Mr. Smith called for a comment by a representative of the MoT regarding the prospect of legislation covering the use of such equipment.
Mr. A. E. Haines, senior engineer of the MoT, then read a statement relating to the operation of 300 three-axle articulated vehicles over 18 months with and without load-sensing equipment. The tractive units of the artics were operated with a lightlyloaded driving axle to which in most cases the load-sensing system was fitted as required for test purposes.
When the vehicles were fitted with loadsensing valves, there were 245 accidents, in seven of which there was an element of jack-knifing and in 11 of which there was an element of trailer swing. When outfits were not fitted with load-sensing valves they were involved in 223 accidents and elements of jack-knifing and trailer swing were evident in 26 and four cases respectively. Applying load-sensing equipment to the rear axle of the tractive unit reduced jack-knifing and increased trailer swing, but the latter was reduced when a load-sensing valve was fitted to the trailer axle, said Mr. IlaMes.
However, if this were done without fitting a valve to the driving axle of the tractive unit jack-knifing was increased. It was essential that load-sensing equipment be well maintained and accurately adjusted. Antilocking devices had been tried and further tests were being made. The Ministry was considering legislation, but further knowledge of both systems was a prerequisite to introducing legislation.
Mr. Shilton pointed out that when there was a transfer of load during deceleration from the back axle to the front axle of a vehicle, the load on the front axle was increased in greater proportion than the load was reduced on the back axle despite the fact that the increase was equal to the reduction. It was therefore beneficial to fit a load-sensing valve of the dynamic-responsive type to both axles.
In the absence of Mr. J. W. Davis of the Dunlop Co. Ltd., who was due to read a paper on anti-locking brakes, Mr. M. B. Packer of the Automotive Products Group gave a talk on the subject. He claimed that an 'anti-locking device improved stability, steerability and road adhesion, prevented flats being worn on tyres and increased tyre tread life in addition to obviating the possibility of jack-knifing.
Commentating on the paper dealing with truck engine cooling by Mr. S. R. G. Taylor of the Ford Motor Co. Ltd., Mr. Bisiker said that a more sophisticated cooling system was long overdue, many vehicles such as tankers operating unladen for 50 per cent of the mileage covered. Ideally, the system should be equipped with radiator shutters and a controlled fan, shutters that were tailored to the system being essential. Recent tests had shown that a sophisticated system could give an improvement in fuel consumption of up to 10 per cent, the normal saving being 4/5 per cent. The majority of vehicle makers offered a system that was of a simple type incorporating a fan and a thermostat which overcooled the engine.
Following Mr. Bisiker, Mr. A. G. Plackett, research and development engineer of Smiths Industries Ltd., said that exhaustive tests of a system equipped with a magnetic-particle fax' clutch showed that it could reduce fuel consumption by some 400gal over a distance of 100,000 miles, which was equivalent to a cost saving of around £100. Mr. Taylor pointed out that Varivane radiator shutters were offered on some of his company's models, and in reply to a later question he admitted that fan design had "a long way to go".
During the discussion of the paper on turbocharging diesel engines, read by Mr. G. E. Soule of Ford, Mr. Haines asked whether it would not have been better to design an engine for turbocharging in preference to adapting the Ford 360 Cu. in. for this purpose. In reply, Mr. Soule said that there would have been no advantage in evolving a different design for turbocharging, and referring to a comment by Mr. Haines that the engine should operate at a lower noise level he said that it was no noisier than a naturally-aspirated engine of the same output Asked whether air starter motors had a future, Mr. K. F. Hutcheon, chief electrical engineer of CAV Ltd., (who was joint author of a paper with Mr. R. F. Marks, development engineer of the same company) referred the question to Mr. Marks who said that the system had disadvantages of cost and the difficulty of air storage over a long period. Mr. P. Capon, of Ford, gave a cost ratio of 2 to 1 in favour of electric starting.