Rigid Control Wastes Money
Page 71
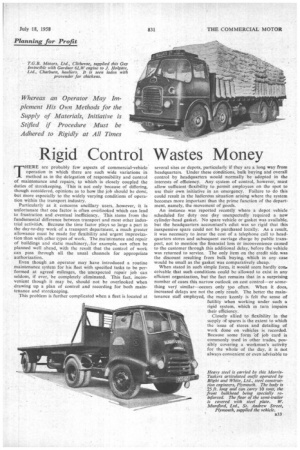
Page 72
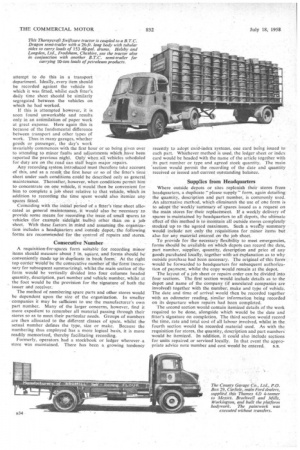
If you've noticed an error in this article please click here to report it so we can fix it.
Whereas an Operator May Implement His Own Methods for the Supply of Materials, Initiative is Stifled if Procedure Must be Adhered to Rigidly at All Times
THERE are probably few aspects of commercial-vehicle operation in which there are such wide variations in method as in the delegation of responsibility and control of maintenance and repairs, to which is closely coupled the duties of storekeeping. This is not only because of differing, though considered, opinions as to how the job should be done, but more especially to the widely varying conditions of operation within the transport industry.
Particularly as it concerns ancillary users, ,however, it is unfortunate that one factor is often overlooked which can lead to frustration and eventual inefficiency. This stems from the fundamental difference between transport and most other industrial activities. Because the time factor plays so large a part in the day-to-day work of a transport department, a much greater allowance must be made for flexibility and urgent improvization than with other types of work. The maintenance and repair of buildings and static machinery;_for example, can often be planned well ahead, with the result that the control of work can pass through all the usual channels for appropriate authorization.
Even though an operator may have introduced a routine maintenance system for his fleet with specified tasks to be performed at agreed mileages, the unexpected repair job can seldom, if ever, be completely eliminated. This fact, inconvenient though it may be, should not be overlooked when drawing up a plan of control and recording for both maintenance and storekeeping.
This problem is further complicated when a fleet is located at
several sites or depots, particularly if they are a long way from headquarters. Under these conditions, bulk buying and overall control by headquarters would normally be adopted in the interests of efficiency. Any system of control, however, must allow sufficient .flexibility to permit employees on the spot to use their own initiative in an emergency. Failure to do this could result in the ludicrous situation arising where the system becomes more important than the prime function of the department, namely, the movement of goods.
An instance was reported recently where a depot vehicle scheduled for duty one day unexpectedly required a new cylinder-head gasket. No spare vehicle or gasket was available, but the headquarters accountant's edict was so rigid that this inexpensive spare could not be purchased locally. As a result, it was necessary to incur the cost of a telephone call to headquarters stores and subsequent carriage charge by public transport, not to mention the financial loss or inconvenience caused to the customer through this additional delay, before the vehicle was returned to service. The only item on the credit side was the discount resulting from bulk buying, which in any case would be small as the gasket was comparatively cheap.
When stated in such simple form, it would seem hardly coup ceivable that such conditions could be allowed to exist in any efficient organization, but the fact remains that in a surprising number of cases this narrow outlook on cost control—or something very similar—occurs only too often. When it does, increased delays are not the only result. The better the maintenance staff employed, the more keenly is felt the sense of futility when working under such a rigid system, .which in turn impairs their efficiency.
Closely allied to flexibility in the supply of spares is the extent to which the issue of stores and detailing of work done on vehicles is recorded_ Because some form Of job card is commonly used in other trades, possibly covering a workman's activity for the whole of the day, it is not always convenient or even advisable to
attempt to do this in a transport department. Ideally, every item should be recorded against the vehicle to which it was fitted, whilst each fitter's daily time sheet should be similarly segregated 'between the vehicles on which he had worked.
If this is attempted however, it is soon found unworkable and results only in an assimilation of paper work at great expense. Here again this is because of the fundamental difference between transport and other types Of work. Thus in many garages, whether goods or passenger, the day's work invariably commences with the first hour or so being given over to attending to minor faults and adjustments which have been reported the previous night. Only when all vehicles scheduled for duty are on the road can staff begin major repairs.
Any recording system introduced must therefore take account of this, and as a result, the first hour or so of the fitter's time sheet under such conditions could be described only as general maintenance. Thereafter, however, when conditions permit him to concentrate on one vehicle, it would -then be convenient for him to complete a job sheet relative to that vehicle, which in addition to recording the time spent would also itemize any
spares fitted. • .
Coinciding with the initial period of a fitter's time sheet allocated as general maintenance,. it would also be necessary to provide some means for recording the issue of small wares tovehicles (for example sidelight -bulbs) other than on a job. sheet. With these factors. in Mind and assuming the organiza-. tion includes a headqtiarters and Outside depot, the following forms are recommended for the -control Of repairs and stores: Consecutive Number A requisition-for-spares form suitablefor recording minor items should measure about 5 in. sqiiare, and forms should he conveniently made up in duplicate in book form: At the right top cornet' Wonld • be the consectitive number of the form (necessary for subsequent summarizing), whilst the main section of the form would be vertically divided into four columns headed quantity, description, part number and vehicle number, whilst at the foot would be the provision for the signature of both the issuer and ,receiver.
The method of numbering spare parts and other stores would be dependent upon the size of the organization. In smaller companies it may be sufficient to use the manufacturer's own part number. Many of the larger concerns, however, find it more expedient to renumber all material passing through their stores so as to meet their particular needs. Groups of numbers are then allocated to the different classes of spare, whilst the actual number defines the type. size or make. Because the numbering thus employed has a more logical basis, it is more readily memorized, thereby facilitating recording.
Formerly, operators had a stockbook or ledger wherever a store was maintained. There has been a growing tendency recently to adopt card-index systems, one card being issued to each part. Whichever method is used, the ledger sheet or index card would be headed with the name of the article together with its part number or type and agreed stock quantity. The main 'section would permit the recording of the date and quantity received or issued and current outstanding balance.
Supplies from Headquarters Where outside depots or sites replenish their stores from headquarters, a duplicate 'please supply" form, again detailing the quantity, description and part number, is commonly used. An alternative method, which eliminates the use of one form is to adopt the weekly Surrimary of spares issued as a request on the main stores for their replacement. If a weekly delivery of spares is maintained by headquarters to all depots, the ultimate effect of this method is to Maintain all outside stores completely stocked up to the agreed maximum. Such a weeltly summary would include not only the :requisitions for minor items but also for any material entered on the job sheet.
To provide for the necessary flexibility to meet emergencies, forms should be available on which depots can record the date, part number, supplier, quantity, description and price of any goods purchased locally, together with-an explanation as to why outside purchase had been necessary. The original of-this form would be forwarded to headquarters for subsequent authorization of payment, whilst the copy would remain at the depot.
The layout of a job sheet or repairs order can be divided into four sections. The first section would include details as to the depot and name of the company (if associated companies are involved) together with the number, make and type of vehicle. The date and time of arrival would then be recorded together with an odometer reading, similar information being recorded on its departure when repairs had been completed.
The second section would contain itemized details of the work required to be done, alongside which would be the date and fitter's signature on completion. The third section would record the time, rate and total cost of all labour involved, whilst in the fourth section would be recorded material used. As with the requisition for stores, the quantity, description and part numbers would be itemized. In addition, it could also include sections for units repaired or serviced locally. In that event the appro priate advice note number and cost would be entered. S.B.