LIGHT WORK WITH 24 )NS GROSS
Page 54
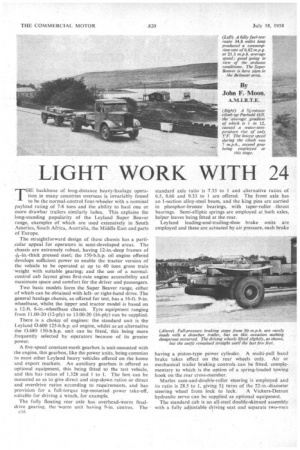
Page 55
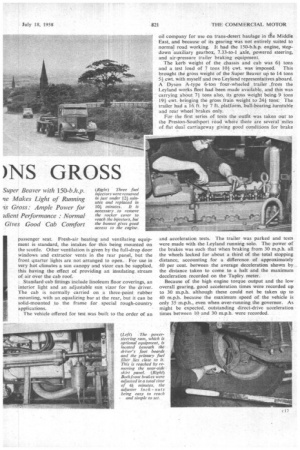
Page 56
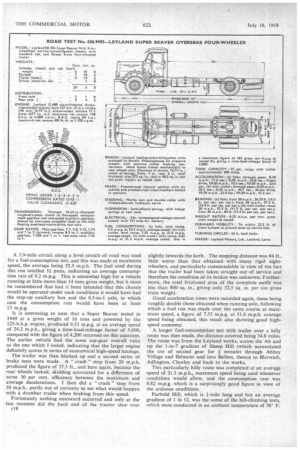
Page 57
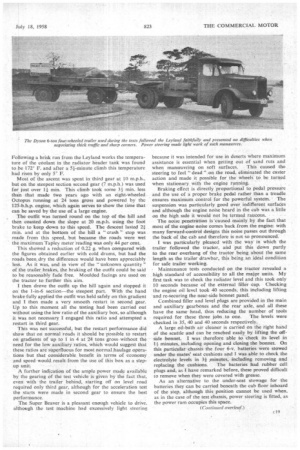
Page 58
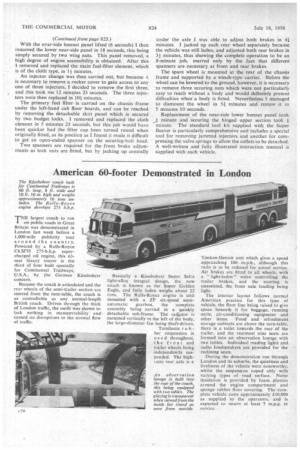
If you've noticed an error in this article please click here to report it so we can fix it.
By John F. -Moak,
Super Beaver with 150-b.h.p. Pie Makes Light of Running Gross .• Ample Power for 7dient Performance : Normal Gives Good Cab Comfort
' HE backbone of long-distance heavy-haulage opera
T
tion in many countries overseas is invariably found to be the normal-control four-wheeler with a nominal payload rating of 7-8 tons and the ability to haul one or more drawbar trailers similarly laden. This explains the long-standing popularity of the Leyland Super Beaver range, examples of which are used extensively in South • America,. South Africa, Australia, the Middle East and parts of Europe.
The straightforward design of these chassis has a parti,cular appeal for operators in semi-developed areas. The chassis are extremely robust, having 12-in.-deep frames of 15K-in.-thick pressed steel; the 150-b.h.p. oil engine offered develops sufficient power to enable the tractor version of the vehicle to be operated at up to 40 tons gross train weight . with suitable gearing; and the use of a normalcontrol cab layout gives first-rate engine accessibility and maximum space and comfort for the driver and passengers.
Two basic models form the Super Beaver range, either of which can be obtained with leftor right-hand drive. The general haulage chassis, as offered for test, has a 16-ft. 9-in. wheelbase, whilst the tipper and tractor model is based on a 12-ft. 6-in.-wheelbase chassis. Tyre equipment ranging from 11.00-20 (12-ply) to 13.00-20 (16-ply) can be supplied.
There is a choice of engines: the standard unit is the Leyland 0.600 125-b.h.p. oil engine, whilSt as an alternative the 0.680 150-b.h.p. unit can be fitted, this being more -frequently selected by operators because of its greater power.
A five-speed constant-mesh gearbox is unit-mounted with the engine, this gearbox, like the power Units, being common to most other Leyland heavy vehicles offered on the home and export markets. An auxiliary gearbox is offered as optional equipment, this being fitted to the test vehicle, and this has ratios of 1.328 and 1 to 1. The box can be mounted so as to give direct and step-down ratios or direct and overdrive ratios aceOrding to requirements, and has provision for a full-torque top-mounted power take-off, suitable for driving a winch, for example. . .
The fully floating rear axle has overhead-worm finaldrive gearing. the 'worm unit haVing. 9-in. centres. The c16
standard axle ratio is 7.33 to 1 and alternative ratios of 6.5, 8.66 and 9.33 to 1 are offered. The front axle has an I-section alloy-steel beam, and the king pins are carried in phosphor-bronze bearings, with taper-roller -thrust bearings. Semi-elliptic springs are employed at both axles, helper leaves being fitted at the rear.
Leyland leading-and-trailing-shoe brake units are employed and these are actuated by air pressure, each brake
having a piston-type power cylinder. A multi-pull hand brake takes effect on the rear wheels only. Air or mechanical trailer braking controls can be fitted, complementary to which is the option of a spring-loaded towing hook on the rear cross-member.
Marks cam-and-double-roller steering is employed and its ratio is 28.5 to I, giving 51 turns of the 22-in.-diameter steering wheel from lock to lock. A Vickers-Detroit hydraulic servo can be supplied as optional equipment. The standard cab is an all-steel double-skinned assembly with a fully adjustable driving seat and separate two-man passenger seat. Fresh-air heating and ventilating equipment is standard, the intakes for this being mounted on the scuttle. Other ventilation is given by the full-drop door windows and extractor vents in the rear panel, hut the front quarter lights are not arranged to open. For use in very hot climates a sun canopy and vizor can be supplied, this having the effect of providing an insulating. stream of air over the cab roof.
Standard cab fittings include linoleum floor coverings, an interior light and an adjustable sun vizor for the driver. The cab is normally carried on a three-point rubber mounting, with an,equalizing bar at the rear, but it can be solid-mounted to the frame for special rough-country applications. • The vehicle offered for test was built to the order of an oil company for use on trans-desert haulage in tie Middle East, and because of its gearing was not entirely suited to normal road working. It had the 150-b.h.p. engine, stepdown auxiliary gearbox, 7.33-to-1 axle, powered steering, and air-pressure trailer braking equipment.
The kerb weight of the chassis and cab was 6f tons and a test load of 7 tons 101 cwt. was imposed. This brought the gross weight of the Super Beaver up to 14 tons 51 cwt. with myself and two Leyland representatives aboard. A' Dyson A-type 6-ton foirr-wheeled trailer .from the Leyland works fleet had been made available, and this was carrying about 71 tons also, its gross weight being 9 tons 19+ cwt. bringing the gross train weight to 241 tons': The trailer had a 16, ft. by 7 ft platfiarm, ball bearingturntable and rear wheel'brakes only. '
FOr the first :series of tests the outfit was taken out to the Preston-Southport road where there are several miles of flat dual carriageway giving good conditions for brake and acceleration tests. The trailer was parked and tests were made with the Leyland running solo. The power of the brakes was such that when braking from 30 m.p.h. all the wheels locked for about a third of the total stopping distance, accounting for a difference of approximately 40 per cent. between the average deceleration shown by . the distance taken to come to a halt and the maximum deceleration recorded on the Tapley. meter.
Because of the high engine torque output and the low overall gearing, good acceleration times were recorded up to 30 m.p.h. although these could not be taken up to 40 m.p.h. because the maximum speed of the vehicle is only 35 m.p.h., even when over-running the governor. As might be expected, outstanding direct-drive acceleration times between 10 and 30 rn.p.h. were recorded.
A 5.9-mile circuit along a level stretch of road was used for a fuel-consumption test, and this was made at maximum speed, the average being 32.5 m.p.h. The fuel used during this run totalled 571 pints, indicating an average consumption rate of 9.2 m.p.g. This is somewhat high for a vehicle running at little more than 14 tons gross weight, but it must be remembered that had it been intended that this chassis would be operated under such conditions it would have had the step-up auxiliary box and the 6.5-to-1 axle, in which case the consumption rate would have been at least 13 m.p.g.
It is interesting to note that a Super Beaver tested in 1949 at a gross weight of 16 tons and powered by the 125-b.h.p. engine, produced 9.33 m.p.g. at an average speed of 24.2 m.p.h., giving a time-load-mileage factor of 3,600, compared with the figure of 4,200 returned on this occasion. The earlier vehicle had the same top-gear overall ratio as the one which I tested, indicating that the larger engine definitely _scores in terms of economical high-speed haulage. The trailer was then hitched up and a second series of brake tests were made. A " crash " stop from 20 m.p.h. produced the figure of 37.5 ft., and here again, because the rear wheels locked, skidding accounted for a difference of some 30 per cent, efficiency between the maximum and average decelerations. I then did a " crash " stop from 30 m.p.h., partly out of curiosity to see what would happen with a drawbar trailer when braking from this speed.
Fortunately nothing untoward occurred and only at the last moment did the back end of the tractor slew over c18
slightly towards the kerb. The stopping distance was 84 ft., little worse than that obtained with many rigid eightwheelers, and particularly commendable in view of the fact that the trailer had been taken straight out of service and therefore the condition of its brakes was unknown. Furthermore, the total frictional area of the complete outfit was less than 800 sq. in., giving only 32.5 sq. in. per ton gross train weight.
Good acceleration times were recorded again, these being roughly double those obtained when running solo, following which a fuel run was made over the same course at maximum speed, a figure of 7.55 m.p.g. at 31.6 m.p.h. average speed being obtained, this result also showing good highspeed economy.
A longer fuel-consumption test with trailer over a hilly route was then made, the distance covered being 34.8 miles. The route was from the Leyland works, across the A6 and up the 1-in-7 gradient of Sheep Hill (which necessitated the use of second gear for I minute) through Abbey Village and Belmont and into Bolton, thence to Harwich, Adlington, Chorley and back to the works.
This particularly hilly route was completed at an average speed of 21.3 m.p.h., maximum speed being used whenever conditions would allow, and the consumption rate was 6.82 m.p.g. which is a surprisingly good figure in view of the arduous conditions..
Parbold Hill, which is 1-mile long and has an average gradient of 1 in 12, was the scene of the hill-climbing tests, which were conducted in an ambient temperature of 56° F. Following a brisk run from the Leyland works the temperature of the coolant in the radiator header tank was found to be 172° F. and after a 51-minute climb this temperature had risen by only 5° F.
Most of the ascent was spent in third gear at 10 m.p.h., but on the steepest section second gear (7 m.p.h.) was used for just over 1+ min. This climb took some 31 min. less than that made two years ago with an eight-wheeled Octopus running at 24 tons gross and powered by the 125-b.h.p. engine, which again serves to show the time that can be saved by the use of a large engine.
The outfit was turned round on the top of the hill and then coasted down the slope at 20 m.p.h. using the foot brake to keep down to this speed. The descent lasted 2+ niM. and at the bottom of the hill a "crash" stop was made from this speed, but because the roads were wet the maximum Tapley meter reading was only 44 per cent_ This showed a reduction of 0.22 g. when compared with the figures obtained earlier with cold drums, but had the roads been dry the difference would have been appreciably less. As it was, and in view of the "unknown quantity" of the trailer brakes, the braking of the outfit could be said to be reasonably fade free. Moulded facings are used on the tractor to further this aim.
I then drove the outfit up the hill Again and stopped it on the 1-in-6 section—the steepest part. With the hand brake fully applied the outfit was held safely on this gradient and I then made a very smooth restart in second gear. Up to this moment all the testing had been carried out without using the low ratio of the auxiliary box, so although it was not necessary. I engaged this ratio and attempted a restart in third gear.
This was not successful, but the restart performance did show that oti normal roads it should be possible to restart on gradients of up to 1 in 4 at 24 tons gross without the need for the low auxiliary ratios, which would suggest that these ratios are superfluous for most normal.hattlage operations but that considerable benefit in terms of economy and speed would result from the use of this box as a stepup unit.
A further indication of the ample power made available by the gearing of the test vehicle is given by the fact that, even with the trailer behind, starting off on level road required only third gear, although for the acceleration test the starts were made in second gear to ensure the best performance.
The Super Beaver is a pleasant enough vehicle to drive, although the test machine had excessively light steering because it was intended for use in deserts where maximum assistance is essential when getting out of sand ruts and when manceuvring on soft surfaces. This caused the steering to feel " dead "on the road, eliminated the caster action and made it possible for the wheels to be turned when stationary with the engine running.
Braking effect is directly 'proportional to pedal pressure and the use of a proper brake pedal rather than a treadle ensures maximum control for the powerful system. The suspension was particularly good over indifferent surfaces and although the engine noise heard in the cab was a little on the high side it would not be termed raucous.
The noise penetration is 'caused mainly by the fact that most of the engine noise comes back from the engine: with many forward-contrel designs this noise passes out through the back of the cab and therefore is not so pronounced.
I was particularly pleased with the way in which the trailer followed the tractor, and put this down partly to the rear overhang of the tractor being about the same length as the trailer drawbar, this being an ideal condition for safe trailer working.
Maintenance tests conducted on the tractor revealed a high standard of accessibility to all the major units. My first task was to check the radiator level and this took only 10 seconds because of the external filler cap. Checking the engine oil level took 40 seconds, this including lifting and re-securing the near-side bonnet panel.
Combined filler and level plugs are provided in the main and auxiliary gearboxes and the rear axle, and all these have the same head, thus reducing the number of tools required for these three jobs to one. The levels were checked in 35, 40 and 40 seconds respectively.
A large oil-bath air cleaner is carried on the right hand of the scuttle and can be reached easily by lifting the offside bonnet. I was therefore able to check its level in 1-1 minutes, including opening and closing the bonnet. On this particular chassis the four 6-v. batteries were stowed under the mates' seat cushions and I was able to check the electrolyte levels in 3+ ,minutes, including removing and replacing the cushions. The batteries had rubber cell plugs and, as I have remarked before, these proved difficult to remove when they were covered with grease.
As an alternative to the under-seat stowage for the batteries they can be carried beneath the cab floor inboard of the step, although this position cannot be used when, as in the case of the test chassis, power steering is fitted, as the power ram occupies this space.
With the near-side bonnet panel lifted (6 seconds) I then removed the lower near-side panel in 18 seconds, this being simply secured by two wing nuts. This panel removed, a high degree of engine accessibility is obtained. After this .1 removed and replaced the main fuel-filter element, which is of the cloth type, in 11 minutes.
An injector change was then carried out, but because it is necessary to remove a rocker cover to gain access to any one of three injectors, I decided to remove the first three, , and this took me 12 minutes 23 seconds. The three injectors were then replaced in 10+ minutes.
The primary fuel filteris carried on the chassis frame under the left-hand cab floor boards, and can be reached by removing the detachable skirt panel which is secured by two budget locks. I removed and replaced the cloth element in 5 minutes 23 seconds, but this job would have been quicker had the filter cap been turned round when originally fitted, as its position as I found it made it difficult to get an open-ended spanner on the securing-bolt head.
Two spanners are required for the front brake adjustments as lock nuts are fitted, but by jacking up centrally under the axle .1 was able to adjust both brakes in 41 minutes. I jacked up each rear wheel separately because the vehicle was still laden, and adjusted both rear brakes in 31 minutes, thus showing the complete operation to be an 8-minute job, marred only by the fact that different spanners are necessary at front and rear brakes. •
The spare wheel is mounted at the rear of the chassis frame and supported by a winch-type carrier. Before the wheel can be lowered to the ground, however, it is necessary to remove three securing nuts which were not particularly easy to reach without a body and would definitely present difficulties when a body is fitted. Nevertheless I managed to dismount the wheel in 5+ minutes and restow it in 5 minutes 10 seconds.
Replacement of the near-side lower bonnet panel took minute and securing the hinged upper section took minute. The standard tool kit supplied with the Super Beaver is particularly comprehensive and includes a special tool for removing jammed injectors and another for compressing the valve springs to allow the collets to be detached. A well-written and fully illustrated instruction manual is supplied with each vehicle.