A New System of
Page 38
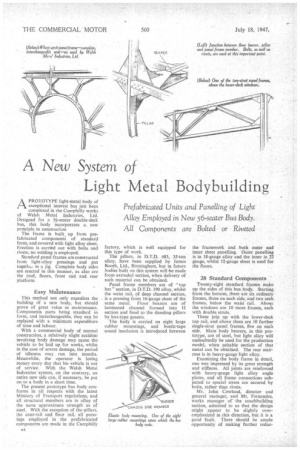
Page 39
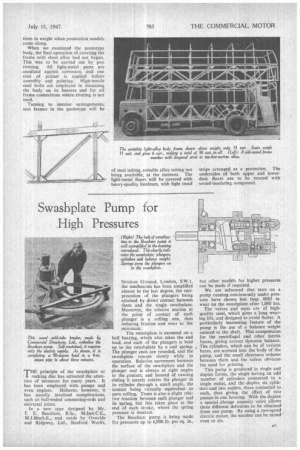
If you've noticed an error in this article please click here to report it so we can fix it.
Light Metal Bodybuilding
Prefabricated Units and Panelling of Light Alloy Employed in New 56-seater Bus Body. Al! Components are Bolted or Riveted APROTOTYPE light-metal body of exceptional interest has just been completed in the Caerphilly works of Welsh Metal Industries, Ltd. Designed fot a 56-seater double-deck bus, this body incorporates a, new principle in construction
The frame is built up from prefabricated components of standard form, and covered with light alloy sheet. Erection is carried out with bolts and rivets; no welding is employed.
Standard panel frames are constructed from light-alloy pressings and put togethr.,. in a jig. Complete body sides are erected in this manner, as also are the roof, floors, front end and rear platform.
Easy Maintenance
This method not only expedites the building of a new body, but should prove of great value in maintenance. Components parts being standard in form, and interchangeable, they can be replaced with a minimum expenditure of time and labour.
With a commercial body of normal construction, a relatively slight accident involving body damage may cause the vehicle to be laid up for weeks, whilst in the case of severe damage, the period of idleness may run into months. Meanwhile, the operator is losing money every day that his vehicle is out of service. With the Welsh Metal Industries system, on the contrary, an entire new side can, if necessary, be put on to a body in a short time.
The present prototype bus body conforms in all respects with the latest Ministry of Transport regulations, and all structural members are in alloy of the same approximate strength as of steel. With the exception of the pillars, the cant-rail and floor rail, all pressings emplbyed in the prefabricated components are made in the Caerphilly factory, which is well equipped for this type of work.
The pillars, in D.T.D. 683, 35-ton alloy, have been supplied by James Booth, Ltd., Birmingham, but in future bodies built on this system will be made from extruded section, when delivery of such material can be obtained.
Panel frame members are of " top hat" section, in D.T.D. 390 alloy, whilst the waist rail, of deep channel section, is a pressing from 16-gauge sheet of the same metal. Floor bearers are of laminated channel formed into H section and fixed to the Standing pillars by box-type gussets.
The body is carried on eight large rubber mountings, and bustic-tape sound insulation is introduced between the framework and both outer and inner sheet panelling. Outer panelling is in 18-gauge alloy and the inner in 22 gauge, whilst 12-gauge sheet is used for the floors.
28 Standard Components
Twenty-eight standard frames make up the sides of this bus body. Starting from the bottom, there are six ordinary frames, three on each side, and two arch frames, below the waist rail. Aboy,e the windows are 10 more frames, each with double struts.
These join up with the lower-deck top rail, and above them are 10 further single-strut panel frames, five on each side. Main body bearers, in this prototype, are of steel, but light alloy will undoubtedly be used for the production model, when suitable section of that metal can be obtained. The rear staircase is in heavy-gauge light alloy.
Examining the body frame in detail, one was impressed by its great strength and stiffness. All joints are reinforced with heavy-gauge light alloy angle plates, and all frame connections subjected to special stress are secured by bolts, rather than rivets.
Mr. John Cowland, director and general manager, and Mr. Fernandes, works manager of the coachbuilding section, admitted to us that the design might appear to be slightly overemphasized in this direction, but it is a good fault. There should be ample opportunity of making further redue tions in weight when production models come along.
When we examined the prototype body, the final operation of covering the frame with sheet alloy had not begun. This was to be carried out by pop riveting. All light-metal parts are anodized against corrosion, and one coat of primer is applied before assembly and painting. High-tensile steel bolts are employed in mounting the body on its bearers and for all frame connections where riveting is not used.
Turning to interior arrangements, seat frames in the prototype will be of steel tubing, suitable alloy tubing not being available, at the moment. The light-metal floors will be covered with heavy-quality linoleum, with light tread strips arranged as a protection. The undersides of both upper and lowerdeck floors are to be treated with sound-insulating compound.