MODERN METHODS OF BATTERY MAKING.
Page 50
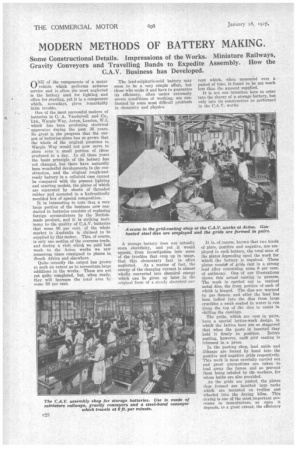
Page 51
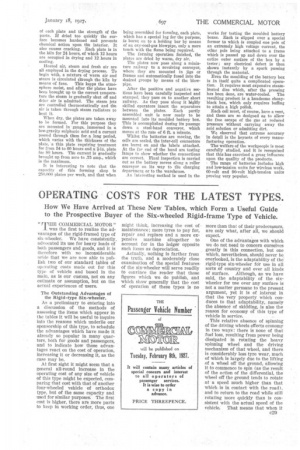
If you've noticed an error in this article please click here to report it so we can fix it.
Some Constructional Details. Impressions of the Works. Miniature Railways, Gravity Conveyors and Travelling Bands to Expedite Assembly. How the C.A.V. Business has Developed.
ONE of the components of a motor vehicle which performs arduous service and is often the most neglected is the battery used for lighting and often for starting, yet it is a component which, nowadays, gives remarkably little trouble.
One of the most successful makers of batteries is C. A. Vandervell and Co., Ltd., Warple Way, Acton, London, W.3, which has been producing electrical apparatus during the past 36 years. So great is the progress that the output of batteries alone has so grown that the whole of the original premises in W.arple Way would not now serve to store even a small portion of those produced in a day. In all these years the basic principle of the battery has not changed, but there have naturally been wonderful developments in the construction, and the original rough-andready battery in a celluloid case cannot be compared with the present lighting and starting models, the plates of which are separated by sheets of threaded rubber and mounted in a hydraulically moulded box of special composition.
It is interesting to note that a very large portion of the business now conducted in batteries consists of replacing foreign accumulators by the Britishmade product, and it is striking testimony to the quality of C.A.V. batteries that some 80 per cent, of the whole market in Australia is claimed to be supplied by this maker. This, of course, is only one section of the overseas trade, and during a visit which we paid last week to the Acton worlcs we saw numerous cases consigned to places in South Africa and elsewhere.
Quite recently the output has grown to such an extent as to necessitate large additions in the works. These are not yet quite completed, but, when ready, they will increase the total area by some 17)0 per cent. The lead-sulphuric-acid battery may seem to be a very simple affair, but those who make it and have to guarantee its efficiency, often under extremely severe conditions of working, are confronted by some most difficult problenls in chemistry and physics.
A storage battery does not actually store electricity, and yet it would appear, from investigation into some of the troubles that crop up in usage, that this elementary fact is often neglected. As a matter of fact, the energy of the charging current is almost wholly converted into chemical energy which can be given up later in the original form of a steady electrical cur rent which, when measuied over a Period of time, is found to be not much less than the amount supplied.
It is not our intention here to enter into the theory of a storage battery, but only into its construction as performed in the C.A.V. works.
It is, of course, known that two kinds of plate, positive and negative, are employed in each battery, the total area of the plates depending upoil the work for which the battery is required. These plates consist of grids cast in a strong lead alloy containing some 6 per cent. of antimony. One of our illustrations shows this actual casting in process. The work is carried out in vertical metal dies, the front portion of each of which is hinged. The dies are warmed hy gas flames, and after the lead has been ladled into the dies from large crucibles a swab soaked in water is run along the top of the dies to assist in chilling the castings.
The grids, which are cast in pairs, have a special lattice-work design, in which the lattice bars are so staggered that when the paste is inserted they hold it firmly in position. Before pasting, however, each grid casting is trimmed in a press.
In the pasting shop, lead oxide and litharge are forced by hand into • the positive and negative grids respectively. This work is most carefully carried out and great precautions are taken to lead away the fumes and so prevent them being inhaled by the workers, for whom baths are also provided.
As the grids are pasted, the plates thus formed are inserted into racks which are mounted On trollies and wheeled into the drying kilns. This drying is one of the most important processes in manufacture, as upon it depends, to a great extent, the efficiency
of each plate and the strength of the paste. If dried too quickly the surface becomes hardened and prevents chemical action upon the interior. It also causes cracking. Each plate is in the kiln for 24 hours, of which 12 hours are occupied in drying and 12 hours in cooling.
Heated air, steam and fresh air are all employed in the drying process. To begin with, a mixture of warm air and steam is circulated through the kiln by means of fans. This keeps the atmosphere moist, and after the plates have been brought up to the correct temperature the steam is gradually shut off and drier air is admitted. The steam jets are controlled thermostatically and the air is taken through steam radiators to heat it.
When dry, the plates are taken away to be formed. For this purpose they are mounted in gangs, immersed in a low-gravity sulphuric acid and a current passed through them for a long period, which varies with the thickness of the plate. a thin plate requiring treatment for from 54 to 60 hours and a /-in, plate for 80 hours. The current is gradually brought up from zero to .75 amp., which is the maximum.
It is interesting to note that the capacity of this forming shop is 250.000 plates per week, and that when
being assembled for forming, each plcte, which has a special lug for the purpose, is burnt on to a holding bar by means of an oxy-coal-gas blowpipe, only a mere touch with the flame being required.
The forming operation finished, the plates are dried by warm, dry air.
The plates now pass along a miniature railway to a revolving conveyor, where they are mounted in jigs or frames and automatically fused into the desired groups by means of the blowpipe.
After the positive and negative sections have been carefully inspected and stamped, they pass on to another short railway. As they pass along it highly skilled operators insert the separators between the plates. Each partly assembled unit is now ready to be mounted into its moulded battery box. This is accomplished during its passage down a steel-band conveyor, which moves at the rate of 6 ft. a minute.
Whilst the batteries are moving, the cells are sealed, the inter-cell connectors are burnt on and the labels attached. At the far end of the band are testing lamps to show whether the connections are correct. klinal inspection is carried out us the battery moves along a roller conveyor on its way to the charging department or to the warehouse.
An interesting method is used in the works for testing the moulded battery boxes. Each is slipped over a special former to which is coupled one pole of an extremely high voltage current, the other pole being attached to a frame which is passed up and down over the entire outer surface of the box by a tester; any electrical defect is then shown instantly by a spark passing through the material.
Even the moulding of the battery box is in itself quite a complicated operation. It requires most expensive steamheated dies which, after the pressing has been done, are water-cooled. The resulting product is a handsome ebonyblack box, which only requires buffing to attain a high polish.
Each cell must, of course, have a vent, and these are 90 designed as to allow the free escape of the gas at reduced !measure without carrying away the acid solution or admitting dirt.
We observed that extreme accuracy in detail is the keynote of every manufacturing operation.
The welfare of the workpeople is most carefully studied, and it is recognized that this has exercised a great influence upon the quality of the products.
• The range of batteries includes high and low-tension units for wireless work, 60-volt and 90-volt high-tension units proving very popular.