Switched on c
Page 48
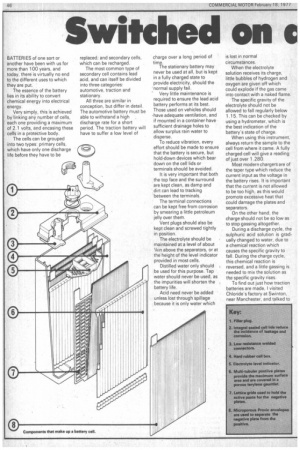
Page 49
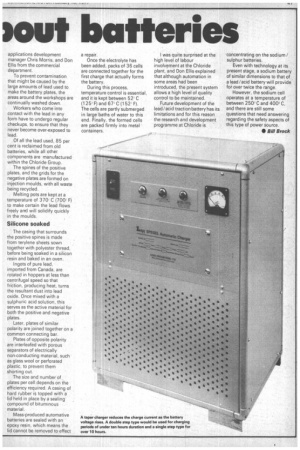
If you've noticed an error in this article please click here to report it so we can fix it.
'out batteries
BATTERIES of one sort or another have been with us for more than 100 years, and today, there is virtually no end to the different uses to which they are put.
The essence of the battery lies in its ability to convert chemical energy into electrical energy.
Very simply, this is achieved by linking any number of cells, each one providing a maximum of 2.1 volts, and encasing these cells in a protective body.
The cells can be grouped into two types: primary cells, which have only one discharge life before they have to be replaced; and secondary cells, which can be recharged.
The most common type of secondary cell contains lead acid, and can itself be divided into three categories: automotive, traction and stationary.
All three are similar in conception, but differ in detail. The automotive battery must be able to withstand a high discharge rate for a short period. The traction battery will have to suffer a low level of charge over a long period of time.
The stationary battery may never be used at all, but is kept in a fully charged state to provide electricity, should the • normal supply fail.
Very little maintenance is required to ensure the lead acid battery performs at its best. Those used on vehicles should have adequate ventilation, and if mounted in a container have sufficient drainage holes to allow surplus rain water to disperse.
To reduce vibration, every effort should be made to ensure that the battery is secure, but hold-down devices which bear down on the cell lids or terminals should be avoided.
It is very important that both the top face and the surround are kept clean, as damp and dirt can lead to tracking between the terminals.
The terminal connections can be kept free from corrosion by smearing a little petroleum jelly over them.
Vent plugs should also be kept clean and screwed tightly in position.
The electrolyte should be maintained at a level of about 1/4in above the separators, or at the height of the level indicator provided in most cells.
Distilled water only should I be used for this purpose. Tap water should never be used, as the impurities will shorten the battery life, Acid need never be added unless lost through spillage because it is only water which is lost in normal circumstances.
When the electrolyte solution receives its charge, little bubbles of hydrogen and oxygen are given off which could explode if the gas came into contact with a naked flame.
The specific gravity of the electrolyte should not be allowed to fall regularly below 1.15, This can be checked by using a hydrometer, which is the best indication of the battery's state of charge.
When using this instrument, always return the sample to the cell from where it came. A fully charged cell will give a reading of just over 1.280.
Most modern chargers are of the taper type which reduce the current input as the voltage in the battery rises. It is important that the current is not allowed to be too high, as this would promote excessive heat that could damage the plates and separators.
On the other hand, the charge should not be so low as to stop gassing altogether.
During a discharge cycle, the sulphuric acid solution is gradually changed to water, due to a chemical reaction which causes the specific gravity to fall. During the charge cycle, this chemical reaction is reversed, and a little gassing is needed to mix the solution as the specific gravity rises.
To find out just how traction batteries are made, I visited Chloride's factory at Swinton, near Manchester, and talked to applications development manager Chris Morris, and Don Ellis from the commercial department.
To prevent contamination that might be caused by the large amounts of lead used to make the battery plates, the areas around the workshops are continually washed down.
Workers who come into contact with the lead in any form have to undergo regular checkups, to ensure that they never become over-exposed to lead.
Of all the lead used, 85 per cent is reclaimed from old batteries, while all other components are manufactured within the Chloride Group.
The spines of the positive plates, and the grids for the negative plates are formed on injection moulds, with all waste being recycled.
Melting pots are kept at a temperature of 370 C (700 F) to make certain the lead flows freely and will solidify quickly in the moulds.
Silicone soaked
The casing that surrounds the positive spines is made from terylene sheets sown together with polyester thread, before being soaked in a silicon resin and baked in an oven.
Ingots of pure lead, imported from Canada, are rotated in hoppers at less than centrifugal speed so that friction, producing heat, turns the resultant dust into lead oxide. Once mixed with a sulphuric acid solution, this serves as the active material for both the positive and negative plates.
Later, plates of similar polarity are joined together on a common connecting bar.
Plates of opposite polarity are interleafed with porous separators of electrically non-conducting material, such as glass wool or perforated plastic, to prevent them shorting out.
The size and number of plates per cell depends on the efficiency required. A casing of hard rubber is topped with a lid held in place by a sealing compound of bituminous material.
Mass-produced automative batteries are sealed with an epoxy resin, which means the lid cannot be removed to effect a repair.
Once the electrolyte has been added, packs of 36 cells are connected together for the first charge that actually forms the battery.
During this process,
temperature control is essential, and it is kept between 52 C (125F) and 67C (152 F). The cells are partly submerged in large baths of water to this end. Finally, the formed cells are packed firmly into metal containers.
I was quite surprised at the high level of labour involvement at the Chloride plant, and Don Ellis explained that although automation in some areas had been introduced, the present system allows a high level of quality control to be maintained.
Future development of the lead/acid traction battery has its limitations and for this reason the research and development programme at Chloride is
.concentrating on the sodium / sulphur batteries.
Even with technology at its present stage, a sodium battery of similar dimensions to that of a lead/acid battery will provide for over twice the range.
However, the sodium cell operates at a temperature of between 250= C and 400= C, and there are still some questions that need answering regarding the safety aspects of this type of power source.
• BM Brock