Bogie still wearing well after 50 years
Page 63
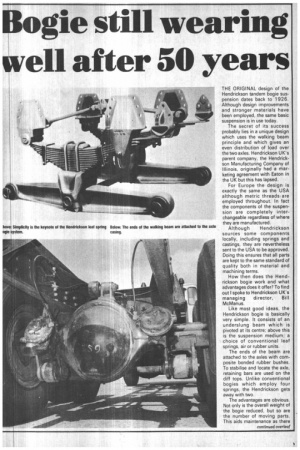
Page 64
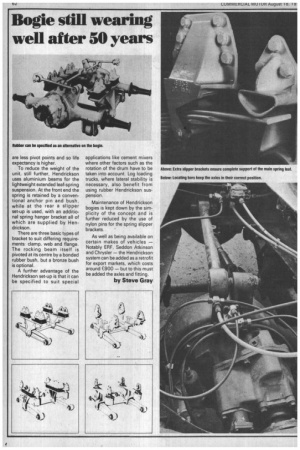
If you've noticed an error in this article please click here to report it so we can fix it.
THE ORIGINAL design of the Hendrickson tandem bogie suspension dates back to 1926. Although design improvements and stronger materials have been employed, the same basic suspension is in use today.
The secret of its success probably lies in a unique design which uses the walking beam principle and which gives an even distribution of load over the two axles. Hendrickson UK's parent company, the Hendrickson Manufacturing Company of Illinois, originally had a marketing agreement with Eaton in the UK but this has lapsed.
For Europe the design is exactly the same as the USA although metric threads are employed throughout. In fact the components of the suspension are completely interchangeable regardless of where they are manufactured.
Although Hendrickson sources some components locally, including springs and castings, they are nevertheless sent to the USA to be approved. Doing this ensures that all parts are kept to the same standard of quality both in material and machining terms.
How then does the Hendrickson bogie work and what advantages does it offer? To find out I spoke to Hendrickson UK's managing director, Bill McManus.
Like most good ideas, the Hendrickson bogie is basically very simple. It consists of an underslung beam which is pivoted at its centre; above this is the suspension medium; a choice of conventional leaf springs, air or rubber units.
The ends of the beam are attached to the axles with cornposite bonded rubber bushes. To stabilise and locate the axle, retaining bars are used on the cliff tops. Unlike conventional bogies which employ four springs, the Hendrickson gets away with two.
The advantages are obvious. Not only is the overall weight of the bogie reduced, but so are the number of moving parts. This aids maintenance as there are less pivot points and so life expectancy is higher.
To reduce the weight of the unit, still further, Hendrickson uses aluminium beams for the lightweight extended leaf-spring suspension. At the front end the spring is retained by a conventional anchor pin and bush, while at the rear a slipper set-up is used, with an additional spring hanger bracket all of which are supplied by Hendrickson.
There are three basic types of bracket to suit differing requirements clamp, web and flange. The rocking beam itself is pivoted at its centre by a bonded rubber bush, but a bronze bush is optional.
A further advantage of the Hendrickson set-up is that it can be specified to suit special applications like cement mixers where other factors such as the rotation of the drum have to be taken into account. Log loading trucks, where lateral stability is necessary, also benefit from using rubber Hendrickson suspension.
Maintenance of Hendrickson bogies is kept down by the simplicity of the concept and is further reduced by the use of nylon pins for the spring slipper brackets. '
As well as being available on certain makes of vehicles — Notably ERF, Seddon Atkinson and Chrysler — the Hendrickson system can be added as a retrofit for export markets, which costs around £900 — but to this must be added the axles and fitting.
by Steve Gray