LT tries out Active Ride
Page 48
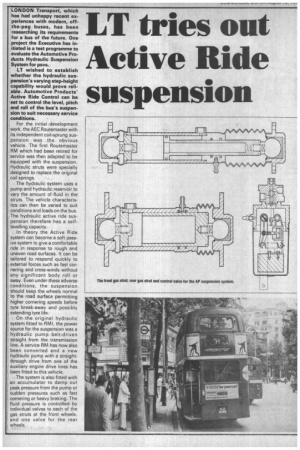
Page 49
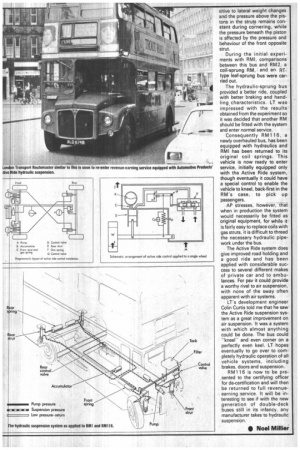
If you've noticed an error in this article please click here to report it so we can fix it.
suspension
LONDON Transport, which has had unhappy recent experiences with modern, offthe-peg buses, has been researching its requirements for a bus of the future. One project the Executive has initiated is a test programme to evaluate the Automotive Products Hydraulic Suspension System for psvs.
LT wished to establish whether the hydraulic suspension's varying step-height capability would prove reliable. Automotive Products' Active Ride Control can be set to control the level, pitch and roll of the bus's suspension to suit necessary service conditions.
For the initial development work, the AEC Routemaster with its independent coil-sprung suspension was the obvious vehicle. The first Routemaster RM which had been retired for service was then adapted to be equipped with the suspension. Hydraulic struts were specially designed to replace the original coil springs.
The hydraulic system uses a pump and hydraulic reservoir to vary the amount of fluid in the struts. The vehicle characteristics can then be varied to suit conditions and loads on the bus. The hydraulic active ride suspension therefore has a selflevelling capacity.
In theory the Active Ride system can become a soft passive system to give a comfortable ride in response to rough and uneven road surfaces. It can be tailored to respond quickly to . external forces such as fast cornering and cross-winds without any significant body roll or sway. Even under these adverse conditions, the suspension should keep the wheels normal to the road surface permitting higher cornering speeds before tyre break-away and possibly extending tyre life.
On the original hydraulic system fitted to RMI, the power source for the suspension was a hydraulic pump belt-driven straight from the transmission line. A service RM has now also been converted and a new hydraulic pump with a straightthrough drive from one of the auxiliary engine drive lines has been fitted to this vehicle.
The system is also fitted with an accumulator to damp out peak pressure from the pump or sudden pressures such as fast cornering or heavy braking. The fluid pressure is controlled by individual valves to each of the gas struts at the front wheels, and one valve for the rear wheels.
sitive to lateral weight changes and the pressure above the pistons in the struts remains constant during cornering, while the pressure beneath the piston is affected by the pressure and behaviour of the front opposite strut.
During the initial experiments with RMI, comparisons between this bus and RM2, a coil-sprung RM, and an RTtype leaf-sprung bus were carried out.
The hydraulic-sprung bus provided a better ride, coupled with better braking and handling characteristics. LT was impressed with the results obtained from the experiment so it was decided that another RM should be fitted with the system and enter normal service.
Consequently RMI 16, a newly overhauled bus, has been equipped with hydraulics and RMI has been returned to its original coil springs. This vehicle is now ready to enter service, initially equipped only with the Active Ride system, though eventually it could have a special control to enable the vehicle to kneel, back-first in the AM's case, to pick up passengers.
AP stresses, however, ihit when in production the system would necessarily be fitted as original equipment, for while it is fairly easy to replace coils with gas struts, it is difficult to thread the necessary hydraulic pipework under the bus.
The Active Ride system does give improved road holding and a good ride and has been applied with considerable success to several different makes of private car and to ambulances. For psv it could provide a worthy rival to air suspension, with none of the sway often apparent with air systems.
LT's development engineer Colin Curtis told me that he saw the Active Ride suspension system as a great improvement on air suspension. It was a system with which almost anything could be done. The bus could "kneel" and even corner on a perfectly even keel. LT hopes eventually to go over to completely hydraulic operation of all vehicle systems, including brakes, doors and suspension.
R M116 is now to be presented to the certifying officer for de-certification and will then be returned to full revenueearning service. It will be interesting to see if with the new generation of double-deck buses still in its infancy, any manufacturer takes to hydraulic suspension.
• Noel Millier