Out of sight shoulci not be out of mind
Page 44
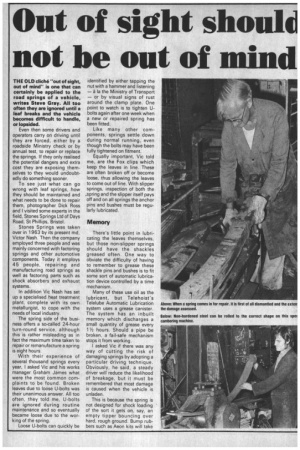
Page 45
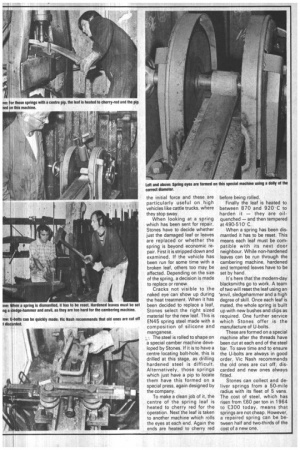
If you've noticed an error in this article please click here to report it so we can fix it.
THE OLD cliché "out of sight, out of mind" is one that can certainly be applied to the road springs of a vehicle, writes Steve Gray. All too often they are ignored until a leaf breaks and the vehicle becomes difficult to handle, or lopsided.
Even then some drivers and operators carry on driving until they are forced, either by a roadside Ministry check or by annual test, to repair or replace the springs. If they only realised the potential dangers and extra cost they are exposing .themselves to they would undoubtedly do something sooner.
To see just what can go wrong with leaf springs, how they should be maintained and what needs to be done to repair them, photographer Dick Ross and I visited some experts in the field, Stones Springs Ltd of Days Road, St Phillips, Bristol.
Stones Springs was taken over in 1963 by its present md, Victor Nash. Then the company employed three people and was mainly concerned with factoring springs and other automotive components. Today it employs 45 people, repairing and manufacturing road springs as well as factoring parts such as shock absorbers and exhaust systems.
In addition Vic Nash has set up a specialised heat treatment plant, complete with its own metallurgist, to cope with the needs of local industry.
The spring side of the business offers a so-called 24-hour turn-round service, although this is rather misleading as in fact the maximum time taken to repair or remanufacture a spring is eight hours.
With their experience of several thousand springs every year, I asked Vic and his works manager Graham James what were the most Common complaints to be found. Broken leaves due to loose U-bolts was their unanimous answer. All too often, they told me, U-bolts are ignored during routine maintenance and so eventually became loose due to the working of the spring.
Loose U-bolts can quickly be identified by either tapping the nut with a hammer and listening — a la the Ministry of Transport — or by visual signs of rust around the clamp plate. One point to watch is to tighten Ubolts again after one week when a new or repaired spring has been fitted.
Like many other components, springs settle down during normal running, even though the bolts may have been fully tightened on fitment.
Equally important, Vic told me, are the Fox clips which keep the leaves in line. These are often broken off or become loose, thus allowing the leaves to come out of line. With slipper springs, inspection of both the ,spring and the slipper itself pays off and on all springs the anchor pins and bushes must be regularly lubricated.
Memory
There's little point in lubricating the leaves themselves, but those non-slipper springs should have the shackles greased often. One way to obviate the difficulty of having to remember to grease these shackle pins and bushes is to fit some sort of automatic lubrication device controlled by a time mechanism.
Many of these use oil as the lubricant, but Telehoist's Telelube Automatic Lubrication system uses a grease canister. The system has an inbuilt memory which discharges a small quantity of grease every 11/2 hours, Should a pipe be broken, a fail-safe mechanism stops it from working.
I asked Vic if there was any way of cutting the risk of damaging springs by adopting a particular driving technique. Obviously, he said, a steady driver will reduce the likelihood of breakage, but it must be remembered that most damage is caused when the vehicle is unladen.
This is because the spring is not designed for shock loading of the sort it gets on, say, an empty tipper bouncing over hard, rough ground. Bump rubbers such as Aeon kits will take the initial force and these are particularly useful on high vehicles like cattle trucks, where they stop sway.
When looking at a spring which has been sent for repair, Stones have to decide whether just the damaged leaf or leaves are .replaced or whether the spring is beyond economic repair. First it is stripped down and examined. If the vehicle has been run for some time with a broken leaf, others too may be affected. Depending on the size of the spring, a decision is made to replace or renew.
Cracks not visible to the naked eye can show up during the heat treatment. When it has been decided to replace a leaf, Stones select the right sized material for the new leaf. This is EN45 spring steel made with a composition of silicone and manganese.
The steel is rolled to shape on a special camber machine developed by Stones. If it is to have a centre locating bolt-hole, this is drilled at this stage, as drilling hardened steel is difficult. Alternatively, those springs which just have a pip to locate them have this formed on a special press, again designed by the company.
To make a clean job of it, the centre of the spring leaf is heated to cherry red for the operation. Next the leaf is taken to another machine which rolls the eyes at each end. Again the ends are heated to cherry red before being rolled.
Finally the leaf is heated to between 870 and 920C to harden it — they are oilquenched — and then tempered at 490-510C.
When a spring has been dismantled it has to be reset. This means each leaf must be compatible with its next door neighbour. While non-hardened leaves can be run through the cambering machine, hardened and tempered leaves have to be set by hand.
Its here that the modern-day blacksmiths go to work. A team of two will reset the leaf using an 'anvil, sledgehammer and a high degree of skill. Once each leaf is mated, the whole spring is built up with new bushes and clips as required. One further service which Stones offer is the manufacture of U-bolts.
These are formed on a special machine after the threads have been cut at each end of the steel bar. To save time and to ensure the U-bolts are always in good order, Vic Nash recommends the old ones are cut off, discarded and new ones always fitted.
Stones can collect and deliver springs from a 50-mile radius with its fleet of 5 vans. The cost of steel, which has risen from £60 per ton in 1964 to £300 today, means that springs are not cheap. However, a repaired spring can be between half and two-thirds of the cost of a new one.