REDUCING THE
Page 16
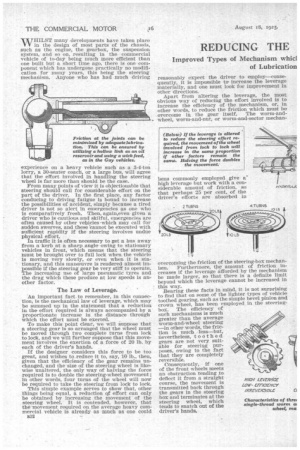
Page 17
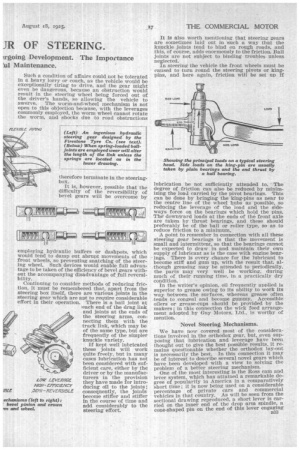
Page 18
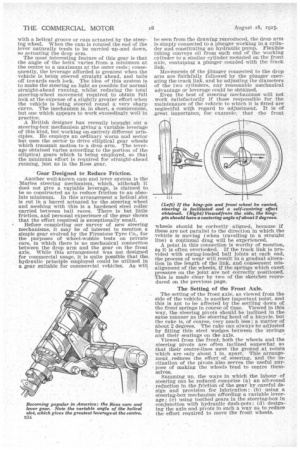
If you've noticed an error in this article please click here to report it so we can fix it.
JR OF 'STEERING.
WHILST many developments have taken place in the design of most parts of. the chassis, such as the engine, the gearbox, the suspension system, and so on, resulting in the commercial vehicle of to-day being much more efficient than one built but a short time ago, there is one component which has undergone practically no modification for many years, this being the steering mechanism. Anyone who has had much driving experience on a heavy vehicle such as a 3-4-ton lorry, a 30-seater coach, or a large bus, will agree that the effort involved in handling the steering wheel is far more than should be the case.
From many points of view it is objectionable that steering should call for considerable effort on the part of the driver. In the first place, any factor conducing to driving fatigue is bound to increase the possibilities of accident, simply because a tired driver is not so alert in emergencies as one who Is comparatively fresh. Then, again,even given a driver who is cautious and skilful, emergencies are often caused by other vehicles -which may call for sudden swerves, and these 'cannot be executed with sufficient rapidity if the steering involves undue physical effort.
In traffic it is often necessary to get a bus away from a kerb at a sharp angle owing to stationary vehicles in front, which means that the steering must be brought over to full lock when the vehicle Is moving very slowly, or even when it is stationary, and this inanceuvre is rendered almost impossible if the steering gear be very stiff to operate. The increasing use of large pneumatic tyres and the drag which these produce at low speeds is another factor.
An important fact-to remember, in this connection, is the mechanical law of leverage, which may be summed up in the statement that a reduction in the effort required is always accompanied by a proportionate increase in the distance through which the effort must be exerted.
To make this point clear, we will suppose that a steering gear is so arranged that the wheel must be moved through two complete turns from lock to lock, and we will further suppose that this movement involves the exertion of a force of 20 lb. by each of the driver's hands.
If the designer considers this force to be too great, and wishes to reduce it to, say, 10 lb., then, given that the efficiency of the gear remains unchanged, and the size of the steering wheel is likewise unaltered, the only way of halving the force required is to double the steering-wheel movement ; in other words, four turns of the wheel will now be required to• take the steering from lock to lock.
This simple example serves to show that, other things being equal, a reduction ef effort can only be obtained by increasing the movement of the steering wheel. It is contended, however, that the movementrequired on the average heavy commercial vehicle is already as much as one could B32 reasonably expect the driver to employ—consequently, it is impossible to increase the leverage materially, and one must look for improvement in other directions.
Apart from altering the leverage, the most obvious way of reducing the effort involved is to increase the efficiency of the mechanism, or, in other words, to reduce the friction which must be overcome in the gear itself. The worm-andwheel, worm-and-nut, or worm-and-sector median overcoming the friction of the steering-box mechanism. Furthermore, the amount of friction in creases if the leverage afforded by the mechanism be made larger, so that there is a definite limit beyond which the leverage cannot be increased in this way. Bearing these facts in mind, it is not surprising to find that on some of the lighter types of vehicle toothed gearing, such as the simple bevel pinion and crown wheel, has been employed in the steering box. The efficiency of such mechanisms is much greater than the average worm-and-wheel steering —in other words, the friction is much less—but, nevertheless, toothed gears are not very suitable for steering purposes, owing to the fact that they are completely reversible.
Consequently, if one of the front wheels meets an obstruction tending to deflect it from a straight course, the movement is transmitted back through the gears in the steering box and terminates at the steering wheel, which tends to snatch out of the driver's hands.
Such a condition of affairs could not be tolerated In a heavy lorry or coach, as the vehicle would be exceptionally tiring to drive, and the gear might even be dangerous, because an obstruction would result in the steering wheel being forced out of • the driver's hands, so allowing the vehicle to swerve. The worm-and-wheel mechanism is not open to this objection because, with the leverages commonly employed, the worm wheel cannot rotate the worm, and shocks due to road obstructions employing hydraulic buffers -or dashpets, which would tend to damp out abrupt movements of the front wheels, so preventing snatching of the steering wheel. Such devices would enable full advantage to be taken of the efficiency of bevel gears without the accompanying disadvantage of full reversibility.
Continuing to consider methods of reducing friction, it must be remembered that, apart from the steering box itself, there are various joints in the steering gear which are apt to require considerable effort in their operation. There is a ball joint at • each end of the drag link and joints at the ends of the steering arms, connecting them with the track link, which may be of the same type, but are frequently of the simpler knuckle Variety.
If kept well lubricated these joints will work quite freely, but in many cases lubrication has not been considered with sufficient care, either by the driver or by the manufacturers in the provision they have made for introducing oil to the joints ; consequently, the joints become stiffer and stiffer in the course of time and add considerably to the steering effort. It is also worth mentioning that steering gears are sometimes laid out in such a way that the knuckle joints tend to bind on rough roads, and this, of course, adds enormously to the friction. Ball joints are not subject to binding troubles unless neglected.
In steering the vehicle the front wheels must be caused to turn round the steering pivots or kingpins, and here again, friction will be set up if lubrication be not sufficiently attended to. The degree of friction can also be reduced by minimizing the load carried by the pivot bearings. This can be done by bringing the king-pins as near to the centre line of the wheel hubs as possible, so reducing the leverage of the load and the sideways force on the bearings which hold the pins. The downward loads at the ends of the front axle are taken by thrust bearings, and these should preferably be of the bail or roller type, so as to reduce friction to a minimum.
A point to remember in connection with all these steering gear bearings is that the movement is small and intermittent, so that the bearings cannot be expected to draw in and maintain their own supply of lubricant as is the case with engine bearings. There is every chance for the lubricant to become stiff and gum up, with the result that, although greasing may be attended to periodically, the parts may very well be working, during much of their running time, in a practically dry condition.
In the writer's opinion, oil frequently applied is superior to grease owing to its ability to work its way between the surfaces, whereas grease often -tends to congeal and become gummy. Accessible oilers or grease-cups should be provided by the makers ; in this connection the wick feed arrangement adopted by Guy Motors, Ltd., is worthy of mention.
Novel Steering Mechanisms.
We have now covered most of the considerations involved in the orthodox gear, but, even supposing that lubrication and leverage have been thought out to give the best possible results, it remains questionable whether the orthodox lay-out is necessarily the best. In this connection it may be of interest to describe several novel gears which have been developed with a view to solving the problem of a better steering mechanism.
One of the most interesting is the Ross cam and lever system, which has attained a remarkable degree of popularity in America in a comparatively short time ; it is now being used on a considerable percentage of private • cars and commercial vehicles in that country. As will be seen from the sectional drawing reproduced, a short lever is carried on the inner end of the drop arm spindle, a cone-shaped pin on the end of this lever engaging with a helical groove or cam actuated by the steering wheel. When the cam is rotated the end of the lever naturally tends to be carried up and down, so actuating the drop arm. The most interesting feature of this gear is that the angle of the helix varies from a minimum at the centre to a maximum at the outer ends consequently, the leverage afforded is greatest when the vehicle is beift steered straight ahead, and tails off towards each locl, The idea of this system is to make the steering as light as possible for normal straight-ahead running, whilst reducing the total steering-wheel movement required to obtain full lock at the expense of a slightly greater effort when the vehicle is being steered round a very sharp curve. The mechanism is, in short, a compromise, but one which appears to work exceedingly well in practice.
A British designer has recently brought out a steering-box mechanism giving a variable leverage of this kind, but working on entirely different principles. He employs an ordinary worm and sector but uses the sector to drive elliptical gear wheels which transmit motion, to a drop arm. The leverage obtained varies according to the portion of the elliptical gears which is being employed, so that the minimum effort is required for straight-ahead running, just as in the Ross gear.
Gear Designed to Reduce Friction.
Another well-known cam and lever system is the Manes steering mechanism„ which, although it does not give a variable leverage, is claimed to be so constructed as to reduce friction to an absolute minimum. In this arrangement a helical slot is cut in a barrel actuated by the steering wheel and meshing with this is a hardened steel roller carried between ball races. There is but little friction, and personal experience of the gear shows that the effort required is exceptionally small.
Before completing our survey of new steering mechanisms, it may be of interest to mention a simple gear evolved by the Firestone Tyre Co., for the purposes of wheel-wobble tests on private cars, in which there is no mechanical connection between the drop arm and the gear on the front axle. While this arrangement was not designed for commercial usage, it is quite possible that the hydraulic principle employed could be utilized in a gear suitable for commercial vehicles. As will be seen from the drawing reproduced, the drop arm is simply connected to a plunger working in a cylinder and constituting an hydraulic pump. Flexible tubing conveys oil from each end of the working cylinder to a similar cylinder mounted on the Vont axle, containing a plunger coupled with the track link.
Movements Of the Plunger connected to the drop arm are faithfully followed by the plunger operating the track link, and by adjusting the diameters of the two cylinders, any reasonable mechanical advantage or leverage could be obtained.
• Even the best of steering mechanisms will not , work Satisfactorily if those responsible for the maintenance of the vehicle to which it is fitted are • neglectful with regard to adjustment. It is of great importance, for example, that the front wheels should be cortectly aligned, because if these are not parallel to the direction in which the vehicle is moving (when travelling in a straight line) a continual drag will be experienced.
A point in thisconnection is worthy of mention, as it is often overlooked. If the track link is provided with spring-loaded ball joints at each end, the process of wear will result in a gradual alteration in the length of the link, and consequent misalignment of the wheels, if the springs which exert pressure on the joint are not correctly positioned. This is made clear by two of the sketches reproduced on the previous page.
The Setting of the Front Axle.
The setting of the front axle, as viewed from the side of the vehicle, is another important point, and this is apt to be affected by the settling down of the front springs in course of time. Viewed in this way, the steering pivots should be inclined in the same manner as the steering head of a bicycle, but the rake is, of course, very much less ; a matter of about 2 degrees. The rake can always be adjusted by fitting thin steel wedges between the 'springs and their seatings on the axle.
Viewed from the front, both the wheels and the steering pivots are often inclined somewhat so that their centre-lines meet the ground at points which are only about 1 in. apart. This arrangement reduces the effort of steering., and the inclination of the -pivots also serves the useful purpose of making the wheels tend to centre themselves.
Summing up. the ways in which the labour of steering can be reduced comprise (a) an all-round reduction in the. friction' of the gear by careful design and provision for. lubrication ; (b) using a steering-box mechanism affording a variable leverage ; (c) using toothed gears in the steering-box in conjunction with hydraulic dash-pots ; (d) designjug the axle and pivots in such a way as to reduce the effort required to move the front wheels.