For DRIVERS, MECHANICS & FOREMEN..
Page 21
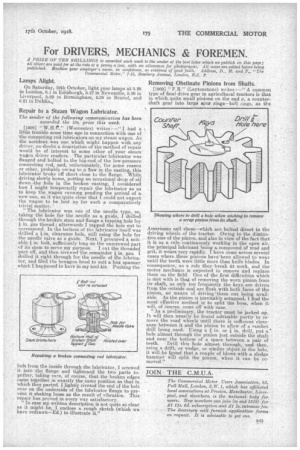
If you've noticed an error in this article please click here to report it so we can fix it.
A PRIZE OF TEN SHILLINGS is awarded each week to the sender of the best letter which we publish on this page ; all others are paid for at the rate oi a penny a has, with an allowance for photographs; All notes are edited before being published. Mention your employer's name, in confidence, as evidence of good faith. Address, D., 31. and F., "The Commercial Motor," 7-15, Rosebery Avenue, London, E.C. ti
Lamps Alight.
On Saturdayt 19th October, light your lamps at 5.28. in London, 6.1 in Edinburgh, 5.27 in Newcastle, 5.36 in Liverpool, 5.29 in Birmingham, 5.38 in Bristol, and 6.21 in Dublin
Repair to a Steam Wagon Lubricator.
The sender of the following communication has been awarded the 10s. prize this week.
[1908] "W .11e." (Worcester) writes :—" I had a 1. little trouble some time ago in connection with one of the connecting rod lubricators on my steam wagon. As the accident was one which might happen with any driver, no doubt a description of the method of repair would be of interest to some other of your steam wagon driver readers. The particular lubricator was flanged and bolted to the big-end of the low-pressure connecting rod, and, unfortunately, for .some reason or other, probably owing to a flaw in the casting, this lubricator broke off short close to the flange. While. driving slowly home, putting an occasional drop of oil down–the hole in the broken casting, I considered how I might temporarily repair the lubricator so as to keep the wagon running pending the arrival of a new one, as it was quite clear that I could not expect the wagon to be laid up for such a comparatively trivial matter. '
"The lubricator was one of the needle type, so, taking the hole tor the needle as a guide, I drilled through the broken stem and flange a tapping hole for t in. gas thread ; afterwards I tapped the hole out to correspond. In the bottom of the lubricator itself was drilled a t-in. clearance hole, still using the hole for the needle valve as a guide. Next, I procured a suitable in. bolt, sufficiently long on the unscrewed part of its stem to serve my purpose. I cut the threaded part off, and then screwed-the remainder tin. gas. I drilled it right through for the needle of the lubricator, and filed the hexagon head to suit a box spannerwhich I happened to have in my tool kit. Pushing the
bolt from the inside through the lubricator, I screwed it into the flange and tightened the two parts together, taking care, of course, that the broken edges came together in exactly the same position as that in which they parted. I lightly riveted the end of the bolt over on the underside of the lubricator flange to prevent it shaking loose as the result of vibration. This repair has proved in every way satisfactory. "In case my written description is not quite so clear as it might be, I enclose a rough sketch (which we have redrawn—Ed.) to illustrate it."
Removing Obstinate Pinions from Shafts.
[1909] " P.R." (Leytonstone) writes A common
type of final drive gear in agricultural tractors is that in which quite small pinions on the end c a countershaft gear into large apnr rings—bull rings, as the Americans call them—which are bolted direct to the driving wheels of the tractor. Owing to the diminutive size of the pinion, and also in view of the fact that it is as a rule continuously working in the open air, the principal lubricant being a compound of mud and grit, it wears very rapidly. I have come across several cases where these pinions havebeen allowed to wear until the teeth. were little more than knife blades. In consequence, as a rule they break at work, and the motor mechanio is expected to remove and replace them on the field. One of the first difficulties which is met with is that of removing. the worn pinion from its shaft, as only too frequently the keys are driven from the outside and are flush with both faces of the pinion, no means of driving 'them out being available. As the pinion is inevitably scrapped, I find the most effective method is to split the boss, when it will, of course, come off with ease.
"As a preliminary, the tractor must be jacked up. It will then usually be found advisable partly to remove the road wheels until there is sufficient clearance between it and the pinion to allow of a ratchet drill being used. Using a in. or in. drill, put a' hole almost through the pinion just outside the shaft and near the bottom of a space between a pair of teeth. Drill this hole almost through, andthen, using a drift, or wedge, or sirnilar object in the hole, it will be fond that a couple of blows with a sledge hammer will split the pinion, when it can be removed."