road and workshop
Page 43
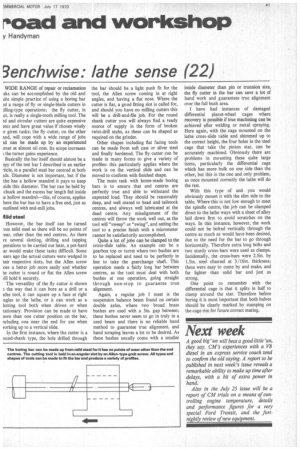
If you've noticed an error in this article please click here to report it so we can fix it.
y Handyman
9enchwise: lathe sense (22)
WIDE RANGE of repair or reclamation isks can be accomplished by the old and Ate simple practice of using a boring bar id a range of fly or single-blade cutters in illing-type operations.. the fly cutter, in ict, is really a single-tooth milling tool. The id and circular cutters are quite expensive ems and have great value if chosen wisely agiven tasks; the fly cutter, on the other and, will cope with a wide range of jobs id can be made up by an experienced irner at almost nil cost. Its scope increases ; the turner gains experience.
Basically the bar itself should almost be a )py of the test bar I described in an earlier • ie a parallel steel bar centred at both ids. Diameter is not important, but if the the has a hollow mandrel it pays to keep iside this diameter. The bar can be held by chuck and the excess bar length fed inside le hollow mandrel—this, of course, applies here the bar has to have a free end, just as outlined with end-mill jobs.
A ild steel
However, the bar itself can be turned -om mild steel as there will be no points of tear, other than the end centres. As there re several slotting, drilling and tapping perations to be carried out later, a pot-hard ar would make these tasks difficult. Some ears ago the actual cutters were wedged in heir respective slots, but the Allen screw oes a better job more easily and whether he cutter is round or flat the Allen screw Jill hold it securely.
The versatility of the fly cutter is shown the way that it can bore as a drill or a athe tool, it can square up a face at right .ngles to the lathe, or it can work as a lotting tool both when driven or when tationary. Provision can be made to have nore than one cutter position on the bar, ncluding one near the end for use when vorking up to a vertical slide.
In the first instance, where the cutter is a ound-shank type, the hole drilled through
the bar should be a light push fit for the tool, the Allen screw coming in at right angles, and having a flat nose. Where the cutter is flat, a good fitting slot is called for, and should you have no milling cutters this will be a drill-and-file job. For the round shank cutter you will always find a ready source of supply in the form of broken twist-drill stubs, as these can be shaped as required on the grinder.
Other shapes including flat facing tools can be made from soft cast or silver steel and finally hardened. The fly cutter can be made in many forms to give a variety of profiles: this particularly applies where the work is on the vertical slide and can be moved to conform with finished shape.
The main task with home-made boring bars is to ensure that end centres are perfectly true and able to withstand the expected load. They should be reasonably deep, and well mated to head and tailstock centres, and always well lubricated at the dead centre. Any misalignment of the centres will throw the work well out, as the tool will "sweep" or "swing", and setting the tool to a precise finish with a micrometer cannot be satisfactorily accomplished.
Quite a lot of jobs can be clamped to the cross-slide table. An example can be a gearbox top or turret where two bushes are to be replaced and need to be perfectly in line to take the gearchange shaft. This operation needs a fairly long bar between centres, as the tool must deal with both bushes at one operation, going straight through non-stop to guarantee true alignment.
Again, a regular job I meet is the suspension balance beam found on certain double axles, where two broad brass bushes are used with a 3in. gap between; these bushes never seem to go in truly in a used beam and there is no reliable hand method to guarantee true alignment, and hand scraping leaves a lot to be desired. As these bushes usually come with a smaller inside diameter than pin or trunnion size, the fly cutter in the bar can save a lot of hand work and guarantees true alignment over the full bush area.
I have had instances of damaged differential planet-wheel cages where recovery is possible if true machining can be achieved after welding or metal spraying. Here again, with the cage mounted on the lathe cross-slide table and shimmed up to the correct height, the four holes in the steel cage that take the pinion star, can be accurately machined. Obviously there are problems in mounting these quite large items, particularly the differential cage which has more bulk on one side than the other, but this is the one and only problem, as once mounted correctly the lathe will do the rest.
With this type of unit you would obviously mount it with the slim side to the table. Where this is not low enough to meet the spindle centre, the job can be clamped direct to the lathe ways with a sheet of alloy laid down first to avoid scratches on the ways. In this instance, however, the work could not be bolted vertically through the centre as much as would have been desired, due to the need for the bar to go through horizontally. Therefore extra long bolts and two sturdy cross-bars were used as clamps. Incidentally, the cross-bars were 2.5in. by 1.5in. steel channel at '3 /16in. thickness; these were easy to come by and make, and far lighter than solid bar and just as strong.
One point to remember with the differential cage is that it splits in half to clamp around the star. Therefore before boring it is most important that both halves should be clearly marked by stamping on the cage rim for future correct mating.