Reclaiming Used Oil a Double Economy
Page 46
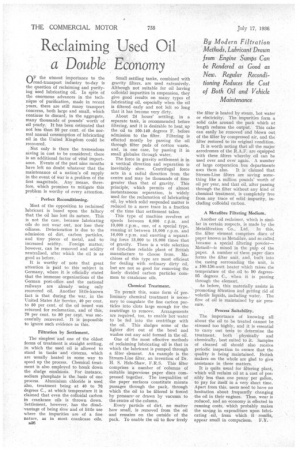
If you've noticed an error in this article please click here to report it so we can fix it.
By Modern Filtration Methods, Lubricant Drawn from Engine Sumps Can be Rendered as Good as New. Regular Reconditioning Reduces the Cost of Both Oil and Vehicle Maintenance
nF the utmost importance to the %.-/road-transport industry to-day is the question of reclaiming and purifying used lubricating oil. In spite of the enormous advances in the technique of purification, made in recent years, there are still many transport concerns, both large and small, which continue to discard, in the aggregate, many thousands of pounds' worth of oil yearly: It has been estimated that not less than 50 per cent, of the normal annual consumption of lubricating oil in the United Kingdom could be recovered.
Not only is there the tremendous saving in cost to be considered; there is an additional factor of vital importance. Events of the past nine months have left no doubt whatever that the maintenance of a nation's oil supply in the event of war is a problem of the first magnitude. Any means, therefore, which promises to mitigate this problem is worthy of every attention.
Perfect Reconditioning.
Most of the opposition to reclaimed lubricant is based upon the fallacy that the oil has lost its nature. This is not the case, because lubricating oils do not wear out, nor lose their oiliness. Deterioration is due to the admission of dirt, carbon particles, and tiny pieces of metal, and to increased acidity. Foreign matter; however, can be removed and acidity neutralised, after which the oil is as good as before.
It is worthy of note that great attention is paid to this subject in Germany, where it is officially stated that the immense organizations of the German post-office and the national railways are already using only recovered oil. Another little-known fact is that during the war, in the United States Air Service, 40 per cent. to 50 per cent, of the oil issued was returned for reclamation, and of this, 70 per cent. to 80 per cept. was successfully recovered. It is impossible to ignore such evidence as this.
Filtration by Settlement.
The simplest and one of the oldest forms of treatment is straight settling, in which the used oil is allowed to stand in tanks and cisterns, which are usually heated in some way to speed up the process. Chemical treatment is also employed to break down the sludge emulsions. For instance, sodium phosphate is the basis of one process. Aluminium chloride is used also, treatment being at 40 to 70 degrees C., at which temperature it is claimed that even the colloidal carbon in crankcase oils is thrown down. Settlement, however, has the disad-vantage of being slow and of little use where the impurities are of a fine nature, as in most crankcase oils. Small settling tanks, combined with gravity filters, are used extensively. Although not suitable for oil having colloidal impurities in suspension, they give good results on many types of lubricating oil, especially when the oil is filtered early and not left so long that it has become very dirty.
About 24 hours' settling, in a separate tank, is recommended before filtering, and it is desirable to heat up the oil to 100-140 degrees F. before admission to the filter. Filtering is effected mostly by passing the oil through filter pads of cotton waste, and, in one case, by passing it in small globules through water.
The force in gravity settlement is in a vertical direction and separation is inevitably slow. Centrifugal force acts in a radial direction from the centre and may be thousands of tune greater than that of gravity. This principle, which permits of almost instantaneous separation, is widely used for the reclamation of lubricating oil, by which solid suspended matter is reduced to a mere trace in a fraction of the time that settlement takes.
This type of machine revolves at speeds between 6,000 r.p.m. and 10,000 r.p.m., one, of a special type, running at between 15,000 r.p.m. and 16,000 r.p.m. and exerting a separating force 13,000 to 15,000 times that of gravity. There is a wide selection of first-class reliable plant of British manufacture to choose from. Machines of this type are most efficient for dealing with ordinary dirty oil, but are not so good for removing the finely divided carbon particles common to crankcase oils.
Chemical Treatment.
To permit this, some form Of preliminary chemical treatment is necessary to coagulate the fine carbon particles into clots large enough for the centrifuge to remove. Arrangements are required, too, to enable hot water to be fed into the centrifuge with the oil. This sludges some of the lighter dirt out of the bowl and washes out any acid formed in the oil.
One of the most effective methods of reclaiming lubricating oil is that in which the lubricant is pumped through a filter element. An example is the Stream-Line filter, an invention of Dr. H. S. Hele-Shaw, F.R.S. This filter comprises a number of columns of suitable impervious paper discs compressed together. The inequalities of the paper surfaces constitute minute passages through the pack, through which the oil to be filtered is forced by pressureor drawn by vacuum to the centre of the column.
Every particle of dirt, no matter how small, is removed from the oil and remains on the outside of the pack. To enable the oil to flow freely • the filter is heated by steam, hot water or electricity. The impurities form a solid cake around the pack which at length reduces the output. This cake can easily be removed and blown out of the filter by compressed air, and the filter restored to its original condition.
It is worth noting that all the major aerodromes of the R.A.F. are equipped with these filters whereby oil can be used over and over again. A number of large corporation bus departments uses them also. It is claimed that Stream-Line filters are saving something like a million pounds' worth of oil per year, and that oil, after passing through the filter without any kind of chemical treatment, is completely free from any trace of solid impurity, including colloidal carbon.
A Metafibre Filtering Medium.
Another oil reclaimer, which is similar in certain respects, is made by the Metafiltration Co., Ltd. In this, the filter element comprises discs of paper known as Metafibre, and so called because a special filtering powderMetasilis mixed in the pulp of the paper. A number of these paper discs forms the filter unit, and, built into the casing surrounding the unit, is a 100-150-watt heater which raises the temperature of the oil to 90 degrees:A degrees C., When it is passing through the element. .
As before, this materially assists in promoting filtration and getting rid of volatile liquids, including water. The flow of oil is maintained by air pressure.
Procesi Suitability.
The importance of knowing all about the oil to be treated cannot be stressed too highly, and it is essential to carry out tests to determine the treatment, both physically and chemically, best suited to it. Samples of cleaned oil should also receive periodic inspection to. ensure that the quality is being maintained. British makers on the whole are glad to give assistance in these matters.
It is quite usual for filtering plant, which will reclaim oil at a cost of possibly less than one penny per gallon, to pay for itself in a very short time. Apart from this, users need to have no hesitation about frequently changing the oil in their engines. Thus, wear is reduced, and an economy is effected in running costs, which probably makes the saving in expenditure upon lubricating oil, from which it results, appear small in comparison. F.Y.