The 'construction and use'
Page 44
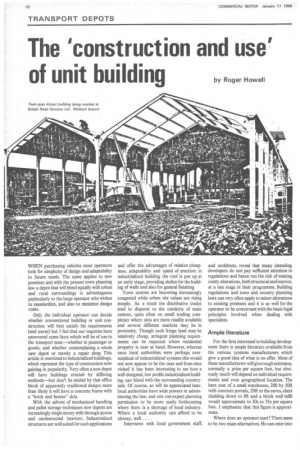
Page 45
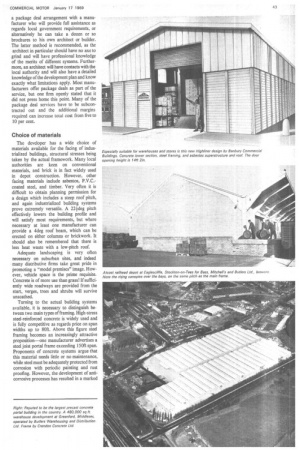
Page 46
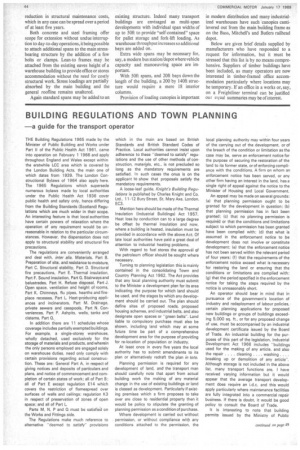
If you've noticed an error in this article please click here to report it so we can fix it.
of unit building by Roger Howell
WHEN purchasing vehicles most operators look for simplicity of design and adaptability to future needs. The same applies to new premises and with the present town planning law a depot that will blend equally with urban and rural surroundings is advantageous particularly to the large operator who wishes to standardize, and also to minimize design costs.
Only the individual operator can decide whether conventional building or unit construction will best satisfy his requirements (and purse) but I feel that our inquiries have uncovered some facts which will be of use to the transport man—whether in passenger or goods, and whether contemplating a whole new depot or merely a repair shop. This article is restricted to industrialized buildings, which represent the type of construction now gaining in popularity. Very often a new depot will have buildings erected by differing methods—but don't be misled by that office block of apparently traditional design; more than likely it will have a concrete frame with a "brick and breeze" skin.
With the advent of mechanized handling and pallet storage techniques new depots are increasingly single storey with through access and unobstructed interiors. Industrialized structures are well suited for such applications and offer the advantages of relative cheapness, adaptability and speed of erection: in industrialized building the roof is put up at an early stage, providing shelter for the building of walls and also for general finishing Town centres are becoming increasingly congested while urban site values are rising steeply. As a result the distributive trades tend to disperse to the outskirts of main centres, quite often on small trading complexes where sites are more readily available and several different markets may be in proximity. Though such fringe land may be relatively cheap, stringent planning requirements can be expected where residential property is near at hand. However, whereas once local authorities were perhaps oversceptical of industrialized systems this would not now appear to be the case and from sites visited it has been interesting to see how a well-designed, low profile industrialized building can blend with the surrounding countryside. Of course, as will be appreciated later, local authorities have wide powers in administering the law, and one can expect planning permission to be more easily forthcoming where there is a shortage of local industry. Where a local authority can afford to be choosy, well . .
Interviews with local government staff, and architects, reveal that many intending developers do not pay sufficient attention to regulations and hence run the risk of making costly alterations, both structural and interior, at a late stage in their programme. Building regulations and town and country planning laws can very often apply to minor alterations to existing premises and it is as well for the operator to be conversant with the basic legal principles involved when dealing with specialists.
Ample literature For the firm interested in building development there is ample literature available from the various systems manufacturers which give a good idea of what is on offer. Most of these manufacturers will give rough estimates, normally a price per square foot, but obviously much will depend on individual requirements and even geographical location. The bare cost of a small warehouse, 200 by 50ft with concrete portals, 20ft to the eaves, sheet cladding down to 811 and a block wall infill would approximate to 30s to 35s per square foot. I emphasize that this figure is approximate.
Where does an operator start? There seem to be two main alternatives. He can enter into a package deal arrangement with a manufacturer who will provide full assistance as regards local government requirements, or alternatively he can take a dozen or so brochures to his own architect or builder. The latter method is recommended, as the architect in particular should have no axe to grind and will have professional knowledge of the merits of different systems. Furthermore, an architect will have contacts with the local authority and will also have a detailed knowledge of the development plan and know exactly what limitations apply. Most manufacturers offer package deals as part of the service, but one firm openly stated that it did not press home this point. Many of the package deal services have to be subcontracted out and the additional margins required can increase total cost from five to 10 per cent.
Choice of materials The developer has a wide choice of materials available for the facing of industrialized buildings, structural stresses being taken by the actual framework. Many local authorities are keen on conventional materials, and brick is in fact widely used in depot construction. However, other facing materials include asbestos, P.V.C.coated steel, and timber. Very often it is difficult to obtain planning permission for a design which includes a steep roof pitch, and again industrialized building systems prove extremely versatile. A 22+deg pitch effectively lowers the building profile and will satisfy most requirements, but where necessary at least one manufacturer can provide a 4deg roof beam, which can be erected on either columns or brickwork. It should also be remembered that there is less heat waste with a low-pitch roof.
Adequate landscaping is very often necessary on suburban sites, and indeed many distributive firms take great pride in promoting a "model premises" image. However, vehicle space is the prime requisite. Concrete is of more use than grass! If sufficiently wide roadways are provided from the start, verges, trees and shrubs will survive unscathed.
Turning to the actual building systems available, it is necessary to distinguish between two main types of framing. High-stress steel-reinforced concrete is widely used and is fully competitive as regards price on span widths up to 80ft. Above this figure steel framing becomes an increasingly attractive proposition—one manufacturer advertises a steel joist portal frame exceeding 150ft span. Proponents of concrete systems argue that this material needs little or no maintenance, while steel must be adequately protected from corrosion with periodic painting and rust proofing. However, the development of anticorrosive processes has resulted in a marked reduction in structural maintenance costs, which in any case can be spread over a period of at least five years.
Both concrete and steel framing offer scope for extension without undue interruption to day-to-day operations, it beingpossible to attach additional spans to the main stressbearing structure by the addition of a few bolts or clamps. Lean-to frames may be attached from the existing eaves height of a warehouse building to provide office or stores accommodation without the need for costly structural work. Stress loadings are partially absorbed by the main building and the general roofline remains unaltered.
Again standard spans may be added to an
existing Structure. Indeed many transport buildings are envisaged as multi-span developments with individual span widths of up to 50ft to provide "self-containedspace for pallet storage and fork-lift loading. As warehouse throughput increases so additional bays are added on.
Extra wide spans may be necessary for, say, a modern bus station/depot where vehicle capacity and manoeuvring space are important.
With 50ft spans, and 20ft bays down the length of the building, a 200 by 140ft structure would require a mere 18 interior columns.
Provision of loading canopies is important in modern distribution and many industrialized warehouses have such canopies cantilevered out from the main building frame as on the Bass, Mitchell's and Butlers railhead depot.
Below are given brief details supplied by manufacturers who have responded to a request for information, but it must be stressed that this list is by no means comprehensive. Suppliers of timber buildings have been included, as many operators are now interested in timber-framed office accommodation particularly where locations may be temporary. If an office in a works or, say, on a Freightliner terminal can be justified our eq ual summaries may be of interest.