Our new series gleans the secrets and habits of top
Page 36
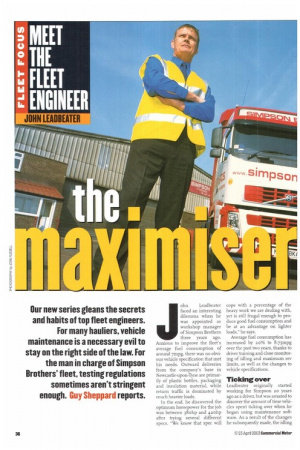
Page 37
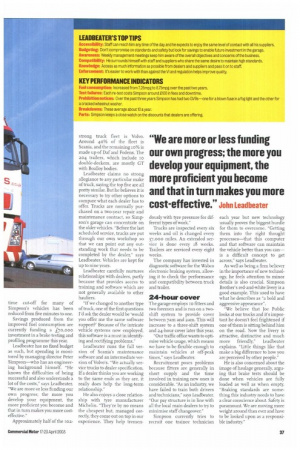
If you've noticed an error in this article please click here to report it so we can fix it.
fleet engineers. For many hauliers, vehicle maintenance is a necessary evil to stay on the right side of the law. For the man in charge of Simpson Brothers' fleet, testing regulations sometimes aren't stringent enough. Guy Sheppard reports.
ohn Leadbeater faced an interesting dilemma when he was appointed as workshop manager of Simpson Brothers three years ago.
Anxious to improve the fleet's average fuel consumption of around 7mpg, there was no obvious vehicle specification that met his needs. Outward deliveries from the company's base in Newcastle-upon-Tyne are primarily of plastic bottles, packaging and insulation material, while return traffic is dominated by much heavier loads.
In the end, he discovered the optimum horsepower for the job was between 38ohp and 42ohp after trying several different specs. "We know that spec will cope with a percentage of the heavy work we are dealing with, yet is still frugal enough to produce good fuel consumption and be at an advantage on lighter loads," he says.
Average fuel consumption has increased by zo% to 8.75mpg over the past two years, thanks to driver training and close monitoring of idling and maximum rev limits, as well as the changes to vehicle specifications.
Ticking over
Leadbeater originally started working for Simpson zo years ago as a driver, but was amazed to discover the amount of time vehicles spent ticking over when he began using maintenance software. As a result of the changes he subsequently made, the idling time cut-off for many of Simpson's vehicles has been reduced from five minutes to one.
Savings produced from the improved fuel consumption are currently funding a ko,000 investment in a brake testing and profiling programme this year.
Leadbeater has no fixed budget as such, but spending is monitored by managing director Peter Simpson—who has an engineering background himself. "He knows the difficulties of being successful and also understands a lot of the costs," says Leadbeater. "We are more or less funding our own progress; the more you develop your equipment, the more proficient you become and that in turn makes you more costeffective."
Approximately half of the roz
strong truck fleet is Volvo. Around 40% of the fleet is Scania, and the remaining ro% is made up of Daf and Fodens. The 204 trailers, which include to double-deckers, are mostly GT with Boalloy bodies.
Leadbeater claims no strong allegiance to any particular make of truck, saying the top five are all pretty similar. But he believes it is necessary to try other options to compare what each dealer has to offer. Trucks are normally purchased on a two-year repair and maintenance contract, so Simpson's garage can concentrate on the older vehicles. "Before the last scheduled service, trucks are put through our own workshop so that we can point out any outstanding work that needs to be completed by the dealer," says Leadbeater. Vehicles are kept for up to nine years.
Leadbeater carefully nurtures relationships with dealers, partly because that provides access to training and software which are not generally available to other hauliers.
"If we changed to another type of truck, one of the first questions I'd ask the dealer would be 'would you offer me the same software support?' Because of the intricate vehicle systems now employed, this software is a must in identifying and rectifying problems."
Leadbeater runs the full version of Scania's maintenance software and an intermediate version of Volvo's. "We actually service trucks to dealer specification. If a dealer thinks you are working to the same ends as they are, it really does help the long-term relationship."
He also enjoys a close relationship with tyre manufacturer Michelin. "They're by no means the cheapest but, managed correctly, they come out on top in our experience. They help tremen
dously with tyre pressure for different types of work."
Trucks are inspected every six weeks and oil is changed every 37,000 miles. An extended service is done every 18 weeks. Trailers are serviced every eight weeks.
The company has invested in diagnostic software for the Wabco electronic braking system, allowing it to check the performance and compatibility between truck and trailer.
24-hour cover
The garage employs ro fitters and two foremen and is run on a twoshift system to provide cover between 7am and zam. This will increase to a three-shift system and 24-hour cover later this year.
"Our traffic office wants to optimise vehicle usage, which means we have to be flexible enough to maintain vehicles at off-peak times," says Leadbeater.
Recruitment poses problems because fitters are generally in short supply and the time involved in training new ones is considerable. "As an industry, we have failed to train both drivers and technicians," says Leadbeater. "Our pay structure is in line with all the local main dealers to try to minimise staff changeover."
Simpson currently tries to recruit one trainee technician each year but new technology usually proves the biggest hurdle for them to overcome. "Getting them into the right thought processes—that this computer and that software can maintain the vehicle better than you can— is a difficult concept to get across," says Leadbeater.
As well as being a firm believer in the importance of new technology, he feels attention to minor details is also crucial. Simpson Brother's red-and-white livery is a good example. This used to have what he describes as "a bold and aggressive appearance".
"We believe that Joe Public looks at our trucks and it's important he doesn't feel frightened if one of them is sitting behind him on the road. Now the livery is attractive, distinctive and much more friendly," Leadbeater explains. "Little things like that make a big difference to how you are perceived by other people."
He is also concerned about the image of haulage generally, arguing that brake tests should be done when vehicles are fully loaded as well as when empty. "Braking standards are something this industry needs to have a clear conscience about. Safety is paramount. We are moving more weight around than ever and have to be looked upon as a responsible industry."