The hard times arE a'changing bodyworli
Page 18
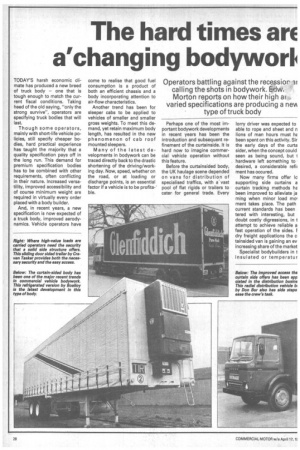
Page 19
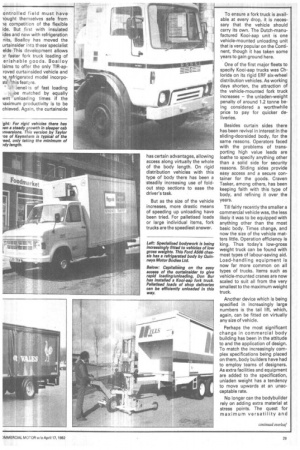
Page 20

If you've noticed an error in this article please click here to report it so we can fix it.
Operators battling against the recessior calling the shots in bodywork. Eidm Morton reports on how their high al varied specifications are producing a neNA type of truck body
TODAY'S harsh economic climate has produced a new breed of truck body — one that is tough enough to match the current fiscal conditions. Taking heed of the old saying, "only the strong survive", operators are specifying truck bodies that will last.
Though some operators, mainly with short-life vehicle policies, still specify cheaper bodies, hard practical experience has taught the majority that a quality specification pays off in the long run. This demand for premium specification bodies has to be combined with other requirements, often conflicting in their nature. Increased versatility, improved accessibility and of course minimum weight are required in virtually every order placed with a body builder.
And, in recent years, a new specification is now expected of a truck body, improved aerodynamics. Vehicle operators have come to realise that good fuel consumption is a product of both an efficient chassis and a body incorporating attention to air-flow characteristics.
Another trend has been for sleeper cabs to be applied to vehicles of smaller and smaller gross weights. To meet this demand, yet retain maximum body length, has resulted in the new phenomenon of cab roof mounted sleepers.
Many of the latest developments in bodywork can be traced directly back to the drastic shortening of the driving/working day. Now, speed, whether on the road, or at loading or discharge points, is an essential factor if a vehicle is to be profitable. Perhaps one of the most important bodywork developments in recent years has been the introduction and subsequent refinement of the curtainside. It is hard now to imagine commercial vehicle operation without this feature.
Before the curtainsided body, the UK haulage scene depended on vans for distribution of specialised traffics, with a-vast pool of flat rigids or trailers to cater for general trade. Every
lorry driver was expected to able to rope and sheet and n lions of man hours must ha been spent on this activity. Sir the early days of the culla sider, when the concept could seen as being sound, but hardware left something to• desired, a considerable refii ment has occu red.
Now many firms offer lc supporting side curtains a curtain tracking methods ha been improved to alleviate ja ming when minor load ma+ ment takes place. The path current standards has been tered with interesting, but doubt costly digressions, in t attempt to achieve reliable a fast operation of the sides. F dry freight applications the c tainsided van is gaining an ev increasing share of the market Specialist bodybuilders in t insulated or temperatur
ontrolled field must have iought themselves safe from le competition of the flexible ide. But first with insulated ides and now with refrigeration nits, Boalloy has moved the urtainsider into these'specialist elds This development allows )r. faster fork truck loading of erishable goods. Boalloy laims to offer the only TIR-aproved curtainsided vehicle and le. rpfrigerated model incorpo
3te fear.ire.
)enelf is of fast loading
-ue matched by equally win 'unloading times if the laximum productivity is to be chieved. Again, the curtainside has certain advantages, allowing access along virtually the whole of the body length. On rigid distribution vehicles with this type of body there has been a 'steadily increasing use of foldout step sections to ease the driver's task.
But as the size of the vehicle increases, more drastic means of speeding up unloading have been tried. For palletised loads or large individual items, fork trucks are the speediest answer. To ensure a fork truck is available at every drop, it is necessary that the vehicle should carry its own. The Dutch-manufactured Kooi-aap unit is one vehicle-mounted unloading unit that is very popular on the Continent, though it has taken some years to gain ground here.
One of the first major fleets to specify Kooi-aap trucks was Chloride on its rigid ERF six-wheel distribution vehicles. As working days shorten, the attraction of the vehicle-mounted fork truck increases — the unladen-weight penalty of around 1.2 tonne being considered a worthwhile price to pay for quicker deliveries.
Besides curtain sides there has been revival in interest in the sliding-doorsided body, for the same reasons. Operators faced with the problems of transporting high value leads are loathe to specify anything other than a solid side for security reasons. Sliding sides provide easy access and a secure container for the goods. Craven Tasker, among others, has been keeping faith with this type of body, and refining it over the years.
Till fairly recently the smaller a commercial vehicle was, the less likely it was to be equipped with anything other than the most basic body. Times change, and now the size of the vehicle matters little. Operation efficiency is king. Thus today's low-gross weight truck can be found with most types of labour-saving aid. Load-handling equipment is now far more common on all types of trucks. Items such as vehicle-mounted cranes are now scaled to suit all from the very smallest to the maximum weight truck.
Another device which is being specified in increasingly large numbers is the tail lift, which, again, can be fitted on virtually any size of vehicle.
Perhaps the most significant change in commercial body building has been in the attitude to and the application of design. To match the increasingly complex specifications being placed on them, body builders have had to employ teams of designers. As extra facilities and equipment are added to the specification, unladen weight has a tendency to move upwards at an unacceptable rate, No longer can the bodybuilder rely on adding extra material at stress points. The quest for maximum versatility and minimum unladen weight demands that the bodybuilder prepares an engineered, stressed design, rather than "design" as he builds.
Where the maximum payload within a given gross weight is required, the designer's efforts are crucial if a durable, yet light structure is to result. With the likely increase in gross weights many operators are specifying vehicles now for use later at the new weights. However, with the haulage industry as competitive as it is, these operators do not wish to sacrifice any payload at today's gross weights, and thus pose a difficult problem to the bodybuilder.
Specialist companies, such as We[ford and Don Bur, have produced a wide variety of bulk body designs with all-alloy construction, including the chassis, in the course of gaining maximum payload. With this type of construction and material a careful, properly stressed design stage is even more vital.
In other areas, truck operators are demanding the maximum from their vehicles. As the driving day is shortened, the chance of being unable to make a round trip in a day increases. This affects rigids as well as artics and has resulted in a growth in demand for sleeper cabs for the non-articulated vehicle. Standard sleeper cabs, generally designed primarily for the larger tractor units in the truck manufacturers range, are wasteful of bodylength when applied to a rigid.
Thus there has been a steady business by many bodybuilders in converting day cabs to sleepers, by adding the minimum extra depth to the standard cab shell.
The latest twist to this theme is the cab top sleeper which does not impinge on the length available for payload. First seen on the continent, this type of conversion is now made by many companies in the UK. The cab-top mounted pod also has a beneficial side effect in that it generally improves the vehicles aerodynamics.
Rising fuel prices have ensured that bodybuilders have had to pay more attention to this aspect of design. Chassis manufacturers have improved the aerodynamics of their cabs and bodybuilders have responded with a variety of own-design bulkhead mounted deflectors and have started to pay more attention to details such as rounding corner pillars.
While body design continues to advance, there is still room in the modern transport scene for some older ideas. Three-way tipping bodies are once again returning to favour after many years of neglect. The advantages of this type of body are very relevant given today's traffic. The ability to tip material at the roadside, yet keep traffic obstruction to a minimum, is the strength of this type of tipper. Modern hydraulics and scientifically designed. subframes should ensure that the new breed of three-way tipper is a more practical tool than in the past.