A one-piece wheel and tyre?
Page 38
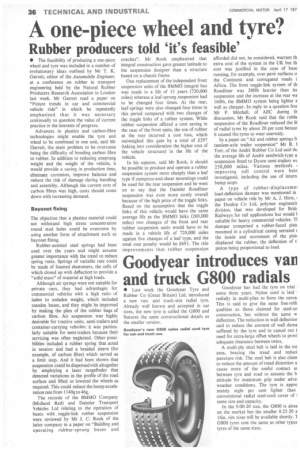
If you've noticed an error in this article please click here to report it so we can fix it.
Rubber producers told 'it's feasible'
• The feasibility of producing a one-piece wheel and tyre was included in a number of evolutionary ideas outlined by Mr T. K. Garrett, editor of the Automobile Engineer, at a conference on rubber in transport engineering held by the Natural Rubber Producers Research Association in London last week. Mr Garrett read a paper on "Future trends in car and commercial .vehicle ride" in which he repeatedly emphasized that it was necessary continually to question the value of current practice in the interests of progress.
Advances in plastics and carbon-fibre technologies might enable the tyre and wheel to be combined in one unit, said Mr Garrett, the main problem to be overcome being the difficulty of bonding carbon fibre to rubber. In addition to reducing unsprung weight and the weight of the vehicle, it would provide a saving in production time, eliminate corrosion, improve balance and reduce the risk of damage during handling and assembly. Although the current cost of carbon fibres was high, costs should come down with increasing demand.
Bayonet fixing The objection that a plastics material could not withstand high stress concentration round stud holes could be overcome by using another form of attachment such as bayonet fixing.
Rubber-assisted steel springs had been used over the years and might assume greater importance with the trend to reduce spring rates. Springs of variable rate could be made of foamed elastomers, the cells of which closed up with deflection to provide a "solid mass" of material at high loads. , Although air springs were not suitable for private -cars, they had advantages for commercial vehicles with a high ratio of laden to unladen weight, which included standee buses, and they might be improved by making the plies of the rubber bags of carbon fibre. Air suspension was highly desirable for tractive units, semi-trailers and container-carrying vehicles; it was particularly suitable for semi-trailers because their servicing was often 'neglected. Other possibilities included a rubber spring that acted in tension and had a braided sleeve (for example, of carbon fibre) which served as a limit stop. And it had been shown that suspension could be dispensed with altogether by employing a laser rangefinder that detected variations in the profile of the road surface and lifted or lowered the wheels as required. This could reduce the bump acceleration rate from 1140g to 46g.
The records of the BMMO Company (Midland Red) and Daimler Transport Vehicles Ltd relating to the operation of buses with, toggle-link rubber suspension were reviewed by Mr J. C. Rook of the latter company in a paper on "Building and operating rubber-sprung buses and coaches". Mr Rook emphasized that integral construction gave greater latitude to the suspension designer than a structure based on a chassis frame.
One replacement of the independent front suspension units of the BMMO integral bus was made in a life of 15 years (720,000 miles) whereas a leaf-sprung suspension had to be changed four times. At the rear, leaf-springs were also changed four times in this period compared with two changes of the toggle links of a rubber system. While rubber suspension offered a cost saving in the case of the front units, the use of rubber at the rear incurred a cost loss, which outweighed this gain by a total of £297 (taking into consideration the higher cost of the vehicle structure) in the life of the vehicle.
In his opinion, said Mr Rook, it should be possible to produce and operate a rubber suspension system more cheaply than a leaf type if compress-and-shear mountings could be used for the rear suspension and he went on to say that the Daimler Roadliner suspension was even more costly overall because of the high price of the toggle links. Based on the assumption that the toggle links of this vehicle would have the same average life as the BMMO links (260,000 miles) two changes of the front and rear rubber suspension units would have to be made in a vehicle life of 720,000 miles against five changes of a leaf type, and the total cost penalty would be £691. The ride improvements that rubber suspension
afforded did not, he considered, warrant th extra cost of the system in the UK but th cost was justified in the case of buse running, for example, over pave surfaces o the Continent and corrugated roads i Africa. The front toggle-link system of th Roadliner was 2801b heavier than letsuspension and the increase at the rear wa 1601b, the BMMO system being lighter a well as cheaper. In reply to a question fror Mr P. Mitchell, of AEC during th discussion, Mr Rook said that the rubbc suspension of the Roadliner reduced the lil of radial tyres by about 20 per cent becalm it caused the tyres to wear unevenly.
In a paper on "Air and rubber springs ft tandem-axle trailer suspension" Mr R. 1 Torr, of the Andre Rubber Co Ltd said thi the average life of Andre sandwich-type a suspension fitted to Dyson semi-trailers wf 250,000 miles. Various methods improving roll control were bein investigated, including the use of intern bump stops.
A type of rubber-displacemei load-deflection damper was mentioned in paper on vehicle ride by Mr A. J. Hirst, the Dunlop Co Ltd, polymer engineerir division, that was developed for Brill Railways for rail applications but would 1 suitable for heavy commercial vehicles. TI damper comprised a rubber-faced pistc mounted in a cylindrical casing serrated c the inside and movement of the pistc displaced the rubber, the deflection of t! piston being proportional to load.