THE MAKING OF BATTERIES for Moto Vehicles
Page 54
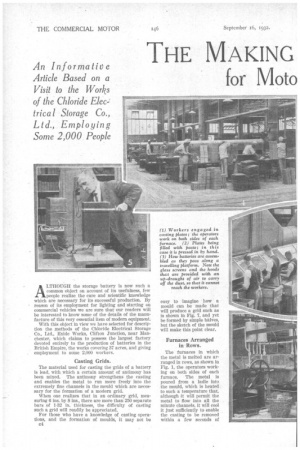
Page 55
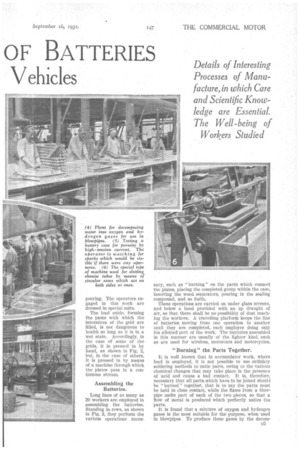
Page 56

If you've noticed an error in this article please click here to report it so we can fix it.
ALTHOUGH the storage battery is now such a common object on account of its usefulness, few people realize the care and scientific knowledge which are necessary for its successful production. By reason of its employment for lighting and starting on commercial vehicles we are sure that our readers will be interested to know some of the details of the manufacture of this very essential item of modern equipment.
With this object in view we have selected for description the .methods of the Chloride Electrical Storage Co., Ltd., Exide Works, Clifton Junction, near Manchester, which claims to possess the largest factory devoted entirely to the production of batteries in the British Empire, the works covering 37 acres, and giving employment to some 2,000 workers.
Casting Grids.
The material used for casting the grids of a battery is lead, with which a certain amount of antimony has been mixed. The antimony strengthens the casting and enables the metal to run more freely into the extremely tine channels in the mould which are necessary for the formation of a modern grid.
When one realizes that in an ordinary grid, measuring 6 ins. by 8 ins., there are more than 250 separate bars of 1-32 in. thickness, the difficulty of casting such a grid will readily be appreciated.
For those who have a knowledge of casting operations, and the formation of moulds, it may not be c4 easy to imagine how a mould can be made that will produce a grid such as is shown in Fig. 7, and yet be formed by simple halves, but the sketch of the mould Will make this point clear.
Furnaces Arranged in Rows.
The furnaces in which the metal is melted are arranged in rows, as shown in Fig. 1, the operators working on both sides of each furnace. The metal is poured from a ladle into the mould, which is heated to such a temperature that, although it will permit the metal to flow into all the minute channels, it will cool it just sufficiently to enable the casting to be removed within a few seconds of pouring. The operators engaged in this work are dressed in special suits.
The lead oxide, forming the paste with which the interstices of the grid are filled, is not dangerous to health so long as it is in a wet state. Accordingly, in the case of some of the grids, it is pressed in by hand, as shown in Fig. 2, but, in the case of others, it is pressed in by means of a machine through which the plates pass in a continnous stream.
Assembling the Batteries.
Long lines of as many as 20 workers are employed in assembling the batteries. Standing in rows, as shown in Fig. 3, they perform the various operations neces sary, such as " burning " on the parts which connect the plates, placing the completed group within the case, inserting the wood separators, pouring in the sealing compound, and so forth.
These operations are carried on under glass screens, and below a hood provided with an up draught of air, so that there shall be no possibility of dust reaching the workers. A travelling platform keeps the line of batteries moving from one operation to another until they are completed, each employee doing only his allotted part of the work. The batteries assembled in this manner are usually of the lighter kind, such as are used for wireless, motorcars and motorcycles.
"Burning" the Parts Together.
It is well known that in accumulator work, where lead is employed, it is not possible to use ordircary soldering methods to unite parts, owing to the various chemical changes that may take place in the presence of acid and cause a bad contact. It is, therefore, necessary that all parts .which have to be joined should be " burned" together, that is to say the parts must be held in close contact, while the flame from a blowpipe melts part of each of the two pieces, so that a flow of metal is produced which perfectly unites the parts.
It is found that a mixture of oxygen and hydrogen gases is the most suitable for the purpose, when used in blowpipes. To produce these gases by the decomc5 posing of water into its two elements, the plant shown in Fig. 4 is employed.
That a battery case should have no minute pores through which the electrolyte can escape will readily be appreciated by all users. To detect such minute pores, however, is not an easy matter, as no great pressure can be exerted from within, as in the system used for pneumatic tyres, in which bubbles are produced to indicate porosity. The acid in the electrolyte, however, is very searching, and will, in time, find its • way through t h e smallest aperture.
The, test which has proved to be the most reliable is an electric one, as illustrated in Fig. 5. A battery case is placed over a block of metal, which approximately his it, and the block is connected to one pole of a high-tension electric circuit. The other pole of this circuit is connected to a metal frame, which is slightly larger than the ease under test. In parallel with this circuit there is a spark gap of approximately 1 in., across which a continuous stream of sparks passes. The distance between the frame and the internal block is considerably less than 1 in., consequently, as the operator passes the frame down over the ease, should there be any aperture, no matter how minute, a spark will jump through it, and the continual stream between the two points an inch apart will stop. The spark coming from the block inside, through the case to the frame, indicates exactly the spot where the fault lies.
The Making of Exide-Ironclad Batteries.
The Exide-Ironclad battery is a speciality of the Chloride Electrical Storage Co., Ltd., and is designed especially for bus lighting and starting service and for use in electrically propelled vehicles. The name Ironclad merely signifies somethina that is not easily damaged, no iron being used in the construction.
It differs from the ordinary battery in that the positive plate is formed as illustrated above, the positive plate being composed of a number of rods cast integral with the piece across the top. Each rod has many fins that hold concentrically an ebonite tube which encases them, the space between the rod and tube being filled with the active material. To ensure access of the electrolyte to the active material the ebonite tubes are provided with a large number of slits, each slit being so fine as to prevent any possibility of the escape of the active material. The slitting of the tubes is carried out by special machines, one of which is shown in Fig. 6. Two thin circular saws attack the tube from each side; the machines work automatically. The active material, in powder form, is introduced mechanically between the rod and the slotted ebonite tube.
The battery, when complete, consists of a positive plate, as described, and a negative plate of standard Exide construction. Between these plates is placed a wood separator, the ebonite tube taking the place of the z= usual slotted ebonite
dia
phragm, as used in some other forms of battery.
In the handling of lead, especially in the form of its oxides in the powder state, there is always a danger of the workers contracting lead poisoning. At the works of the Chloride Electrical Storage Co., Ltd., the most minute precautions are taken to reduce to a minimum any possibility of the workers suffering illeffects of this kind. These precautions go far beyond those laid down by the Board of Trade, and vary in their strictness according to the nature of the work upon which the men are engaged.
Health Precautions for the Workers.
No smoking or eating during working hours is permitted, in case food or cigarettes might be contaminated. On some operations respirators have to be worn, and extractors are at work carrying away any dust, the floors being kept continually flooded to prevent dust from rising in those shops where such precautions are needed. Certain of the workers, as previously mentioned, are provided with a complete working suit, and when leaving work they have to change entirely and take a bath. In addition, each man is provided with a tooth brush, which he has to use over a jet of water. As an extra precaution each worker has to rub a compound into his hands to prevent lead from entering the pores of his skin. This compound is manufactured by the Exide company, and is known as " Rozalex,"
A medical staff is always in attendance, consisting of a doctor, a nurse, and a dentist. Blood tests and microscopic examinations of samples are made at regular intervals, and, in short, no pains whatever seem to be spared to ensure the health of the workers. Purthermore, their welfare on the social side is also keenly provided for, by the provision of spacious recreation grounds adjacent to the works.