Handle with care
Page 36
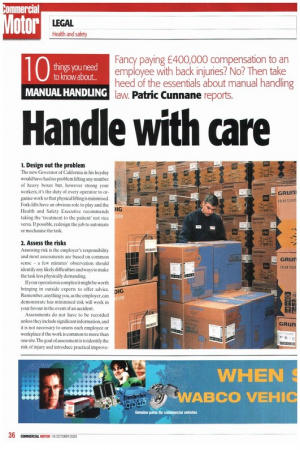
Page 37
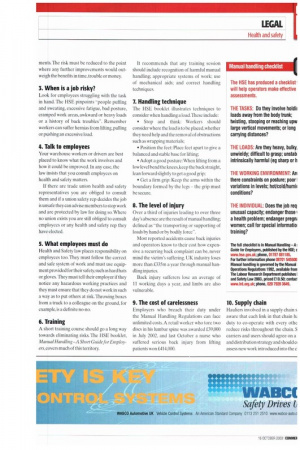
If you've noticed an error in this article please click here to report it so we can fix it.
1. Design out the problem The new Governor of California in his heyday would have had no problem lifting any number of heavy boxes but, however strong your workers, it's the duty of every operator to organise work so that physical lifting is minimised. Fork-lifts have an obvious role to play and the Health and Safety Executive recommends taking the 'treatment to the patient' not vice versa. If possible, redesign the job to automate or mechanise the task.
2. Assess the risks Assessing risk is the employer's responsibility and most assessments are based on common sense — a few minutes' observation should identify any likely difficulties and ways to make the task less physically demanding.
If your operation is complex it might be worth bringing in outside experts to offer advice. Remember, anything you, as the employer.can demonstrate has minimised risk will work in your favour in the event of an accident.
Assessments do not have to be recorded unless they include significant information,and it is not necessary to assess each employee or workplace if the work is common to more than one site.The goal of assessment is to identify the risk of injury and introduce practical improve ments. The risk must be reduced to the point where any further improvements would outweigh the benefits in time, trouble or money.
3. When is a job risky?
Look for employees struggling with the task in hand. The HSE pinpoints "people puffing and sweating, excessive fatigue, had posture, cramped work areas, awkward or heavy loads or a history of back troubles". Remember workers can suffer hernias from lifting, pulling or pushing an excessive load.
4. Talk to employees Your warehouse workers or drivers are best placed to know what the work involves and how it could be improved. In any case, the law insists that you consult employees on health and safety matters.
If there are trade union health and safety representatives you are obliged to consult them and if a union safety rep decides the job is unsafe they can advise members to stop work and are protected by law for doing so. Where no union exists you are still obliged to consult employees or any health and safety rep they have elected.
5. What employees must do Health and Safety law places responsibility on employees too. They must follow the correct and safe system of work and must use equipment provided for their safety.such as hard hats or gloves. They must tell their employer if they notice any hazardous working practices and they must ensure that they do not work in such a way as to put others at risk.Throwing boxes from a truck to a colleague on the ground, for example. is a definite no-no.
6. Training A short training course should go a long way towards eliminating risks. The HSE booklet, Manual Handling—A Short Guide for Employers,covers much of this territory. It recommends that any training session should include recognition of harmful manual handling; appropriate systems of work; use of mechanical aids; and correct handling techniques.
7. Handling technique The 11SL booklet illustrates techniques to consider when handling a load.These include: • Stop and think: Workers should consider where the load is to be placed,whether they need help and the removal of obstructions such as wrapping materials; • Position the feet: Place feet apart to give a balanced and stable base for lifting; • Adopt a good posture: When lifting from a low level bend the knees, keep the back straight, lean forward slightly to get a good grip; • Get a firm grip: Keep the arms within the boundary formed by the legs — the grip must be secure.
8. The level of injury Over a third of injuries leading to over three day's absence are the result of manual handling; defined as "the transporting or supporting of loads by hand or by bodily force".
Most reported accidents cause back injuries and operators know to their cost how expensive a recurring back complaint can be, never mind the victim's suffering. UK industry loses more than £335m a year through manual handling injuries.
Back injury sufferers lose an average of II working days a year. and limbs are also vulnerable.
9. The cost of carelessness Employers who breach their duty under the Manual Handling Regulations can face unlimited costs. A retail worker who tore two discs in his lumbar spine was awarded L39,000 in July 2002. and last October a nurse who suffered serious back injury from lifting patients won £414,000. 10. Supply chain Hauliers involved in a supply chain s aware that each link in that chain hi duty to co-operate with every othe reduce risks throughout the chain. S carriers and users should agree on a and distribution strategy and should cl assess new work introduced into the c