Designing for Lightness
Page 94
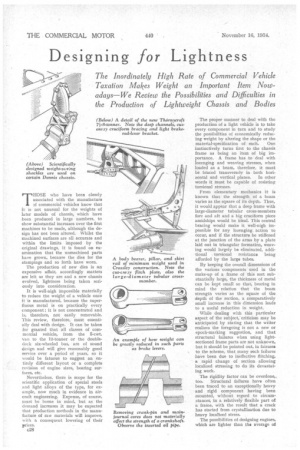
Page 95
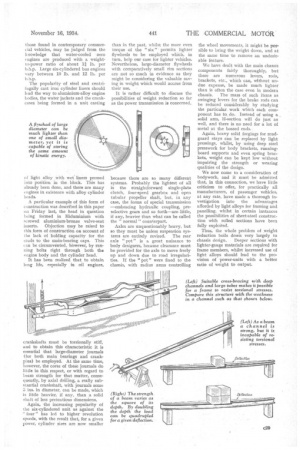
If you've noticed an error in this article please click here to report it so we can fix it.
The Inordinately High Rate of Commercial Vehicle Taxation Makes Weight an Important Item Nowadays—We Review the Possibilities and Difficulties in the Production of Lightweight Chassis and Bodies
THOSE who have been clesely associated with the manufacture of commercial vehicles know that it is not unusual for the weights of later models of chassis, which have been produced in large numbers, to show substantial increases over the first machines to be made, although the design has not been altered. Whilst the machined surfaces are all accurate and within the limits imposed by the original drawings, it is found on examination that the unmachined parts have grown, because the dies for the stampings and so forth have worn.
The production of new dies is an expensive affair, accordingly matters are left as they are and a new chassis evolved, lightness being taken seriously into consideration.
It is well-nigh impossible materially to reduce the weight of a vehicle once it is manufactured, because the superfluous metal is on practically every component ; it is not concentrated and is, therefore, not easily removable. This review, therefore, must essentially deal with design. It can be taken for granted that all classes of commercial vehicle, from the 5-cwt. van to the 12-tonner or the doubledeck six-wheeled bus, are of sound design and will give reasonably good service over a period of years, so it would be fatuous to suggest an entirely different layout or a complete revision of engine sizes, bearing surfaces, etc.
Nevertheless, there is scope for the scientific application of special steels and light alloys of the type, for example, now much in evidence in aircraft engineering. Expense, of course, must be borne in mind, but as the demand increases it may be expected that production methods in the manufacture of raw materials will improve, with a consequent lowering of their prices.
c28
The proper manner to deal with the production of a light vehicle is to take every component in turn and to study the possibilities of economically reducing weight by altering the shape or the
material-specification of each. One instinctively turns first to the chassis frame as being an item of big importance. A frame has to deal with lozenging and weaving stresses, when loaded as a beam, therefore, it must be braced transversely in both horizontal and vertical planes. In other words it must be capable of resisting torsional stresses.
From elementary mechanics it is known that the strength of a beam varies as the square of its depth. Thus, it would appear that a deep frame with large-diameter tubular cross-members fore and aft and a big cruciform piece amidships would be ideal. This central bracing would make it well-nigh impossible for any lozenging action to occur, and if the structure be stiffened at the junction of the arms by a plate laid out in triangular formation, weaving would largely he eliminated, additional torsional resistance being afforded by the large tubes.
By keeping the overall dimensions of the various -components used in the make-up of a frame of this sort substantially large, the thickness of metal can be kept small so that, bearing in mind the relation that the beam strength varies as the square of the -depth of the section, a comparatively small increase in this dimension leads to a useful reduction in weight.
While dealing with this particular aspect of the subject, criticism may be anticipated by stating that the writer realizes the foregoing is not a new or epoch-marking suggestion, and that structural failures when using lightsectioned frame parts are not unknown, but it should be pointed out, in fairness to the scheme, that many such failures have been due to ineffective flitching, a rapid change of section allowing localized stressing to do its devastating work.
The rigidity factor can be overdone,,
too. Structural failures have often been traced to an exceptionally heavy and rigid component having been mounted, without regard to circumstances, in a relatively flexible part of a frame, with the result that a crack has started from crystallization due to heavy localized stress.
The possibilities of-designing engines, which are lighter than the average of
those found in contemporary commercial vehicles, may be judged from the knowledge that water-cooled aero engines are produced with a weightto-power ratio of about 11 lb. per b-h.p. Large six-cylindered bus engines vary between 10 lb. and 12 lb. per b. h.p.
The popularity of steel and centrifugally cast iron cylinder liners should lead the way to aluminium-alloy engine bodies, the water jackets and the crankcases being formed in a unit casting ef light alloy with wet' liners pressed into position in the block. This has already been done, and there are many engines in existence with alloy cylinder heads.
A particular example of this form of construction was described in this paper on Friday last, the head in question being formed in bliduminium with screwed aluminium-bronze valve-seat inserts. Objection may be raised to this form of construction cis account of the lack of holding capacity for the studs to the main-bearing caps. This can be circumvented, however, by running bolts right through both ties engine body and the cylinder head.
It has been realized that to obtain long life, especially in oil engines, crankshafts must be torsionally stiff, and to obtain this characteristic it is essential that large-diameter journals (for both main bearings and crankpins) be employed. At the same time, however, the cores of these journals do little in this respect, or with regard to beam strength for that matter, consequently, by axial drilling, a really substantial crankshaft, with journals some 3 ins, in diameter, can be made, which is little heavier, if any, than a solid shaft of less pretentious dimensions.
Again, -the increasing popularity of the six-cylindered unit as against the " four " has led to higher revolution speeds, with the result that, for a given power, cylinder sizes are now smaller than in the past, whilst the more even torque of the " six " • permits lighter flywheels to be employed which, in turn, help our case for lighter vehicles. Nevertheless, large-diameter flywheels with comparatively small rim sections are not so much in evidence as the might be considering the valuable saving in weight which would accrue from their use.
It is rather difficult to discuss the possibilities of weight reduction so far as the power transmission is concerned, because there are so many different systems. Probably the lightest of all is the straightforward single-plate clutch, four-speed gearbox and open tubular propeller shaft, but, in any case, the forms of special transmission —embracing hydraulic coupling, preselective gears and so forth—are-little, if any, heavier than what can be called the " normal" counterpart.
Axles are unquestionably heavy, hut so they must be unless suspension sys tems are entirely revised. The rear axle " pot " is a great nuisance to body designers, because clearance must be provided for the axle to move freely up and down due to road irregularities. If the "pot" were fixed to the chassis, with radius arms controlling
the wheel movements, it might be possible to bring the weight down, and at the same time to remove an undesirable feature.
We have dealt with the main chassis components fairly thoroughly, but there are numerous levers, rods, brackets, etc., which can, without undue expense, be made much lighter than is often the case even in modern chassis. The mass of such items as swinging levers for the brake rods can be reduced considerably, by studying the particular work which each component has to do. Instead of using a solid arm, H-section will do just as well, and there is no need for a lot of metal at the bossed ends.
Again, heavy solid forgings for mudguard stays can be replaced by light pressings, whilst, by using deep steel presswork for body brackets, runningboard supports and even spring brackets, weight can be kept low without impairing the strength or wearing qualities of the design.
We now come to a consideration of bodywork, and it must be admitted that, in this connection, we have little criticism to offer, for practically all manufacturers, of passenger vehicles, at any rate, have made a thorough investigation into the advantages afforded by light alloys for framing and panelling, whilst in certain instances the possibilities of sheet-steel construction with rolled sections have been fully exploited.
Thus, the whole problem of weight reduction boils down very largely to
chassis design. Deeper sections with lighter-gauge materials are required for frame members, whilst increased use of light alloys should lead to the provision of power-units with a better ratio of weight to output.