Old dog diesel must learn new tricks
Page 51
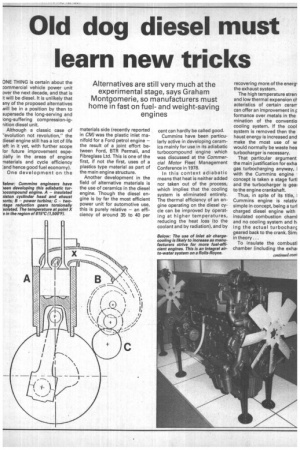
Page 52
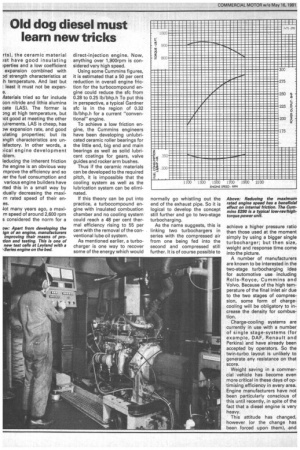
Page 53
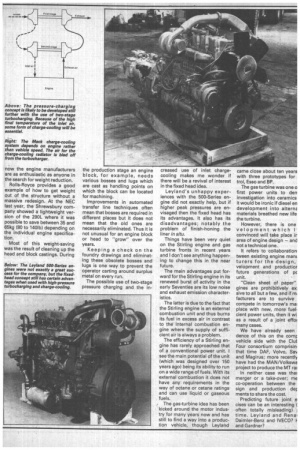
If you've noticed an error in this article please click here to report it so we can fix it.
Alternatives are still very much at the experimental stage, says Graham Montgomerie, so manufacturers must home in fast on fueland weight-saving engines
ONE THING is certain about the commercial vehicle power unit aver the next decade, and that is it will be diesel. It is unlikely that any of the proposed alternatives MU be in a position by then to 3upersede the long-serving and long-suffering compression-ignition diesel unit.
Although a classic case of ''evolution not revolution," the iiesel engine still has a lot of life eft in it yet, with further scope for future improvement espe-jally in the areas of engine -naterials and cycle efficiency :and hence good fuel economy).
One development on the
materials side (recently reported in CM) was the plastic inlet manifold for a Ford petrol engine — the result of a joint effort between Ford, BTR Permali, and Fibreglass Ltd. This is one of the first, if not the first, uses of a plastics type material as part of the main engine structure.
Another development in the field of alternative materials is the use of ceramics in the diesel engine. Though the diesel engine is by far the most efficient power unit for automotive use, this is purely relative — an efficiency of around 35 to 40 per cent can hardly be called good.
Cummins have been particularly active in developing ceramics mainly for use in its adiabatic turbocompound engine which was discussed at the Commercial Motor Fleet Management Conference in 1978.
In this context adiabatic means that heat is neither added nor taken out of the process, which implies that the cooling system is eliminated entirely. The thermal efficiency of an engine operating on the diesel cycle can be improved by operating at higher temperatures, reducing the heat loss (to the coolant and by radiation), and by
recovering more of the energ, the exhaust system.
The high temperature stren and low thermal expansion cb acteristics of certain cerarr can offer an improvement in formance over metals in the mination of the conventio cooling system. If the cool system is removed then the haust energy is increased and make the most use of w would normally be waste hea turbocharger is necessary.
That particular argument the main justification for exha gas turbocharging anyway, I with the Cummins engine concept is taken a stage furtl and the turbocharger is geal to the engine crankshaft.
Thus, in spite of its title, 1 Cummins engine is relativ simple in concept, being a turl charged diesel engine with insulated combustion chaml and no cooling system and h. ing the actual turbocharc geared back to the crank. Simi in theory ...
To insulate the combusti chamber (including the exhal rts), the ceramic material 1st have good insulating )perties and a low coefficient expansion combined with ad strength characteristics at h temperature. And last but : least it must not be expene.
Aaterials tried so far include con nitride and lithia alumina Gate (LAS). The former is ang at high temperature, but lot good at meeting the other luirements. LAS is cheap, has aw expansion rate, and good ulating properties; but its angth characteristics are unisfactory. In other words, a )ical engine development iblem.
teducing the inherent friction he engine is an obvious way mprove the efficiency and so rer the fuel consumption and various engine builders have rted this in a small way by dually decreasing the maxim rated speed of their enes.
lot many years ago, a maxim speed of around 2,600 rpm s considered the norm for a direct-injection engine. Now, anything over 1,900rpm is considered very high speed.
Using some Cummins figures, it is estimated that a 50 per cent reduction in overall engine friction for the turbocompound engine could reduce the sfc from 0.28 to 0.25 lb/bhp.h To put this in perspective, a typical Gardner sfc is in the region of 0.32 lb/bhp.h for a current "conventional" engine.
To achieve a low friction engine, the Cummins engineers have been developing unlubricated ceramic roller bearings for the little end, big end and main bearings as well as solid lubricant coatings for gears, valve guides and rocker arm bushes.
Thus if the ceramic materials can be developed to the required pitch, it is impossible that the cooling system as well as the lubrication system can be eliminated.
If this theory can be put into practice, a turbocompound engine with insulated combustion chamber and no cooling system could reach a 48 per cent thermal efficiency rising to 55 per cent with the removal of the conventional lube oil system.
As mentioned earlier, a turbocharger is one way to recover some of the energy which would normally go whistling out the end of the exhaust pipe. So it is logical to develop the concept still further and go to two-stage turbocharging.
As the name suggests, this is linking two turbochargers in series with the compressed air from one being fed into the second and compressed still further. It is of course possible to achieve a higher pressure ratio than those used at the moment simply by using a bigger single turbocharger; but then size, weight and response time come into the picture.
A number of manufacturers are known to be interested in the two-stage turbocharging idea for automotive use including Rolls-Royce, Cummins and Volvo. Because of the high temperature of the final inlet air due to the two stages of compression, some form of chargecooling will be obligatory to increase the density for combus tion.
Charge-cooling systems are currently in use with a number of single stage-systems (for example, DAF, Renault and Perkins) and have already been accepted by operators. So the twin-turbo layout is unlikely to generate any resistance on that score.
Weight saving in a commer cial vehicle has become even more critical in these days of optimising efficiency in every area. Engine manufacturers have not been particularly conscious of this until recently, in spite of the fact that a diesel engine is very heavy.
This attitude has changed, however (or the change has been forced upon them), and now the engine manufacturers are as enthusiastic as anyone in the search for weight reduction.
Rolls-Royce provides a good example of how to get weight out of the structure without a massive redesign. At the NEC last year, the Shrewsbury company showed a lightweight version of the 290L where it was possible to save between 35 and 65kg (80 to 140Ib) depending on the individual engine specification.
Most of this weight-saving was the result of cleaning up the head and block castings. During the production stage an engine block, for example, needs various bosses and lugs which are cast as handling points on which the block can be located for machining.
Improvements in automated transfer line techniques often mean that bosses are required in different places but it does not mean that the old ones are necessarily eliminated. Thus it is not unusual for an engine block or head to "grow" over the years.
Keeping a check on the foundry drawings and eliminating these obsolete bosses and lugs is one way to prevent the operator carting around surplus metal on every run.
The possible use of two-stage pressure charging and the in
creased use of inlet chargecooling makes me wonder if there will be a revival of interest in the fixed head idea.
Leyland's unhappy experiences with the 500-Series engine did not exactly help, but if higher peak pressures are envisaged then the fixed head has its advantages. It also has its disadvantages; notably the problem of finish-honing the liner in situ.
Things have been very quiet on the Stirling engine and gas turbine fronts in recent years and I don't see anything happening to change this in the near future.
The main advantages put forward for the Stirling engine in its renewed burst of activity in the early Seventies are its low noise and exhaust emission characteristics.
The latter is due to the fact that the Stirling engine is an external combustion unit and thus burns its fuel in excess air in contrast to the internal combustion engine where the supply of sufficient air is always a problem.
The efficiency of a Stirling engine has rarely. approached that of a conventional power unit. I see the main potential of the unit (which was designed over 150 years ago) being its ability to run on a wide range of fuels. With its external combustion it does not have any requirements in the way of octane or cetane ratings and can use liquid or gaseous fuels.
( The gas-turbine idea has been kicked around the motor industry for many years now and has still to find a way into a production vehicle, though Leyland came close about ten years with three prototypes for trol, Esso and BP.
The gas turbine was one o first power units to den investigation into ceramics it would be ironic if diesel en development into alternE materials breathed new life the turbine.
However, there is one velopment which I convinced will take place ir area of engine design — and not a technical one.
It refers to collaboration tween existing engine mank turers for the design, velopment and productior future generations of pc unit.
"Clean sheet of paper" gines are prohibitively ex sive to all but a few, and if rn. facturers are to survive compete in tomorrow's mal place with new, more fuelcient power units, then it wi as a result of a joint effor many cases.
We have already seen dence of this on the comp vehicle side with the Clut Four consortium comprisin, that time DAF, Volvo, Sav and Magirus; more recently have had the MAN/Volkswa project to produce the MT rar
In neither case was ther merger or a take-over; me co-operation between the sign and production der ments to share the cost.
Predicting future joint e cises can be an interesting ( often totally misleading) I time. Leyland and Rena. Daimler-Benz and IVECO? land Gardner?