Value of Flow Production in Axle Construction
Page 41
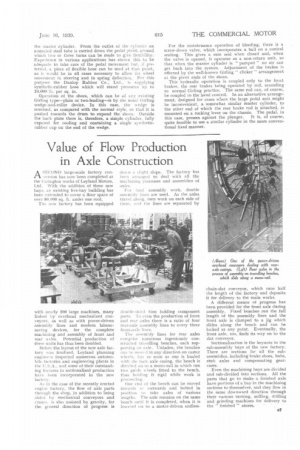
If you've noticed an error in this article please click here to report it so we can fix it.
A SECOND large-scale factory con, version has now been completed at the Farington works of Leyland Motors, Ltd. With the addition of three new bays. an existing five-bay building has been extended to cover a floor space of Oyer 80,000 sq. ft. under one roof.
The new factory has been equipped
with nearly 200 large machines, many linked by overhead mechanized conveyors, as well as with power-driven assemblylines and modern laboursaving devices, for the complete machining and assembly of front and rear axles. Potential production of these units has thus been doubled.
Before the layout of the new axle factory was linalized, Leyland planning engineers inspected numerous automobile factories and engineering plants in the t3_S.A., and some of their outstanding features in sectionalized production have been incorporated in the new factory.
As in the case of the recently erected engile factory, the flow of axle parts through the shop, in addition to being aided by mechanical conveyors and cranes, is also assisted by gravity, for the general direction of progress is 4,10`.1 ii d slight slope. The factory has been arranged to deal with all the machining processes and assemblies of axles.
For final assembly work, double assembly lines are used. As the axles travel along, men work on each side of them, and the lines are separated by d ou bl e • side( i bins holding component parts. To even the production of front and rear axles there is a ratio of four rear-axle assembly lines to every three front-axle lines.
The assembly lines for rear axles comprise numerous ingeniously constructed travelling benches, each supporting an axle. Unladen, the benches can he mov(d in any direction on castor wheels, but so soon as one is loaded with the bare axle casing, the bench is directed on to a mono-rail in which run two guide wheels fitted to the bench, thus holding it rigid while work is proceeding.
One end of the bench can be moved inwards or outwards and bolted in position to take axles of various lengths. The axle remains on the mine bench until it is completed, when it is lowered on to a motor-driven endless
chain-slat conveyor, which runs half the length of the factory and deposits it for delivery to the main works.
A different means of progress has heen provided for the front axle during assembly. Fixed benches run the full length of the assembly lines and the front axle is clamped to a jig which slides along the bench and can he locked at any point. Eventually, the front axle, too, finds its way on to the slat conveyor.
Sectionalization is the keynote in the sub-assembly bays of the new factory. There are sections for all the subassemblies, including brake shoes, hubs, stub axles and compensating gear. cases.
Even the machining bays are divided and sub-divided into sections, All the parts that go to Make a finished axle have portions of a bay in the machining sections to themselves, and they flow in the same downward direction through their various tfirning. milling, drilling and grinding machines for delivery to the " finished " stores. "