Big potential for UK pallet pool
Page 30
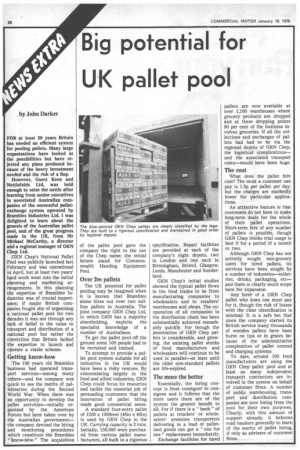
If you've noticed an error in this article please click here to report it so we can fix it.
by John Darker
FOR at least 20 years Britain has needed an efficient system for pooling pallets. Many large organisations have looked at the possibilities but have rejected any plans produced because of the heavy investment needed and the risk of a flop.
However, Guest Keen and Nettlefolds Ltd, was bold enough to seize the nettle after learning from senior executives in associated Australian companies of the successful pallet exchange system operated by Brambles Industries Ltd. I was delighted to learn about the genesis of the Australian pallet pool, and of the great progress made in the UK, from Mr Michael McCarthy, a director and a regional manager of GKN Chep Ltd.
GKN Chep's National Pallet Pool was publicly launched last February and was operational in April, but at least two years' hard work went into the initial planning and marketing arrangements. In this planning the expertise of Brambles Industries was of crucial importance; if major British companies fought shy of organising a national pallet pool for two decades it was not through any lack of belief in the value to transport and distribution of a national pool but rather the conviction that Britain lacked the expertise to launch and operate a viable scheme.
Getting know-how
The 100 years old Brambles business had operated transport services—among many others—and the company was quick to see the merits of palletisation during the Second World War. When there was an opportunity to develop the pallet activities—initially organised by the American Forces but later taken over by • the Australian government— the company devised the hiring and monitoring procedures which constitute the Brambles "know-how." The acquisition of the pallet pool gave the company the right to the use of the Chep name; the initial letters stand for Commonwealth Handing Equipment Pool.
Over 2m pallets
The UK potential for pallet pooling may be imagined when it is known that Brambles alone hires out over two million pallets in Australia, The joint company GKN Chep Ltd, in which GKN has a majority shareholding, exploits the specialist knowledge of a number of Australians.
To get the pallet pool off the ground some 100 people had to be recruited and trained.
To attempt to provide a pallet pool system suitable for all industries in the UK would have been a risky venture. By concentrating largely in the food and allied industries, GKN Chep could focus its resources and tackle the essential job of persuading customers that the innovation of pallet hiring made good commercial sense.
A standard four-entry pallet of 1200 x 1000mm (48in x 40in) is used by GKN Chep in the UK. Carrying capacity is 2 tons. Initially, 150,000 were purchased from various pallet manufacturers, all built to a rigorous specification. Repair facilities are provided at each of the company's eight depots, two in London and one each in Birmingham, Bristol, Glasgow, Leeds, Manchester and Sunderland.
GKN Chep's initial studies showed the typical pallet flows in the food trades to be from manufacturing companies to wholesalers and to retailers' warehouses and shops. The cooperation of all companies in the distribution chain has been substantially achieved remarkably quickly. For though the penetration of GKN Chep pallets is considerable, and growing, the existing pallet stocks of food manufacturers and wholesalers will continue to be used in parallel—at least until the older non-standard pallets are life-expired.
The more the better
Essentially, the hiring concept is from consignor to consignee and it follows that the more users there are of the system the greater benefit to all. For if there is a " bank " of pallets at retailers' or wholesalers' premises transporters delivering in a load of palletised goods can get a "one for one" replacement immediately.
Exchange facilities for hired pallets are now available at over 1,100 warehouses where grocery products are dropped and at these dropping points 90 per cent of the business involves groceries. If all the collections and exchanges of pallets had had to be via the regional depots of GKN Chep, the logistical complications— and the associated transport costs—would have been huge.
The cost
What does the pallet hire cost? The most a customer can pay is 1.5p per pallet per day, but the charges are markedly lower for particular applications.
An attractive feature is that customers do not have to make long-term deals for the whole of their pallet operations. Short-term hire of any number of pallets is possible, though GKN Chep thinks trial usage is best if for a period of a month or two.
Although GKN Chen has not actively sought non-grocery users for hired pallets, its services have been sought by a number of industries—toiletries, drinks, packaging, etc— and there is clearly much scope here for expansion.
Any hirer of a GKN Chep pallet who loses one must pay for it, though the risk of losses with the clear identification is minimal. It is a safe bet that since the company started its British service many thousands of wooden pallets have been burnt on tips or in grates because of the administrative complexities of pallet control and charging systems.
To date, around 100 food manufacturers are using the GKN Chep pallet pool and at least as many independent transport contractors are involved in the system on behalf of customer firms, A number of public warehousing, transport and distribution companies are now hiring from the pool for their own purposes. Clearly, with this amount of support already, it behoves road hauliers generally to learn of the merits of pallet hiring, if only as advisers of customer firms.