DUNLOP TYRES IN THE MAKING.
Page 20
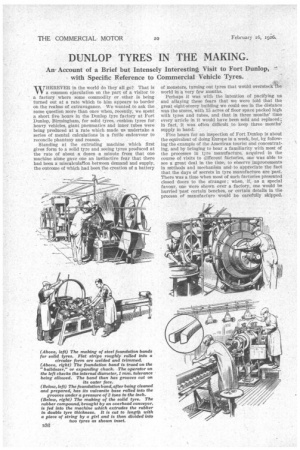
Page 21
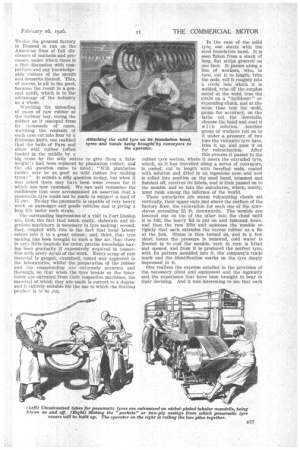
Page 22
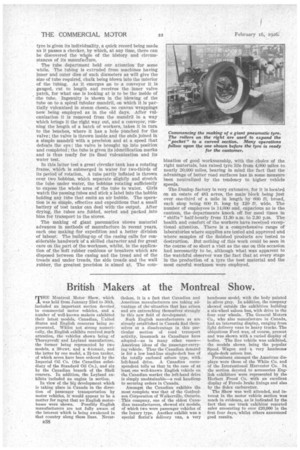
If you've noticed an error in this article please click here to report it so we can fix it.
AnAccount of a Brief but Intensely Interesting Visit to Fort Dunlop, with Specific Reference to Commercial Vehicle Tyres.
WHEREVER in the world do they all go? That is a common ejaculation on the part of a visitor to a factory where some commodity or other is being turned out at a rate which to him appears to border on the realms of extravagance. We wanted to ask the same question more than once when, recently, we spent a short five hours in the Dunlop tyre factory at Fort Dunlop, Birmingham, for solid tyres, cushion tyres for heavy vehicles, giant pneumatics and inner tubes were being produced at a rate which made us undertake a series of mental calculations in a futile endeavour to reconcile phantasy and reason.
Standing at the extruding machine which first gives form to a solid tyre and seeing tyres produced at the rate of about a dozen a minute from that one machine alone gave one an instinctive fear that there had been a miscakulation between demand and supply, the outcome of which had been the creation of a battery of monsters, turning out tyres that would overstock e world in a very few months.
Perhaps it was with the intentiOn of pacifying us and allaying these fears that we were told that the great eight-storey building we could see in the distance was the stores, with 15 acres of floor space packed high with tyres and tubes, and that in three months' time every article in it would have been sold and replaced; in fact, it was often difficult to keep three months' supply in hand.
Five hours for an inspection of Fort Dunlop is about the equivalent of doing Europe in a week, but, by, following the example of the American tourist and concentrating, and by bringing to bear a familiarity with most of the processes in tyre manufacture, acquired in the course of visits to different factories, one was able to see a great deal in the time, to observe improvements in methods and mechanism and to appreciate the fact that the days of secrets in tyre manufacture are past. There was a time when most of such factories presented closed doors to the stranger ; when, if, as a special favour, one were shown over a factory, one would be hurried past certain benches, or certain details in the process of manufacture would be carefully skipped. To-day the greatest factory in Engand is run on the American lines of full disclosure of methods and processes, under which there is a free discussion with competitors and any knowledgeable visitors of the merits and demerits thefeof. This, of course, is all to the good, because the result is a general uplift, which is to the advantage of tile industry as a whole.
Watching the unloading of cases of raw rubber at the railway hay, seeing the rubber as it emerged from its thousands of cases, watching the contents of each case cut into four by a fearsome knife, one realized that the balls of Para and other wild rubber (often loaded in the middle by a big stone by the wily native to give thern a false weight!) had been replaced by plantation rubber, an the old question came to mind "Will plantation rubber ever be as good as wild rubber for making tyres." It sounds a silly question to-day, hut when it • was asked there may have been some reason for it
• which has now vanished. We can well remember the confidence that once accompanied an assertion that a pneumatic .tyre could not be made to support a load of 15 cwt. To-day the pneumatic is capable of very heavy. work on passenger and goods vehicles and is giving a
long life under such strain.
The outstanding impressions of a: visit to Fort Dunlop are, first, the fact that much costly, elaborate and ingenious machinery is necessary in tyre making; second; that, coupled: with this is the fact that -hand labour enters into it to a great extent ; arid, third, that tyre making has been brought to such a fine art that there is very little loophole for error, precise knowledge having been gradually if expensively" acquired in connection with every detail of the.work. Every scrap of -raw material is gauged, examined, tested and approved in the laboratories, whilst the preparation of the rubber and the compounding are extremely accurate and thorough, so that when the tyre treads or the inner tubes are extruded from their respective machines, the material of ,Which they 'are made is correct to a degree and is entirely suitable for-the use to which the finished product is to be knit. In the case of the solid Lyre, one starts with the steel foundation band. It is seen taken from a stack of long, flat strips grooved on one face. It passes along a line of workers, who, in turn, cut it to length, trim the ends, roll it roughly into a circle' into which it is welded, trim off the surplus metal at the weld, true the circle on a "bulldozer" or expanding chuck, and at the awe time test the weld, gauge for accuracy, on the lathe cut the dovetails, cleanse the band and coat it with solution. Another group of workers roll on to it under a pressure of two tons the vulcanite tyre base, trim it up, and pass it on for vulcanization. After this process it passes to the rubber tyre section, where it meets the extruded tyre, which, as it has travelled along a series of conveyors, is cooled, cut to length with bevelled ends, coated with solution and dried in an ingenious oven and now is rolled into position on the steel band, trimmed and finished off, receives its labels, and is then passed on to the moulds and so into the autoclaves, which, surely, must rank among the infernos of the world.•
These autoclaves are steam vulcanizing chests set vertically, their upper ends just above the surface of the factory floor, the excavation for each one of the autoclaves extending 35 ft. downwards. The moulds are lowered one on top of the other into the chest until it is full, the heavy lid is put on and fastened down, and then the ram lifts and squeezes the moulds so tightly that each extrudes the excess rubber as n fin at the join. Steam is then turned on, and in a few short hours the pressure is removed, cold water is flooded in to cool the moulds, each in turn is lifted and opened, and from it is produced the perfect tyre, with its pattern moulded into it, the company' S trade mark and the identification marks on the tyre deeply impressed in it.
One realizes the expense entailed in the provision of the necessary plant and equipment and the ingenuity and the experience that have been brought to bear in their devising. And it was interesting to see that each
tyre is given its individuality, a quick record being made as it passes a checker, by which, at any time, there can be discovered the whole of the history and circumstances of its manufaclure.
The tube department held our attention for some while. The tubing is extruded from machines having inner and outer dies of such diameters as will give the size of tube required, chalk being blown into the interior of the tubing. As it emerges on to a conveyor it is gauged, cut to length and receives the inner valve patch, for what one is looking at is to be the inside of the tube. Ingenuity is -shown in the blowing of the tube on to a spiral tubular mandril, on which it is partially vulcanized in steam chests, no canvas wrappings now being employed as in the old days. After vulcanization it is removed from the mandril in a way which brings it the right way out, and a conveyor, running the length of a batch of workers, takes it in turn to the benches, where it has a hole punched for the valve; the valve is thrown inside and the ends joined in a simple mandril with a precision and at a speed that defeats the eye; the valve is brought up into position and completed ; the tube is given its identification marks and is thus ready for its final vulcanization and its water test.
In this latter test a great circular tank has a rotating frame, which is submerged in water for two-thirds of its period of rotation. A tube partly inflated Is thrown over, two bobbins, which separate slightly and stretch the tube under water, the bobbins rotating sufficiently to expose the whole area of the tube to water. Girls watch the passing tubes and stick a label into the bobbin holding any tube that emits an air bubble. The operation is so simple, effective and expeditious that a small battery of test tanks can deal with the output. After drying, the tubes are folded, sorted and packed into bins for transport to the stores.
The making of giant pneumatics shows material advances in methods of manufacture in recent years, each one making for expedition and a better division of labour. The building-up of the casing calls for considerable handwork of a skilled character and for great care on the part of the workmen, whilst, in the application of the soft rubber cushions or breakers which are disposed between the casing and the tread and of the treads and under treads, the side treads and the wall rubber, the greatest precision is aimed at. The coin bination of good workmanship, with the choice of the right materials, has raised tyre life from 4,000 miles to nearly 20,000 miles, bearing in mind the fact that the advantage of better road surfaces has in some measure been neutralized by the tendency to higher vehicle speeds.
The Dunlop factory is very extensive, for it is located on an estate of 481 acres, the main block being just over one-third of a mile in length by 600 ft. broad, each shop being 600 ft. long by 120 ft. wide. The number of employees is 11,000 and, capacious as is the canteen, the departments knock off, for meal times in " shifts " half-hourly from 11.30 a.m. to 2.30 p.m. The health and comfort of the workers have received exceptional attention. There is a comprehensive range of laboratories where supplies are tested and approved and where samples of the finished products are tested to destruCtion. But nothing of this work could be seen in the course of so short a visit as the one on this occasion had necessarily to be, although what was apparent to the watchful observer was the fact that at every stage in the production of a tyre the best material and the most careful workmen were employed.