New Injection and Compression Testing Equipment
Page 58
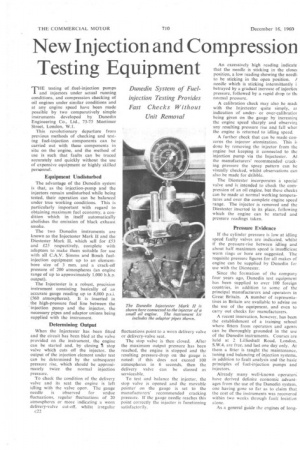
Page 59
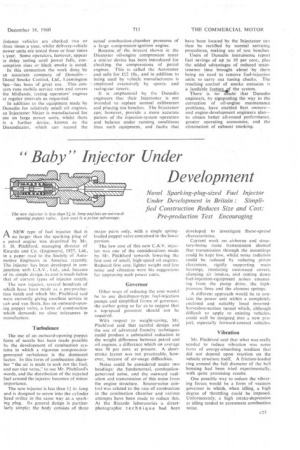
If you've noticed an error in this article please click here to report it so we can fix it.
Dunedin System of Fuelinjection Testing Provides Fast Checks Without Unit Removal
THE testing of fuel-injection pumps and injectors under actual running conditions, and compression checking of oil engines under similar conditions and at any engine speed have been made possible by two comparatively simple instruments developed by Dunedin Engineering Co., Ltd., 73-75 Mortimer Street, London, W.I.
This revolutionary departure from previous methods of checking and testing fuel-injection components can be carried out with these components in situ on the -engine, and the method of use is such that faults can be traced accurately and quickly without the use of expensive equipment or highly skilled personnel.
Equipment Undisturbed
The advantage of the Dunedin system is that, as the injection-pump and the injectors remain undisturbed while being tested, their operation can be balanced under true working conditions. This is particularly important with regard to obtaining maximum fuel economy, a condition which in itself automatically abolishes the emission of black exhaust smoke.
The two Dunedin instruments are known as the Injectester Mark H and the Diestester Mark II, which sell for £53 and £25 respectively, complete with adaptors to make them suitable for use with all C.A.V. Simms and Bosch fuelinjection equipment up to an elementbore size of 3 mm. and a crack-off pressure of 200 atmospheres (an engine range of up to approximately 1,000 b.h.p. output).
The Injectester is a robust, precision instrument consisting basically of an accurate gauge reading up to 8,000 p.s.i. (560 atmospheres). It is inserted in the high-pressure fuel line between the injection pump and the injector, the necessary pipes and adaptor unions being supplied with the instrument.
Determining Output
When the Injectester has been fitted and the circuit has been bled at the valve provided on the instrument, the engine can be started and, by closing "8. stop valve which cuts off the injector, the output of the injection element under test can be determined by the subsequent pressure rise, which should be approximately twice the normal injection pressure.
To check the condition of the delivery valve and its seat the engine is left idling with the valve open. The gauge needle is observed for undue fluctuations, regular fluctuations of 20 atmospheres or more indicating a worn delivery-valve cut-off, whilst irregular c2.2 fluctuations point to a worn delivery valve or delivery-valve seat.
The stop valve is then closed. After the maximum output pressure has been reached, the engine is stopped and the resulting pressure-drop on the gauge is noted: if this does not exceed 100 atmospheres in 6 seconds, then the delivery valve can be classed as serviceable.
To test and balance the injector, the stop valve is opened and the movable pointer on the gauge is set to the manufacturers' recommended cracking pressure. If the gauge needle reaches this point correctly the injector is functioning satisfactorily. An excessively high reading indicate that the needle is sticking in the close( position, a low reading showing the need to be sticking in the open position. needle which is sticking intermittently i betrayed by a gradual increase of injectioi pressure, followed by a rapid drop to thi normal pressure.
A calibration check may also be mad( with the Injectester quite simply, at indication of underor over-ocalibratior being given on the gauge by increasing the engine speed sharply and observing any resulting pressure rise and fall whet the engine is returned to idling speed.
A further check that can be made con. cerns the injector atomization. This i: done by removing the injector from the engine but keeping it connected to the injection pump via the lnjectester. Al the manufacturers' recommended cracking pressure the spray pattern can be visually checked, whilst observations can also be made for dribble. .
The Diestester incorporates a special valve and is intended to check the compression of an oil engine, but these checks can be made at normal working temperatures and over the complete engine speed range. The injector is removed and the Diestester inserted in its place, following which the engine can be started and pressure readings taken.
Pressure Evidence
If the cylinder pressure is low at idling speed faulty valves are indicated, whilst if the pressure-rise between idling and about half maximum speed is insufficient worn rings or bore are suggested. The requisite pressure figures for all makes of engine can be supplied by Dunedin for use with the Diestester.
Since the formation of the company four years ago, Dunedin test equipment has been supplied to over 100 foreign countries, in addition to some of the principal manufacturers and operators in Great Britain. A number of representatives in Britain are available to advise on the use of the equipment, and even to carry out checks for manufacturers.
A recent innovation, however, has been the establishment of a traihing school where fitters from operators and agents can be thoroughly grounded in the use of the Dunedin instruments. Courses are held at 2 Lillieshall Road, London, S.W.4. are free, and last one day only. At them a fitter is taught the maintenance, tuning and balancing of injection systems, in addition to fault analysis and the basic principles of fuel-injection pumps and injectors.
Already many well-known operators have derived definite economic advantages from the use of the Dunedin system. one having gone so far as to claim that the cost of the instruments was recovered within two weeks through fault location alone.
As a general guide the engines of long
distance vehicles are checked two or• hree times a•year, whilst delivery-vehicle power units are tested three or four times year. Some operators, however, appear lo delay testing until power falls, conwmption rises OT black smoke is noted. Tn this connection the work done by in associate company of Dunedin— Diesel .Smoke Control, Ltd., Leamington Spa—has been of great use. This concern runs mobile service vans and covers the Midlands, testing operators' engines at regular intervals as requested.
In addition to the equipment made by Dunedin for relatively small oil engines, an Injectester Major is manufactured for use on large power units, whilst there is a further device, known as the Diesindicator, which can record the actual combustion-chamber pressures of a large compression-ignition engine.
Because _.of the interest, showri in the Diestester Oil.engine compression tester a similar device has been introduced for checking the compressions of :petrol engines. This is called the Autotester and sells for £12 10s., and in addition to being used by vehicle manufacturers is employed extensively by sportsand racing-car tuners.
It is emphasized by the Dunedin engineers that their Injectester is not intendd to replace normal calibration and phasing test benches. The Injectester can however, provide a more accurate picture of the injection-system operation and balance under running conditions than such equipment, and faults that have been located by the Injectester can then be rectified by normal servicing procedures, Making use of test benches.
Users of Dunedin instruments report fuel savings of up to 10 per cent., plus the added advantages of reduced maintenance time brought about by there being no need to remove fuel-injection units to carry out tuning checks. The resulting control of smoke emission is a laudable featuf the system. There is no Mubt that Dunedin engineefs, by signposting the way to the correction of oil-engine maintenance problems, have enabled fleet owners— and engine-development engineers also— to obtain better all-round perforniance, greater operating economies, and the elimination of exhaust smoking.