THE DIRECT APPROACH
Page 31
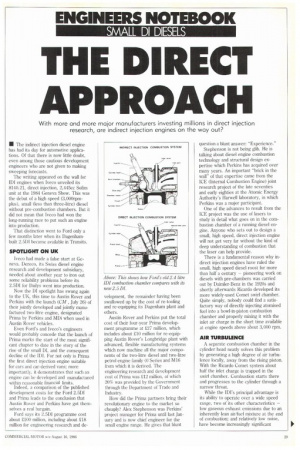
Page 32
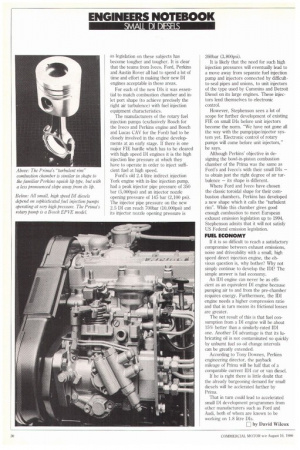
If you've noticed an error in this article please click here to report it so we can fix it.
With more and more major manufacturers investing millions in direct injection research, are indirect injection engines on the way out?
• The indirect injection diesel engine has had its day for automotive applications. Of that there is now little doubt, even among those cautious development engineers who are not given to making sweeping forecasts.
The writing appeared on the wall for ID1 engines when Iveco unveiled its 8140.21, direct injection, 2,445cc Sofim unit at the 1984 Geneva Show. This was the debut of a high speed (3,000rprnplus), small (less than three-litre) diesel without pre-combustion chambers. But it did not mean that Iveco had won the long-running race to put such an engine into production.
That distinction went to Ford only a few months later when its Dagenhambuilt 2.51)1 became available in Transits.
SPOTLIGHT ON UK Iveco had made a false start at Geneva. Dereco, its Swiss diesel engine research and development subsidiary, needed about another year to iron out some reliability problems before its 2. 5D1 for Dailys went into production.
Now the DI spotlight has swung again to the UK, this time to Austin Rover and Perkins with the launch (CM , July 26) of their jointly developed and jointly manufactured two-litre engine, designated Prima by Perkins and MDi when used in Austin Rover vehicles.
Even Ford's and Iveco's engineers would probably concede that the launch of Prima marks the start of the most significant chapter to date in the story of the rise of the small DI, and the consequent decline of the IN. For not only is Prima the first direct injection engine suitable for cars and car-derived vans; more importantly, it demonstrates that such an engine can be developed and manufactured within reasonable financial limits.
Indeed, a comparison of the published development costs for the Ford 2. 5D1 and Prima leads to the conclusion that Austin Rover and Perkins have got themselves a real bargain.
Ford says its 2.5D1 programme cost about 2100 million, including about 218 million for engineering research and de velopment, the remainder having been swallowed up by the cost of re-tooling and re-equipping its Dagenham plant and others.
Austin Rover and Perkins put the total cost of their four-year Prima development programme at 227 million, which includes about 210 million for re-equipping Austin Rover's Longbridge plant with advanced, flexible manufacturing systems which now machine all the major components of the two-litre diesel and two-litre petrol engine family (0 Series and MI6 from which it is derived. The engineering research and development cost of Prima was 212 million, of which 20% was provided by the Government through the Department of Trade and Industry.
How did the Prima partners bring their revolutionary engine to the market so cheaply? Alex Stephenson was Perkins' project manager for Prima until last January and is now chief engineer for the small engine range. He gives that blunt question a blunt answer: "Experience."
Stephenson is not being glib. He is talking about diesel engine combustion technology and structural design expertise which Perkins has acquired over many years. An important "brick in the wall" of that expertise came from the ICE (Internal Combustion Engine) joint research project of the late seventies and early eighties at the Atomic Energy Authority's Harwell laboratory, in which Perkins was a major participant.
One of the advances to result from the ICE project was the use of lasers to study in detail what goes on in the combustion chamber of a running diesel engine. Anyone who sets out to design a small, high speed, direct injection engine will not get very far without the kind of deep understanding of combustion that the laser can help provide.
There is a fundamental reason why indirect injection engines have ruled the small, high speed diesel roost for more than half a century — pioneering work on diesels with pre-chambers was carried out by Daimler-Benz in the 1920s and shortly afterwards Ricardo developed its more widely-used Cornet swirl chamber. Quite simply, nobody could find a satisfactory way of directly injecting atomised fuel into a howl-in-piston combustion chamber and properly mixing it with the inlet air charge in the short time available at engine speeds above about 3,000 rpm.
AIR TURBULENCE A separate combustion chamber in the cylinder head neatly solves this problem by generating a high degree of air turbulence locally, away from the rising piston. With the Ricardo Comet system about half the inlet charge is trapped in the swirl chamber. Combustion starts there and progresses to the cylinder through a narrow throat.
While the IDI's principal advantage is its ability to operate over a wide speed range, two of its other characteristics — low gaseous exhaust emissions due to an inherently lean air/fuel mixture at the end of combustion; and relatively low noise, have become increasingly significant as legislation on these subjects has become tougher and tougher. It is clear that the teams from Iveco, Ford, Perkins and Austin Rover all had to spend a lot of time and effort in making their new DI engines acceptable in those areas.
For each of the new DIs it was essential to match combustion chamber and inlet port shape (to achieve precisely the right air turbulence) with fuel injection equipment characteristics.
The manufacturers of the rotary fuel injection pumps (exclusively Bosch for the Iveco and Perkins engine and Bosch and Lucas CAV for the Ford) had to be closely involved in the engine developments at an early stage. If there is one major FIE hurdle which has to be cleared with high speed DI engines it is the high injection line pressure at which they have to operate in order to inject sufficient fuel at high speed.
Ford's old 2.4 litre indirect injection York engine with in-line injection pump, had a peak injector pipe pressure of 350 bar (5,000psi) and an injector nozzle opening pressure of 145 bar (2,100 psi). The injector pipe pressure on the new 2.5 DI can reach 700bar (10,000psi) and its injector nozzle opening pressure is 260bar (3,800psi).
It is likely that the need for such high injection pressures will eventually lead to a move away from separate fuel injection pump and injectors connected by difficultto-seal pipes and unions, to unit injectors of the type used by Cummins and Detroit Diesel on its large engines. These injectors lend themselves to electronic control.
However, Stephenson sees a lot of scope for further development of existing FIE on small Dls before unit injectors become the norm. "We have not gone all the way with the pump/pipe/injector system yet. Electronic control of rotary pumps will come before unit injectors," he says.
Although Perkins' objective in designing the bowl-in-piston combustion chamber of the Prima was the same as Ford's and Iveco's with their small Dis — to obtain just the right degree of air turbulence — its shape is different.
Where Ford and Iveco have chosen the classic toroidal shape for their combustion chambers, Perkins has developed a new shape which it calls the "turbulent rim". While this chamber gives good enough combustion to meet European exhaust emission legislation up to 1994, Stephenson admits that it will not satisfy US Federal emission legislation.
FUEL ECONOMY If it is so difficult to reach a satisfactory compromise between exhaust emissions, noise and driveability with a small, high speed direct injection engine, the obvious question is, why bother? Why not simply continue to develop the IDI? The simple answer is fuel economy.
An IDI engine can never be as efficient as an equivalent DI engine because pumping air to and from the pre-chamber requires energy. Furthermore, the IDI engine needs a higher compression ratio and that in turn means its frictional losses are greater.
The net result of this is that fuel consumption from a DI engine will be about 15% better than a similarly-rated IDI one. Another DI advantage is that its lubricating oil is not contaminated so quickly by unburnt fuel so oil change intervals can be greatly extended.
According to Tony Downes, Perkins engineering director, the payback mileage of Prima will be half that of a comparable current IDI car or van diesel.
If he is right there is little doubt that the already burgeoning demand for small diesels will be acclerated further by Prima.
That in turn could lead to accelerated small DI development programmes from other manufacturers such as Ford and Audi, both of whom are known to be working on 1.8 litre DI& by David Wilcox