management
Page 50
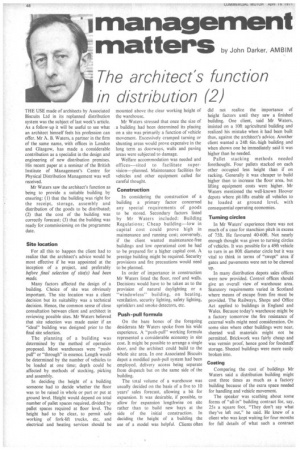
Page 51
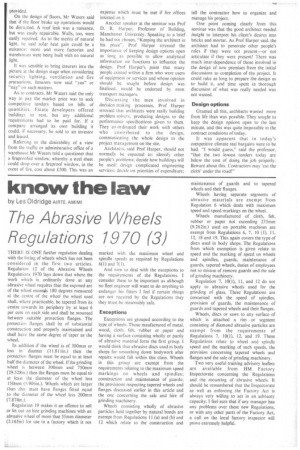
If you've noticed an error in this article please click here to report it so we can fix it.
matters by John Darker AMB1M
The architect's function in distribution (2)
THE USE made of architects by Associated Biscuits Ltd in its replanned distribution system was the subject of last week's article. As a follow-up it will be useful to see what an architect himself feels his profession can offer. Mr A. B. Waters, a partner in the firm of the same name, with offices in London and Glasgow, has made a considerable contribution as a specialist in the design and engineering of new distribution premises. His recent paper at a seminar of the British Institute of Management's Centre for Physical Distribution Management was well received.
Mr Waters saw the architect's function as being to provide a suitable building by ensuring: (1) that the building was right for the receipt, storage, assembly and distribution of the goods to be distributed; (2) that the cost of the building was correctly forecast; (3) that the building was ready for commissioning on the programme date.
Site location For all this to happen the client had to realize that the architect's advice would be most effective if he was appointed at the inception of a project, and preferably before final selection of site(s) had been made.
Many factors affected the design of a building. Choice of site was obviously important. The site location was a client decision but its suitability was a technical decision. Hence, the common sense of close consultation between client and architect in reviewing possible sites. Mr Waters believed that site selection was made easier if an "ideal" building was designed prior to the final site selection.
The planning of a building was determined by the method of operation proposed. Most warehouses were "pushpull" or "through" in essence. Length would be determined by the number of vehicles to be loaded at one time; depth could be affected by methods of stocking, picking and assembly.
In deciding the height of a building someone had to decide whether the floor was to be raised in whole or part or put at ground level. Height would depend on total number of pallet spaces required, divided by pallet spaces required at floor level.. The height had to be clear, to permit safe working of fork-lift trucks, etc, and electrical and heating services should be mounted above the clear working height of the warehouse.
Mr Waters stressed that once the size of a building had been determined its placing on a site was primarily a function of vehicle movement. Excessively cramped turning or shunting areas would prove expensive in the long term as doorways, walls and paving areas were subjected to damage.
Welfare accommodation was needed and offices—sited to facilitate supervision—planned. Maintenance facilities for vehicles and other equipment called for careful thought.
Construction In considering the construction of a building a primary factor concerned any special requirements of goods to be stored. Secondary factors listed by Mr Waters included: Building Regulations; Cheap building—low in capital cost could prove high in maintenance and running cost; conversely, if the client wanted maintenance-free buildings and low operational cost he had to be prepared for a higher capital cost. A prestige building might be required. Security provisions and fire precautions would need to be planned.
In order of importance in construction Mr Waters listed the floor, roof and walls. Decisions would have to be taken as to the provision of natural daylighting or a "windowless" building, on heating, ventilation, security lighting, safety lighting, sprinklers and smoke detectors, etc.
Push-pull formula On the bare bones of the foregoing desiderata Mr Waters spoke from his wide experience. A "push-pull" working formula represented a considerable economy in site cost. It might be possible to arrange a single door, and the architect could build to the whole site area. In one Associated Biscuits depot a modified push-pull system had been employed, delivery access being separate from dispatch but on the same side of the building.
The total volume of a warehouse was usually decided on the basis of a five to 10 years' sales forecast, allowing a bit for expansion. It was desirable, if possible, to allow for expansion lengthwise on site rather than to build new bays at the side of the initial construction. In deciding the height of a building the use of a model was helpful. Clients Often'
did not realize the importance of height factors until they saw a finished building. One client, said Mr Waters, insisted on a 10ft agricultural building and realized his mistake when it had been built thus, against the architect's advice. Another client wanted a 24ft 6in.-high building and when shown one he immediately said it was higher than he needed.
Pallet stacking methods needed forethought. Four pallets stacked on each other occupied less height than if on racking. Generally it was cheaper to build higher than to increase the floor area, but lifting equipment costs were higher. Mr Waters mentioned the well-known Hoover depots where pit-lifts enable all vehicles to be loaded at ground level, with consequential operating economies.
Turning circles In Mr Waters' experience there was not much of a case for stanchion pitch in excess of 75ft. He favoured 40-60ft. Not nearly enough thought was given to turning circles of vehicles. It was possible for a 49ft vehicle to turn in an 80ft diameter circle but it was vital to think in terms of "swept" area if gates and pavements were not to be chewed up.
In many distribution depots sales offices were now provided. Control offices should give an overall view of warehouse area. Statutory requirements varied in Scotland where means of escape from fire must be provided. The Railways, Shops and Office Act applied to buildings in England and Wales. Because today's warehouse might be a factory tomorrow the fire resistance of external walls might need consideration. On some sites where other buildings were near, sheeted wall materials might not be permitted. Brickwork was fairly cheap and was vermin proof, hence good for foodstuff storage. Sheeted buildings were more easily broken into.
Costing Comparing the cost of buildings Mr Waters said a distribution building might cost three times as much as a factory building because of the extra space needed for handling and vehicle movement.
The speaker was scathing about some forms of "all-in" building contract for, say, 25s a square foot. "They don't say what they've left out," he said. He knew of a client who was kept waiting for four months for full details of what such a contract provided.
On the design of floors, Mr Waters said that if the floor broke up operations would be disrupted. A roof leak was a nuisance, but was easily repairable. Walls, too, were easily repaired. As to the merits of natural light, he said solar heat gain could be a nuisance: more and more factories and warehouses were being built with no natural light.
It was sensible to bring insurers into the picture at the design stage when considering security lighting, ventilation and fire precautions. Insurers now said -yea" or "nay" on such matters.
As to contracts, Mr Waters said the only way to pay the market price was to seek competitive tenders based on bills of quantities. Estate developers offered buildings to rent, but any additional requirements had to be paid for. If a company arranged its own building it could, if necessary, be sold to an investor and leased.
Referring to the desirability of a view from the traffic or administrative office of a warehouse Mr Waters told a questioner that a firoproofed window, whereby a steel sheet could drop over a fireproof window, in the event of fire, cost about £300. This was an expense which must be met if fire offices insisted on it.
Another speaker at the seminar was Prof D. R. Harper, Professor of Building, Manchester University. Speaking to a brief he had not chosen, "Keeping the architect in his place", Prof Harper stressed the importance of keeping design options open as long as possible to allow analytical information on functions to influence the design. Prof Harper's point that many people existed within a firm who were users of equipment or services and whose opinion should be sought before design was finalized, would be endorsed by most transport managers.
Discussing the men involved in decision making processes, Prof Harper stressed that architects were really building problem-solvers, producing designs to the performance specifications given to them. They co-ordinated their work with others who contributed to the design, communicating the whole design to the project management on the site.
Architects, said Prof Harper, should not normally be expected to: identify other people's problems; decide how buildings will be used: design complicated engineering services; decide on priorities of expenditure;
tell the contractor, how to organize and manage his project.
One point coming clearly from this seminar was that the good architect needed insight to interpret his client's desires into bricks and mortar. As Prof Harper said, the architect had to penetrate other people's roles if they were not present—or not articulate if they were present! There was much inter-dependence of those involved in the design of new premises from the initial discussions to completion of the project. It could take as long to prepare the design as to build it, and time spent in thorough discussion of what was really needed was not wasted.
Design options Granted all this, architects wanted more from life than was possible. They sought to keep the design options open to the last minute. and this was quite impossible in the contract conditions of today.
It was apparent that in today's competitive climate real bargains were to be had. "I would guess," said the professor, "that the two lowest tenders today are below the cost of doing the job properly. Beware about this. Contractors may 'cut the cloth' under the road!"