A System of Costing.*
Page 22
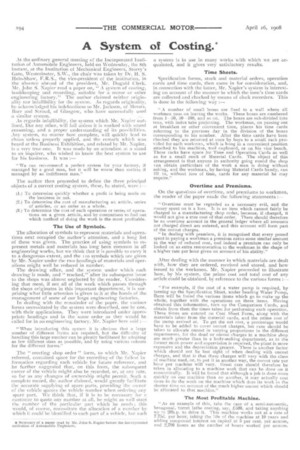
Page 23
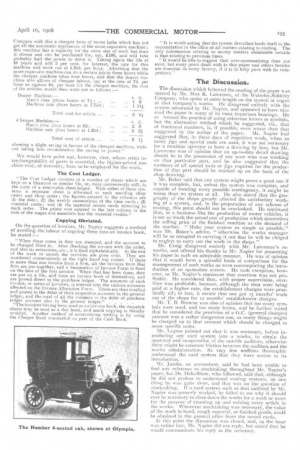
If you've noticed an error in this article please click here to report it so we can fix it.
At the ordinary general meeting of the Incorporated Instillution of Automobile Engineers, held on Wednesday, the 8th instant, at the Institution of Mechanical Engineers, Storey's Gate, Westminster, S.W., the chair was taken by Dr. H. S. Hele-Shaw, F.R.S., the vice-president of the institution, in the absence abroad of the president, Mr. Dugald Clerk. Mr. John S. Napier read a paper on, " A system of costing, -bookkeepingand recording, suitable for a tnotor or other engineering factory." The author claimed neither originality nor infallibility for the system. As regards originality, he acknowledged his indebtedness to Mr. Jackson, of Messrs. Barr and Stroud, of Glasgow, who have successfully used a similar system.
As regards infallibility, the system which Mr. Napier outlined, like any other, will fail unless it is worked with sound reasoning, and a proper understanding of its possibilities. Any system, no matter how complete, will quickly lend to chaos unless properly applied, and the remark which was beard at the Business Exhibition, and related by Mr. Napier, is a very true one. It was made by an attendant at a stand to an inquirer, who wished to know the best system to use for his business. It was :—
" We can recommend a perfect system for your factory, if managed by a good man, but it will be worse than useless if managed by an indifferent man."
The author then proceeded to define the three principal objects of a correct costing system, these, he stated, were (1.) To determine quickly whether a profit is being made on the business or not.
(2.) To determine the cost of manufacturing an article, series of articles, or an order as a whole.
..(3.) To determine the cost of each operation or series of operations on a given article, and by comparison to find out which method of doing the work is the most profitable.
The Use of Symbols.
The allocation of symbols to represent materials and operations next occupied the author's attention, and a long list of these was given. The practice of using symbols to represent metals and materials has long been common in all engineering works, hut we think that it is possible to carry it to a dangerous extent, and the iso symbols which are given by Mr. Napier under the two headings of materials and operations might well be reduced in number.
The drawing office, and the system under which each drawing is made, and " tracked," after its subsequent issue to the shops was almost neglected by the reader. Considering that most, if not all of the work which passes through the shops originates in this important department, it is surprising what little attention is given to it at the hands of the management of some of our large engineering factories.
In dealing with the remainder of the paper, the various forms necessitated by the system were described, one by one, with their applications. They were introduced under appropriate headings and in the same order as they would be called for in an engineering factory. Mr. Napier here said :—
"When introducing this system it is obvious that a large number of different forms are required, but the difficulty of handling this large number can be greatly facilitated by adopting as few different sizes as possible, and by using various colours for the different forms."
The " erecting shop order " form, to which Air. Napier referred, contained space for the recording of the fullest information regarding each vehicle for future reference, and he further suggested that, on this form, the subsequent career of the vehicle might also he recorded, or, at any rate, so far as any changes of ownership might permit. Such a complete record, the author claimed, would greatly facilitate the accurate supplying of spare parts, providingthe owner of the vehicle quotes the vehicle number when ordering any
spare part. We think that, if it is to he n v 'ecessarfor customer to quote any number at all, he might as well state the number of the particular part which he needs ; this would, of course, necessitate the allocation of a number by which it could be identified to each part of a vehicle, hut such a system is in use in many works with which we are acquainted, and it gives very satisfactory results.
Time Sheets.
Specification forms, stock and material orders, operation cards and time cards, then came in for consideration, and, in connection with the latter, Mr. Ni-pier's system is interesting on account of the manner in which the men's time cards are collected and checked by means of clock recorders. This is done in the following way :—
" A number of small boxes are fixed to a wall where all workmen pass on leaving the works. These boxes are numbered from 1-50, 50-100, and so on. The boxes are sub-divided into tens, with index tabs projecting. The workman, on passing out at breakfast or other convenient time, places his time cards referring to the previous day in the division of the boxes corresponding to his number. After the time cards have been checked they are returned at once by boys to a small rack provided for each workman, which is hung in a convenient position attached to his machine, tool cupboard, or on his vice bench. These racks have space for Time and Operation Cards as well as for a small stock of Material Cards. The object of this arrangement is that anyone in authority going round the shop can obtain particulars of the work a man is doing without asking, and the workman, by having Material Cards handy, can fill in, without loss of time, cards for any material he may require.'i
Overtime and Premiums.
On the questions of overtime, and premiums to workmen, the reader of the paper made the following statements Overtime musthe regarded as a necessary evil, and the money spent on it a loss. It is an item which cannot fairly be charged to a manufacturing shop order, because, if charged, it would not give a true cost of that order. There should therefore be an overtime account in the general ledger where all amounts not charged direct are entered, and this account will form part of the oncost charges.
"In dealing with premium, it is recognised that every pound spent in paying a workman a premium earns some similar amount in the way of reduced cost, and indeed a premium can only be looked on as extra remuneration to the workman in the shape of a higher rate per hour given on account of his ability."
After dealing with the manner in which materials are dealt with, how they are ordered, received and stored, and how issued to the workmen, Mr. Na. pier proceeded to illustrate how, by his system, the prime cost and total cost of any article could be obtained, by reference to the various forms :— "For example, if the cost of a water pump is required, by turning up the Specification Sheet, under heading Water Pump, There will be found the various items which go to make up the whole, together with the operations on these items. Having obtained this information, turn up the Comparison Cards, and obtain from them the times taken for performing each operation. These times are entered on Cost Sheet Form, along with the materials taken from the material cards, and the prime cost of the pump arrived at. To get the net cost, a percentage would have to be added to cover oncost charges, but care should be taken to allocate oncost in varying proportions in the different departments, for the dead or oncost charges in a machine shop are much greater than in a body-making department, as in the former more power and supervision is requited, the plant is more expensive and the depreciation greater. There is another factor which should not he lost sight of when dealing with oncost charges, and that is that these charges will vary with the class of machine used, or, in put it in another way, the oncost rate per hour per machine will vary. Great care should therefore be taken in allocating to a machine work that can be clone on it economically. It will be found that although a job is done more quickly on one machine than on another, it may actually cost snore to do the work on the machine which does its work in the shorter time on account of the much higher oncost which should be allocated to that machine."
The Most Profitable Machine.
"As an example of this, take the case of a semi-automatic, hexagonal, turret lathe costing, say, £530, and taking anything up to 20h.p. to drive it. This machine works out at a rate of 7.75d. per hour, taking the life of the machine at 10 years and adding compound interest on capital at 5 per cent, per annum, and 2,700 hours as the number of hours worked per annum.
Compare with this a cheaper form of turret lathe which has not got all the automatic appliances of the more expensive machine ; this machine has a capacity for the same size of work but does it slower and can be purchased for, say, £100, and will take probably half the power to drive it. Taking again the life at 10 years and add 5 per cent, for interest, the rate for this machine will work out at 1.33d. per hour. Admitting that the more expensive machine can do a certain job in three hours while the cheaper machine takes four hours, and that the dearer machine also allows of cheaper labour, say at the rate of 7d. per hour as against 8d. per hour for the cheaper machine, the cost of the articles would then work out as follows :— showing a slight saving in favour of the cheaper machine, without taking into consideration the saving in power."
We would here point out, however, that, wherc strict interchangeability of parts is essential, the higher-priced machine may, of necessity, have to be employed for the work.
The Cost Ledger.
" The Cost Ledger consists of a number of sheets which are kept on a Shannon or similar file, or, more conveniently still, in The form of a removable sheet ledger. With either of these systems a separate sheet is allocated to each standing shop order and shop order ; the figures. entered in the columns are (1) the date ; (2) the weekly summations of the time cards ; (31 material cards ; and (4) the material return cards referring to each order. The prime cost entered in the last column is the sum of the wages and materials less the material credits."
Copying Obviated.
On the question of invoices, Mr. Napier suggests a method of avoiding the labour of copying these into an invoice book, he stated :—
" When these come in they are stamped, and the account to be charged filled in. After checking the invoice with the order, and also its extensions, etc., it is filed alphabetically. At the end of the week or month the invoices are gone over. They are numbered consecutively at the right hand top corner. If there is more than one invoice front a firm, all the invoices from that firm are put together, and a Summation of Invoice Form is fixed on the face of the first invoice. When that has been done, they are put on a file, and form an invoice book of themselves, and are posted direct to the purchase ledger. The amounts of each invoice, or series of invoices, is entered into the various accounts affected on the Invoice Allocation Form. These are then totalled and posted to the debit of their respective accounts in the general ledger, and the total of all the columns to the debit of purchase ledger account also in the general ledger." . . . . .
"The invoices having been used as an invoice book, the despatch sheets may be used as a day book, and much copying is thereby avoided. Another method of economising writing is by using the Cheque Book counterfoil as part of the Cash Book.
"It is worth noting that the system described lends itself to the concentration in the office of all matters relating to costing. The only information relating to money matters obtainable outside is that relating to premium times. "It would be idle to suggest that over-systematising does not exist, but every point dealt with in this paper and others besides are essential in every factory, if it is to keep pace with 45 cern:. petitors."
The Discussion: The discussion which followed the reading of the paper was opened by Mr. Max R. Lawrence, of the Wolselev-Siddeley Company, who spoke at some length on the system in vogue at that company's works. He disagreed entirely with the system advocated by Mr. Napier, and appeared to have misread the paper in many of its most important bearings. He cc lernned the practice of using reference letters or symbols, but the alternative method which he suggested, viz., that of fractional numbers, is, if possible, even worse than that
suggested by the author of the paper. Mr. Napier had suggested that, in these days of repetition work, when so many jigs and special tools are used, it was not necessary for a machine operator to have a drawing by him, but Mr. Lawrence was of opinion that an up-to-date detail drawing should he in the possession of any man who was working on that particular part, and he also suggested that the numbers of all special tools or jigs required for the production of that part should be marked up on the back of the shop drawing.
Mr. Baker said that any system might prove a good one if it was complete, but, unless the system was complete, and capable of meeting every possible contingency, it might be worse than no system at all. He also stated that the geography of the shops greatly affected the satisfactory working of a system, and, in the preparation of any scheme of costing, this point should not be overlooked. He continued that, in a business like the production of motor vehicles, it is not so much the actual cost of production which determines the selling price of the finished machine as the demand of the market. " Make your system as simple as possible," was Mr. Baker's advice, " otherwise the works manager will be so occupied in carrying it out that he will be (bilged to neglect to carry out the work in the shops." Mr. Craig disagreed entirely with Mr. Lawrence's remarks, and offered his thanks to Mr. Napier for presenting his paper in such an admirable manner. He was of opinion that it would form a splendid basis of comparison for the management of such works as were contemplating the introduction of an up-to-date system. He took exception, however, to Mr. Napier's statement that overtime was not profitable. He considered that, with proper supervision, overtime was profitable, because, although the men were being paid at a higher rate, the establishment Charges were practically nil; in fact, it meant that one got 15 months' work out of the shops for 12 months' establishment charges.
Mr. T. B. Browne was also of opinion that too many symbols were used, and too many forms, and he further stated that he considered the provision of a G.C. (general charges) account was a rather dangerous one, as many things might be charged up to that account which should be charged to some specific order.
Mr. Legros pointed out that it was necessary, before introducing any card system into a works, to obtain the approval and co-operation of the outside auditors, otherwise there might be constant friction between the auditors and the works administration. So very few auditors thoroughly understood the card system that they were averse to its introduction.
Mr. Jacobs, an accountant, said he had been unable to find ant' reference to stocktaking throughout Mr. Napier's paper, but Dr. Hele-Shaw, who followed, said that, although he did not profess to understand costing systems, on one thing he was quite clear, and that was on the question of stocktaking_ If a card system such as that outlined by Mr. Napier was properly worked, he failed to see why it should ever be necessary to close down the works for a week or more for the purpose of counting up and valuing every article in the works. Whenever stocktaking was necessary, the value of the stock in hand, rough material, or finished goods, could be obtained in the general office from the record cards.
At this point the discussion was closed, and, as the hour was rather late, Mr. Napier did not reply, but stated that he would communicate his reply to the secretary.