UNIROYAL EUROPE
Page 28
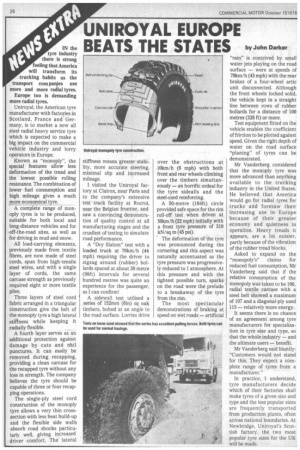
If you've noticed an error in this article please click here to report it so we can fix it.
BEATS THE STATES by John Darker IN the tyre industry there is strong feeling that America will transform its trucking habits as the transport corn pansies use more and more radial tyres.
Europe too is demanding more radial tyres.
Uniroyal, the American tyre manufacturer with factories in Scotland, France and Germany, is to market a new all steel radial heavy service tyre which is expected to make a big impact on the commercial vehicle industry and lorry operators in Europe.
Known as "monoply", the special features allow less deformation of the tread and the lowest possible rolling resistance. The combination of lower fuel consumption and high mileage gives a much more economical tyre.
A complete range of monoply tyres is to be produced, suitable for both local and long-distance vehicles and for off-the-road sites, as well as for driving in mud and snow.
All load-carrying elements, previously made from textile fibres, are now made of steel cords, spun from high-tensile steel wires, and with a single layer of cords, the same carcase strength as previously required eight or more textile plies.
Three layers of steel cord fabric arranged in a triangular construction give the belt of the monoply tyre a high lateral stiffness while keeping it radially flexible. .
A fourth layer serves as an additional protection against damage by cuts and WI punctures. It can easily be removed during recapping, providing a clean carcase for the recapped tyre without any loss in strength. The company believes the tyre should be capable of three or four recapping operations.
The single-ply steel cord construction of the monoply tyre allows a very thin crosssection with less heat build-up and the flexible side walls absorb road shocks particularly well, giving increased driver comfort. The lateral stiffness means greater stability, more accurate steering, minimal slip and increased mileage.
I visited the Uniroyal factory at Clairox, near Paris and to the company's extensive test track facility at Rocroi, near the Belgian frontier, and saw a convincing demonstration of quality control at all manufacturing stages and the cruellest of testing to simulate road performance.
A "Dry Slalom" test with a loaded truck at 70km /h (44 mph) requiring the driver to zigzag around (rubber) bollards spaced at about 30 metre (98ft) intervals for several hundred metres was quite an experience for the passenger, as I can confirm!
A sidewall test utilised a series of 152mm (Gin) sq oak timbers, bolted at an angle to the road surface. Lorries drive over the obstructions at 10km/h (6 mph) with both front and rear wheels climbing over the timbers simultaneously — an horrific ordeal for the tyre sidealls and the steel-cord reinforcing.
A 50-metre (164ft) circle provided safe space for the rim roll-off test when driven at 50km/h (22 mph) initially with a front tyre pressure of 310 kN/sq m (45 psi). • The deformation of the tyre was pronounced during the cornering and this aspect was naturally accentuated as the tyre pressure was progressively reduced to 1 atmosphere. At this pressure and with the tightest possible turn, sparks on the road were the prelude to a breakaway of the tyre from the rim.
The most spectacular demonstrations of braking at speed on wet roads — artificial "rain" is contrived by small water jets playing on the road surface — were at speeds of 70km/h (43 mph) with the rear brakes of a four-wheel artic unit disconnected. Although the front wheels locked solid, the vehicle kept in a straight line between rows of rubber bollards for a distance of 100 metres (328 ft) or more.
Test equipment fitted on the vehicle enables the coefficient of friction to be plotted against speed. Given the right depth of water on the road surface "planing" of tyres can be demonstrated.
Mr Vanderberg considered that the monoply tyre was more advanced than anything available to the trucking industry in the United States. He believed that America would go for radial tyres for trucks and foresaw their increasing use in Europe because of their greater economy and quietness in operation. Heavy treads it appears, are a lot noisier, partly because of the vibration of the rubber tread blocks.
Asked to expand on the "monopoly's" claims for reduced fuel consumption, Mr Vanderberg said that if the relative consumption of the monopoly was taken to be 100, radial textile carcase with a steel belt showed a maximum of 107 and a diagonal-ply used 115 — relatively more energy.
It seems there is no chance of an agreement among tyre manufacturers for specialisation in tyre size and type, so that the whole industry — and the ultimate users — benefit.
Mr Vanderberg said bluntly: "Customers would not stand for this. They expect a complete range of tyres from a manufacturer."
In practice, I understand, tyre manufacturers decide which of their factories shall make tyres of a given size and type and the less popular sizes are frequently transported from production plants, often across national boundaries. At Newbridge. Uniroyal's Scottish factory, the two most popular tyre sizes for the UK will be made.