Future pointers to tipping gear design
Page 24
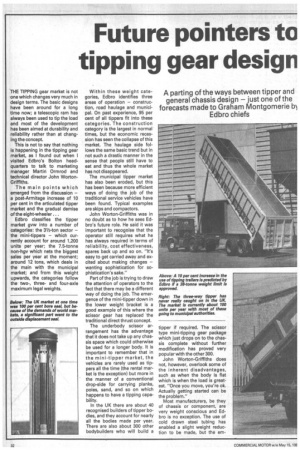
Page 25
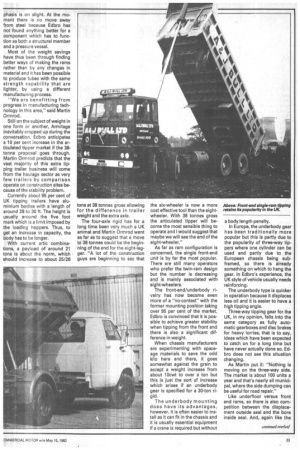
If you've noticed an error in this article please click here to report it so we can fix it.
THE TIPPING gear market is not one which changes very much in design terms. The basic designs have been around for a long time now; a telescopic ram has always been used to tip the load and most of the development has been aimed at durability and reliability rather than at changing the concept.
This is not to say that nothing is happening in the tipping gear market, as I found out when I visited Edbro's Bolton headquarters to talk to marketing manager Martin Ormrod and technical director John WortonGriffiths.
The main points which emerged from the discussion — a post-Armitage increase of 10 per cent in the articulated tipper market and the gradual demise of the eight-wheeler Edbro classifies the tipper market gvw into a number of categories: the 31/2-ton sector — the mini-tippers — which currently account for around 1,200 units per year; the 7.5-tonne non-hgv which nets the biggest sales per year at the moment; around 12 tons, which deals in the main with the municipal market; and from this weight upwards, the categories follow the two-, threeand four-axle maximum legal weights. Within these weight categories, Edbro identifies three areas of operation — construction, road haulage and municipal. On past experience, 95 per cent of all tippers fit into these categories. The construction category is the largest in normal times, but the economic recession has seen the collapse of this market. The haulage side follows the same basic trend but in • not such a drastic manner in the sense that people still have to eat and thus the whole market has not disappeared.
The municipal tipper market has also been eroded, but this has been because more efficient ways of doing the job of the traditional service vehicles have been found. Typical examples are skips and compactors.
John Worton-Griffiths was in no doubt as to how he sees Edbro's future role. He said it was important to recognise that the operator still requires what he has always required in terms of reliability, cost effectiveness, spares back up and so on. "It's easy to get carried away and excited about making changes — wanting sophistication for sophistication's sake," Part of the job is trying to draw the attention of operators to the fact that there may be a different way of doing the job. The emergence of the mini-tipper down in the lower weight bracket is a good example of this where the scissor gear has replaced the traditional direct thrust concept.
The underbody scissor arrangement has the advantage that it does not take up any chassis space which could otherwise be used for a longer body. it is important to remember that in the mini-tipper market, the vehicles are rarely used as tippers all the time (the rental market is the exception) but more in the manner of a conventional drop-side for carrying planks, poles, sand, and so on which happens to have a tipping capability.
In the UK there are about 40 recognised builders of tipper bodies, and they account for nearly all the bodies made per year. There are also about 300 other bodybuilders who will build a tipper if required. The scissor type mini-tipping gear package which just drops on to the chassis complete without further modification has proved very popular with the other 300.
John Worton-Griffiths does not, however, overlook some of the inherent disadvantages, such as when the body is flat which is when the load is greatest. "Once you move, you're ok. Actually getting started can be the problem."
Most manufacturers, be they of chassis or component, are very weight conscious and Edbro is no exception. The use of cold drawn steel tubing has enabled a slight weight reduction to be made, but the em phasis is on slight. At the moment there is no move away from steel because Edbro has not found anything better for a component which has to function as both a structural member and a pressure vessel.
Most of the weight savings have thus been through finding better ways of making the rams rather than by any changes in material and it has been possible to produce tubes with the same strength capability that are lighter, by using a different manufacturing process.
"We are benefitting from progress in manufacturing technology in this area," said Martin Ormrod.
Still on the subject of weight in one form or another, Armitage inevitably cropped up during the conversation. Edbro anticipates a 10 per cent increase in the articulated tipper market if the 38tonne proposal goes through. Martin Ormrod predicts that the vast majority of this extra tipping trailer business will come from the haulage sector as very few trailers by comparison operate on construction sites because of the stability problem.
Currently about 95 per cent of UK tipping trailers have aluminium bodies with a length of around 28 to 30 ft. The height is usually around the five foot mark which is a limit imposed by the loading hoppers. Thus, to get an increase in capacity, the body has to be longer.
With current artic combinations, a payload of around 21 tons is about the norm, which should increase to about 25/26 tons at 38 tonnes gross allowing for the difference in trailer weight and the extra axle.
The four-axle rigid has for a long time been very much a UK animal and Martin Ormrod went as far as to suggest that a move tO 38 tonnes could be the beginning of the end for the eight-legger. "A lot of the construction guys are beginning to say that the six-wheeler is now a more cost effective tool than the eightwheeler. With 38 tonnes gross the articulated tipper will become the most sensible thing to operate and I would suggest that maybe we will see the end of the eight-wheeler."
As far as ram configuration is concerned, the single front-end unit is by far the most popular. There are still many operators who prefer the twin-ram design but the number is decreasing and is mainly associated with eight-wheelers.
The front-end/underbody rivalry has now become even more of a "no-contest" with the former mounting position taking over 95 per cent of the market. Edbro is convinced that it is possible to achieve greater stability when tipping from the front and there is also a significant difference in weight.
When chassis manufacturers are experimenting with spaceage materials to save the odd kilo here and there, it goes somewhat against the grain to accept a weight increase from about 10cwt to over a ton but this is just the sort of increase which arises if an underbody gear is specified for a 30-ton rigid.
The underbody mounting does have its advantages, however. It is often easier to install as it can fit in the chassis and it is usually essential equipment if a crane is required but without a body length penalty.
In Europe, the underbody gear has been traditionally more popular but this is partly due to the popularity of three-way tippers where one cylinder can be used and partly due to the European chassis being subframed, so there is already something on which to hang the gear. In Edbro's experience, the UK style of vehicle usually needs reinforcing.
The underbody type is quicker in operation because it displaces less oil and it is easier to have a high tipping angle.
Three-way tipping gear for the UK, in my opinion, falls into the same category as fully automatic gearboxes and disc brakes for heavy lorries, that is to say, ideas which have been expected to catch on for a long time but have never actually done so. Edbro does not see this situation changing.
As Martin put it: "Nothing is moving on the three-way side. The market is about 100 units a year and that's nearly all municipal, where the side dumping can be useful for road repair."
Like underfloor versus front end rams, so there is also competition between the displacement outside seal and the bore inside seal. And, again like the