New Design for injector Nozzles
Page 60
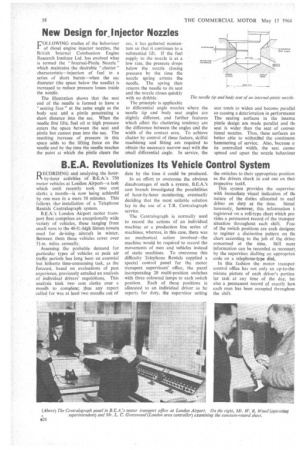
If you've noticed an error in this article please click here to report it so we can fix it.
L'OLLOWING studies of the behaviour 1 of diesel engine injector nozzles, the British Internal Combustion Engine Research Institute Ltd. has evolved what is termed the " Internal-Pintle Nozzle" which maintains the desirable " chatter " characteristic—injection of fuel in a series of short bursts—when the sac diameter (the space below the needle) is increased to reduce pressure losses inside the nozzle.
The illustration shows that the seat end of the needle is formed to have a " seating face" at the same angle as the body seat arid a pintle penetrating a short distance into the sac. When the needle first lifts, fuel oil at high pressure enters the space between the seat and pintle but cannot pass into the sac. The resulting increase of pressure in this space adds to the lifting force on the needle and by the time the needle reaches the point at which the pintle clears the sac, it has gathered momentum so that it continues to a substantial lift. If the fuel supply to the nozzle is at a low rate, the pressure drops below the nozzle closing pressure by the time the nozzle spring arrests the needle. The spring then returns the needle to its seat and the nozzle closes quickly with no dribble.
The principle is applicable to differential angle nozzles where the needle tip and body seat angles are slightly different, and further features which affect the chattering tendency are the difference between the angles and the width of the contact area. To achieve chatter by control of these factors, skilful machining and fitting are required to obtain the necessary narrow seat with the small differential angle. In service, the seat tends to widen and become parallel so causing a deterioration in performance The seating surfaces in the interna *die design are made parallel and till seat is wider than the seat of conven tional nozzles. Thus, these surfaces an better able to withstlad the continumi hammering of service. Also, because o its controlled width, the seat canno spread and upset the nozzle behaviour