road and workshop
Page 92
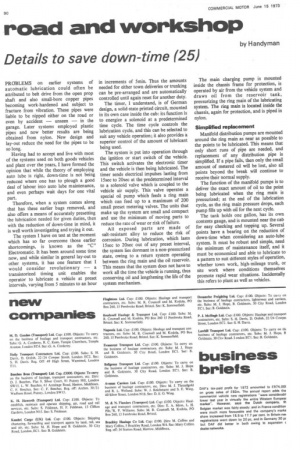
If you've noticed an error in this article please click here to report it so we can fix it.
Details to save down-time (25)
by Handyman PROBLEMS on earlier systems of automatic lubrication could often be attributed to belt drive from the open prop shaft and also small-bore copper pipes becoming work-hardened and subject to fracture from vibration. These pipes were liable to be nipped either on the road or even by accident — unseen — in the garage. Later systems employed plastic pipes and now better results are being obtained from nylon. New design and lay-out reduce the need for the pipes to be so long.
Having had to accept and live with most of the systems used on both goods vehicles and plant over the years, I have formed the opinion that while the theory of employing auto lube is right, down-time is not being reduced where one has to plough a good deal of labour into auto lube maintenance, and even perhaps wait days for one vital part.
Therefore, when a system comes along that has these earlier bugs removed, and also offers a means of accurately presetting the lubrication needed for given duties, then with the reduction of down-time in mind, it is well worth investigating and trying it out.
The system I have on test at the moment which has so far overcome those earlier shortcomings, is known as the "C" Electromatic. It has been around some time now, and while similar in general lay-out to other systems, it has one feature that I would consider revolutionary -a transistorized timing unit enables the operator to lubricate a vehicle at preset intervals, varying from 5 minutes to an hour in increments of 5min. Thus the amounts needed for either town deliveries or trunking can be pre-arranged and are automatically controlled until again reset for another duty.
The tinier, I understand, is of German design, a solid-state printed circuit, mounted in its own case inside the cab: its function is to energize a solenoid at a predetermined time cycle. The time cycle controls the lubrication cycle, and this can be selected to suit any vehicle operation; it also provides a superior control of the amount of lubricant being used.
The system is put into operation through the ignition or start switch of the vehicle. This switch activates the electronic timer and the vehicle is then being lubricated. The timer sends electrical impulses lasting from 15sec to 20sec at the predetermined interval to a solenoid valve which is coupled to the vehicle air supply. This valve operates a special oil pump which feeds a ring main which can feed up to a maximum of 200 small preset metering valves. The units that make up the system are small and compact and use the minimum of moving parts to reduce the rate of wear or risk of failure.
All exposed parts are made of salt-resistant alloy to reduce the risk of corrosion. During lubrication, which lasts 15sec to 20sec out of any preset interval, the system lies dormant in a non-pressurized state, owing to a return system operating between the ring main and the oil reservoir. This means that the system does not have to work all the time the vehicle is running, thus conserving oil and lengthening the life of the system mechanism.
The main charging pump is mounted inside the chassis frame for protection, is operated by air from the vehicle system and draws oil from the reservoir tank, pressurizing the ring main of the lubricating system. The ring main is located inside the chassis, again for protection, and is piped in nylon.
Simplified replacement Manifold distribution pumps are mounted around the ring main as near as possible to the points to be lubricated. This means that only short runs of pipe are needed, and replacement of any distribution pipe is simplified. If a pipe fails, then only the small amount of metered oil will be lost, also all points beyond the break will continue to receive their normal supply.
The function of the manifold pumps is to deliver the exact amount of oil to the point being lubricated when the ring main is pressurized; at the end of the lubrication cycle, as the ring main pressure drops, each pump fills up with oil for the next cycle.
The tank holds one gallon, has its own contents gauge, and is mounted near the cab for easy checking and topping up. Several points have a bearing on the reduction of down-time when considering an auto-lube system. It must be robust and simple, need the minimum of maintenance itself, and it must be economical and able to lubricate to a pattern to suit different styles of operation, whether town work, high-mileage trunk, or site work where conditions themselves promote rapid wear situations. Incidentally this refers to plant as well as vehicles.