Putting the Leyland National together
Page 42
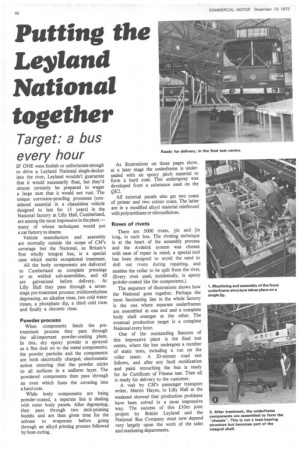
If you've noticed an error in this article please click here to report it so we can fix it.
Target: a bus every hour
IF ONE were foolish or unfortunate enough to drive a Leyland National single-decker into the river, Leyland wouldn't guarantee that it would necessarily float, but they'd almost certainly be prepared to wager a large sum that it would not rust. The unique corrosion-proofing processes (considered essential in a chassisless vehicle designed to last for 15 years) in the National factory at Lilly Hall, Cumberland,
are among the most impressive in the plant—many of whose techniques would put
a car factory to shame.
Vehicle manufacture and assembly
are normally outside the scope of CM's
coverage but the National, as Britain's first wholly integral bus, is a special case which merits exceptional treatment. All the body components are delivered to Curnberland as complete pressings or as welded sub-assemblies, and all are galvanized before delivery. At Lilly Hall they pass through a sevenstage pre-treatment process: trichlorethylene degreasing, an alkaline rinse, two cold water rinses, a phosphate dip, a third cold rinse and finally a chromic rinse.
Powder process When components finish the pretreatment process they pass through the all-important powder-coating plant. In this, dry epoxy powder is sprayed as a fine dust on to the metal components; the powder particles and the components are both electrically charged, electrostatic action ensuring that the powder sticks to all surfaces in a uniform layer. The powdered components then pass through an oven which fuses the covering into a hard coat.
While body components are being powder-coated, a separate line is dealing with outer body panels. After degreasing, they pass through two etch-priming booths and are then given time for the solvent to evaporate before going through an alkyd priming process followed by heat-curing. As illustrations on these pages show, at a later stage the underframe is undersealed with an epoxy pitch material to form a hard coat. This underspray was developed from a substance used on the QE2. All external panels also get two coats of primer and two colour coats. The latter are in a modified alkyd material reinforced with polyurethane or nitrocellulose.
Rows of rivets There are 5000 rivets, +in and iin long, in each bus. The riveting technique is at the heart of the assembly process and the Avdelok system was chosen with ease of repair in mind; a special tool has been designed to avoid the need to drill out rivets during repairing, and enables the collar to be split from the rivet. (Every rivet used, incidentally, is epoxy powder-coated like the components.) The sequence of illustrations shows how the National goes together. Perhaps the most fascinating line in the whole factory is the one where separate underframes are assembled at one end and a complete body shell emerges at the other. The eventual production target is a complete National every hour. One of the outstanding features of this impressive plant is the final test centre, where the bus undergoes a number of static tests, including a run on the roller tester. A 20-minute road test follows, and after any fault rectification and paint retouching the bus is ready for its Certificate of Fitness test. Then all is ready for delivery to the customer.
A visit by CM's passenger transport writer, Martin Hayes, to Lilly Hall at the weekend showed that production problems have been solved in a most impressive way. The success of this £10m joint project by British Leyland and the National Bus Company must now depend very largely upon the work of the sales and marketing departments.