The Advantages of
Page 50
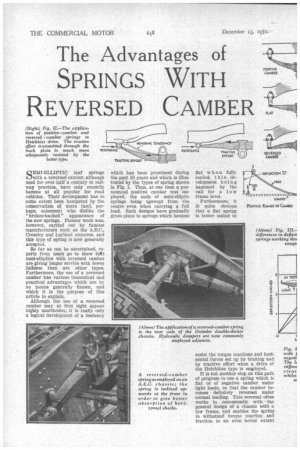
Page 51
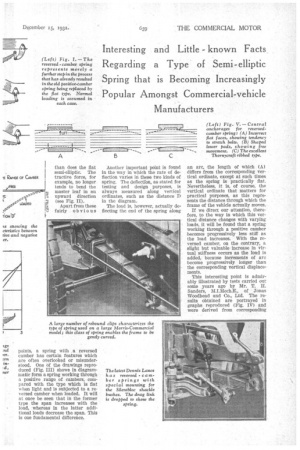
Page 52
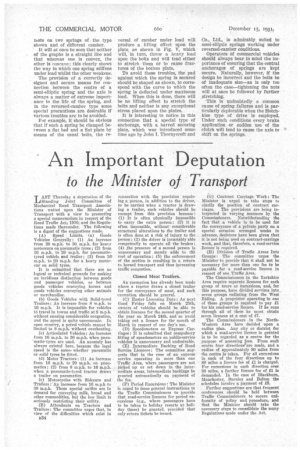
If you've noticed an error in this article please click here to report it so we can fix it.
SPRINGS WITH REVERSED CAMBER
Interesting and Little known Facts Regarding a Type of Semi-elliptic Spring that is Becoming Increasingly Popular Amongst Commercial-vehicle Manufacturers
SEMI-ELLIPTIC leaf springs with a reversed camber, although used for over half a century in railway practice, have only recently become at all popular for road vehicles. Their development has to some extent been hampered by the conservatism of users (and, perhaps, salesmen) who dislike the "broken-backed" appearance of the new springs. Pioneer work was, however, carried out by famous manufacturers such as the A.E.C.. Crossley and Leyland concerns, and this type of spring is now generally accepted.
So far as can be ascertained, reports from users go to show thilt semi-elliptics with reversed camber are giving longer service with fewer failures than are other types. Furthermore, the use of a reversed camber has various theoretical and practical advantages which are by no means generally known, and which it is the purpose of this article to explain.
Although the use of a reversed camber may at first sight appear highly unorthodox, it is really only a logical development of a tendency
which has been prominent during the past 10 years and which is illustrated by the types of spring shown in Fig. 1. Thus, at one time a pronounced positive camber was employed, the ends of semi-elliptic springs ,being upswept from the centre even when carrying a full load. Such designs have gradually given place to springs which became flat when fully loaded, this development being hastened by the call for a low frame level.
Furthermore, it is quite obvious that a fiat spring is better suited to resist the torque reactions and horizontal forces set up by braking and by tractive effort when a drive of the Hotchkiss type is employed.
It is but another step on this path of progress to use a spring which is flat or of negative camber under light loads, so that the camber becomes definitely reversed under normal loading. This reversal often works in conveniently with the general design of a chassis with a low frame, and enables thespring to withstand torque reaction and traction to an even better extent than does the flat semi-elliptic. The tractive force, for example, no longer tends to bend the master leaf in an upward direction (see Fig. ID.
Apart from these fairly obvious points, a spring with .0. reversed camber has certain features which are often overlooked or misunderstood. One of the drawings reproduced (Fig. III) shows in diagrammatic form a spring working through a positive range of cambers, compared with the type which is flat when light and is subjected to a reversed camber when loaded. It will at once be seen that in the former type the span increases with the load, whereas in the latter additional loads decrease the span. This is one fundamental difference. Another important point is found in the way in which the rate of deflection varies in these two kinds of spring. The deflection, as stated for testing and design purposes, is always measured along vertical ordinates, such as the distance I) iii the diagram..
The load is, however, actually deflecting the end of the spring along
an arc, the length of which (A) differs from the corresponding vertical ordinate, except at such times as the spring is practically flat. Nevertheless, it is, of course, the vertical ordinate that matters for practical purposes, as this represents the distance through which the frame of the vehicle actually moves.
If we direct our attention, therefore, to the way in which this vertical distance changes with varying loads, it will be found that a spring working through a positive camber becomes progressively less stiff as the load increases. With the reversed camber, on the contrary, a slight but valuable increase in virtual stiffness occurs as the load is added, because increments of are become progressively longer than the corresponding vertical displacements.
This interesting point is admirably illustrated by tests carried out some years ago by Mr. T. H. Sanders, M.I.Mech.E., of Jonas Woodhead and Co., Ltd. The results obtained are portrayed in graphs reproduced (Fig. TV) and were derived from corresponding ttSt on Iwo springs of the type shown and of different camber.
It will at once be seen that neither of the graphs is a straight line and that whereas one is convex, the other is concave ; this clearly showS the way in which one spring stiffens under load whilst the other weakens.
The provision of a correctly designed and secure means for connection between the centre of a semi-elliptic spring and the axle is always a matter of extreme importance to the life of the spring, and in the reversed-camber type some special precautions are desirable if various troubles are to be avoided.
For example, it should be obvious that if such a spring be clamped between a flat bed and a flat plate by means of the usual bolts, the re
versal of camber under load will produce a lifting effect upon the plate, as shown in Fig. V, which will, in turn, throw a heavy load upon the bolts and will tend either to stretch them or to cause fractures of the bottom plate.
To avoid these troubles, the pad against which the spring is secured should be shaped as shown, to correspond with the curve to which the spring is deflected under maximum load. When this is done, there will be no lifting effect to stretch the bolts and neither is any exceptional stress placed upon the plates.
It Is interesting to notice in this connection that a special type of anchorage, with a barred securing plate, which was introduced some time ago by John I. Thornycroft and
Co., Ltd., is admirably suited to semi-elliptic springs working under reversed-camber conditions.
Operators of commercial vehicles should always bear in mind the importance of ensuring that the central anchorages of springs are kept secure. Naturally, however, if the design be incorrect and the bolts be of inadequate size—as is only too often the case—tightening the nuts will at once be followed by further stretching.
This is undoubtedly a common cause of spring failures and is particularly deplorable when the Hotchkiss type of drive is employed. Under such conditions every brake application or sudden use of the clutch will tend to cause the axle to shift on the springs.