WELDING anc
Page 36
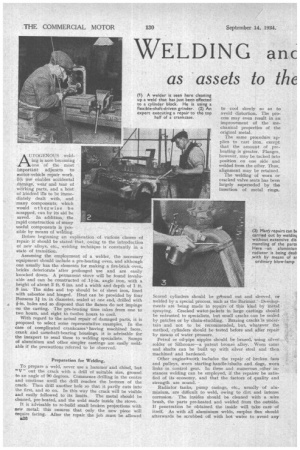
Page 37
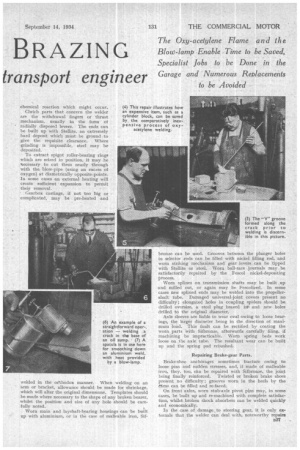
Page 38
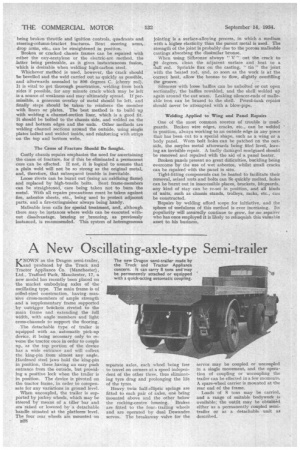
If you've noticed an error in this article please click here to report it so we can fix it.
BRAZING
as assets to the
transport engineer
1' l'O.GENOVS wold
ing is now becoming . One of the most important adjuncts to motor-vehicle repair work. Its use enables accidental damage; wear and tear of we■rking parts, and a host of kindred ills to be Mamediately dealt with, and many components, which would otherwise be scrapped, can by its aid be saved. In addition, the rapid construction of many useful components is pos
sible by means of welding. . Before beginning an explanation of various classes of repair. it should be stated that, owing to the introduction of new alloys, etc., welding technique is constantly in a state of transition.
Assuming the employment of a welder, the necessary equipment should include a pre-heating oven, and although one usually has the elements for making a fire-brick oven, bricks deteriorate ' after prolonged use and are easily knocked down. A permanent stove will be found invaluable and can be constructed of 1k-in. angle iron, with a height of about 2 ft. 6 ins, and a width and depth of 1 ft. 8 ins. The sides and top should be of sheet iron, lined with asbestos and hinged. Heat can be provided by four Bunsens 1/ in, in diameter, sealed at one end, drilled with
„ fin. holes and so disposed that the flames do not impinge on the casting. The pre-heating time takes from one to two hours, and eight to twelve hours to cool.
With regard to the actual repair of damaged parts, it is proposed to select some representative examples. In the case of complicated crankcases', having machined faces, crank and camshaft-bearing housings, it is advisable for the inexpert to send these to welding specialists. Sumps of aluminium and other simpler castings are easily weldable if the precautions referred to be observed.
Preparation for Welding.
To prepare a weld, never use a hammer and chisel, but "V" out the crack with a drill of suitable size, ground to an angle of 90 degrees. Commence drilling in the centre and continue until the drill reaches the bottom of the crack. Then drill another hole so that it partly cuts into the first, and so on. In this way the crack will be visible and easily followed to its limits. The metal should be cleaned, pm-heated, and the weld made inside the stove.
It is advisable to re-build small broken projections with new metal; this ensures that only the new piece will require facing. After the repair the job must be allowed
x26
to cool slowly so as to avoid distortion. The process may even result in an improvement of the mechanical properties of the original metal.
The same procedure applies to cast iron, except . that the amount of preheating is greater. Flanges, however, may be tacked into position on one side and welded from the other. Thus, alignment may be retained.
The welding of worn or cracked valve seats has been largely superseded by the insertion of metal rings.
Scored cylinders should be ground out and sleeved, or welded by a special process, such as the Barimar.' Developments are being made in repairs of this kind by metal spraying. Cracked water-jackets in large castings should be entrusted to specialists, but small cracks can be sealed by patches or by chain-studding. Brazing cracks is uncertain and not to be recommended, but, whatever the method, cylinders should be tested before and after repair by means of water pressure. • . •
Petrol or oil-pipe nipples should be brazed, using silversolder or Sifbronze----a patent bronze alloy. Worn cams and shafts can be built up with silver steel and then machined and hardened. •
Other enginevgavork includes the repair of broken fans and pulleys, -worn starting-handle 'shafts and dogs, worn links in control gear. In these and numerous other instances welding can be employed, if the repairer be satisfied of its economy, and that the factors of quality and strength are sound.
Radiator tanks, pump casings, etc., usually of aluminium, are difficult to weld, owing to dirt and intense corrosion. The insides should be cleaned with a wire brush, the parts pre-heated and welded from the outside. If penetration be obtained the inside will take care of itself. As with all aluminium welds, surplus flux should afterwards be scrubbed off with hot water to avoid any
chemical reaction which might occur.
Clutch parts that concern the welder are the withdrawal 'fingers or thrust mechanism, usually in the form of radially disposed levers. The ends can be built up with Stelae, an extremely hard deposit which must be ground to give the requisite clearance. Where -grinding is impossible, steel may be deposited.
To extract spigot roller-bearing rings which are seized in position, it may be Tiecessary to cut them nearly through with the blow-pipe (using an excess of oxygen) at diametrically opposite points In some cases an external heating will create sufficient expansion to pernait their removal.
Gearbox Castings, if not too big or complicated, may be pre-heated and welded in the orkhodox manner. When welding on an arm or bracket, allowance should be made for shrinkage, which will alter the original dimensions. Templates should be made where necessary to the shape of any broken bearer, whilst the position and size of any hole should be carefully noted.
Worn main and layshaft-bearing housings can he built up with aluminium, or in the case of malleable iron, Sit
bronze can be used. Grooves between the plunger holes in selector .rods can be filled with nickel filling rod, and worn striking mechanism and gear levers can be tipped with Stellite or steel. Worn ball-race journals may be satisfactorily repaired by the Fescol nickel-depositing process.
Worn splines on transmission shafts may be built up and milled out, or again may be Feseolizecl. In some cases new splined ends may be welded into the propellershaft tube. Damaged universal-joint covers present no difficulty ; elongated holes in coupling spiders _should be drilled oversize, a steel plug brazed in' and new holes drilled to the original diameter.
Axle sleeves are liable to wear oval owing to loose bearings, the larger diameter being in the direction of maximum load.. This fault can be rectified by coating the worn parts with Sifbronze, afterwards carefully filing, if machining be impracticable. Worn spring beds work loose on the axle tube. The resultant wear can be built up and the spring pad rebushed.
Repairing Brake-gear Parts.
Brake-shoe anchorages sometimes fracture owing to loose pins and sudden stresses, and, if made of malleable iron, they, too, can be repaired with Sifbronze, the joint being finally reinforced. Twisted or broken brake shoes present no difficulty; grooves worn in the heels by the ms can be filled and re-faced:
On front axles, worn stub-axle pivot pins may, in some cases, be built up and re-machined with complete satisfaction, whilst broken shock absorbers can be welded quickly and economically.
In the case of damage to steering gear, it is only externals that the welder can deal with, noteworthy repairs
being brolean throttle and ignition controls, quadrants and steering-columusbracket fractures. Bent steering arms, drop arms, etc„ can be straightened in position.
Broken or cracked chassis frames can he repaired with either the oxy-acetylene or the electric-arc method, the latter being preferable, as it gives instantaneous fusion. which is desirable when welding high-carbon steel.
Whichever method is used, however, the crack should be bevelled and the weld carried out as quickly as possible, and afterwards annealed to 800 degrees C. (cherry red). It is vital to get thorough penetration, welding from both sides if possible, for any minute crack which may be left is a source of weakness and may ultimately spread. If permissible, a generous overlay of metal should be left, and finally steps should be taken to reinforce the member with liners or plates. The best method is to build up with welding a channel-section liner, which is a good fit. It should be bolted to the chassis side, and welded on the top and bottom edges and the ends. Other methods are welding channel sections around the outside, using single plates bolted and welded inside, and reinforcing with strips on the top and bottom webs.
The Cause of Fracture Should Be Sought.
Costly chassis repairs emphasize the need for ascertaining the cause of fracture, for if this be eliminated a permanent cure can he effected. If not, it is logical to assume that a plain weld will not be so strong a.s the original metal, and, therefore, that subsequent trouble is inevitable.
Loose rivets can be burnt out (using an oxidizing flame) and replaced by high-tensile bolts. Bent frame-members can be straightened, care being taken not to burn the metal. With all repairs precautions must be taken against fire, asbestos sheets, etc., being used to protect adjacent parts, and a fire-extingeisher always being handy.
Malleable iron calls for special treatment, and, although there may be instances where welds can be executed without disadvantage, brazing or bronzing, as previously instanced, is recommended. This system of heterogeneous
jointing is a surface-alloying process, in which a medium with a higher elasticity than the parent metal is used. The strength of the joint is probably due to the porous malleable castings absorbing the dissimilar bronze.
When using Sifbronze always " V " out the crack to 20 degrees, clean the adjacent surface and heat to a lull red. Sprinkle flux on the casting, " tin " the joint with the heated rod, and, so soon as the work is at the correct heat, allow the bronze to flow, slightly overfilling
the groove, a • Silencers with loose baffles can be unbolted or cut open sectionally, the baffles rewelded, and the shell welded up again around the cut seam. Leaking silencer-ends of malleable iron can be brazed to the shell. Petrol-tank repairs should never be attempted with a blow-pipe.
Welding Applied to Wing and Panel Repairs One of the most common sources of trouble is mudguards. Broken wire edges, cracks, etc., can be welded in position, always working to an outside edge in any piece that has been cut to a special shape, such as a wing or a body panel. Worn bolt holes can be patched on the outside, the surplus metal afterwards being filed level, leaving an invisible repair. A badly damaged mudguard should be removed and repaired with the aid of a panel beater.
Broken panels present no great difficulties, buckling being overcome by the use of wet asbestos, whilst small cracks can be repaired with the panel in situ.
Tight-fitting components can be heated to facilitate their removal, seized nuts and bolts can He quickly melted, holes can be burnt out in inaccessible places, brackets, lifeguards, any kind of stay can be re-set in position, and all kinds of units, such as chassis stands, trolleys, racks. etc., can be constructed.
Repairs by welding afford scope for initiative, and the sphere of usefulness of this method is ever increasing. Its popularity will assuredly continue to grow, for no repairer who has once employed it is likely to relinquish this valuable asset to his business.