.LIONS of people take it granted that their daily rspaper
Page 123
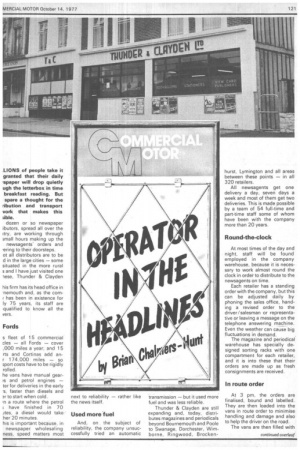
Page 124
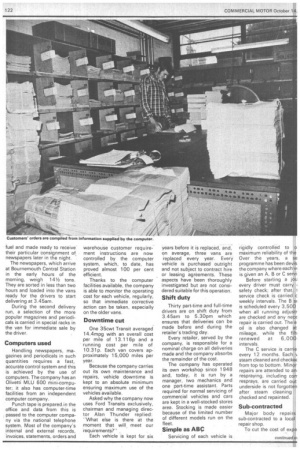
Page 126
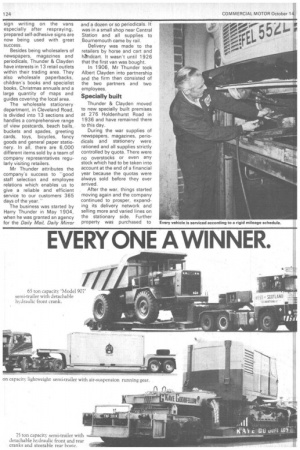
Page 127

If you've noticed an error in this article please click here to report it so we can fix it.
will drop quietly ugh the letterbox in time breakfast reading. But spare a thought for the ribution and transport vork that makes this tible.
dozen or so newspaper ibutors, spread all over the itry, are working through small hours making up the newsagents' orders and 'en rig to their doorsteps.
ot all distributors are to be d in the large cities — some situated in the more rural s and I have just visited one -lose, Thunder & Clayden his firm has its head office in -nemouth and, as the corn
has been in existence for ly 75 years, its staff are hqualified to know all the vers.
Fords
s fleet of 15 commercial ales — all Fords — cover ,000 miles a year; and 15 rts and Cortinas add an 1 74,000 miles — so 3port costs have to be rigidly rolled.
he vans have manual gear and petrol engines — ter for deliveries in the early s, faster than diesels and ?,r to start when cold.
hn a route where the petrol ; have finished in 70 Jtes, a diesel would take her 20 minutes.
his is important because, in newspaper wholesaling ness, speed matters most
Used more fuel
And, on the subject of reliability, the company unsuccessfully tried an automatic transmission — but it used more fuel and was less reliable
Thunder & Clayden are still expanding and, today, distributes magazines and periodicals beyond Bournemouth and Poole to Swanage, Dorchester, VVimborne, Ringwood, Brocken
hurst, Lymington and all areas between these points — in all 320 retailers.
All newsagents get one delivery a day, seven days a week and most of them get two deliveries. This is made possible by a team of 54 full-time and part-time staff some of whom have been with the company more than 20 years.
Round-the-clock
At most times of the day and night, staff will be found employed in the company warehouse, because it is necessary to work almost round the clock in order to distribute to the newsagents on time.
Each retailer has a standing order with the company, but this can be adjusted daily by phoning the sales office, handing a revised order to the driver/salesman or representative or leaving a message on the telephone answering machine. Even the weather can cause big fluctuations in demand.
The magazine and periodical warehouse has specially designed sorting racks with one compartment for each retailer, and it is into these that their orders are made up as fresh consignments are received.
In route order
At 3 pm, the orders are finalised, bound and labelled. They are then loaded into the vans in route order to minimise handling and damage and also to help the driver on the road.
The vans are then filled with
fuel and made ready to receive. their particular consignment of newspapers later in the night. .
The newspapers, which arrive at Bournemouth Central Station in the early hours of the morning, weigh 141/2 tons. They are sorted in less than two hours and loaded into the vans ready for the drivers to start delivering at 3.45am.
During the second delivery run, a selection of the more popular magazines and periodicals is carried in special racks in the van for immediate sale by the driver.
Computers used
Handling newspapers, magazines and periodicals in such quantities requires a fast, accurate control system and this is achieved by the use of computers. The company has an Olivetti MLU 600 mini-computer; it also has computer-time facilities from an independent computer company.
Punch tape is prepareckin the office and data from this is passed to the computer company via the national telephone system. Most of the company's internal and external records, invoices, statements, orders and warehouse customer requirement instructions are now controlled by the computer system, which, to date, has proved almost 100 per cent efficient, Thanks to the computer facilities available, the company is able to monitor the operating cost for each vehicle, regularly, so that immediate corrective action can be taken, especially on the older vans.
Downtime cut
One 35cwt Transit averaged 14.4mpg with an overall cost per mile of 13.116p and a running cost per mile of . 10.31p. Each van covers approximately 15,000 miles per year.
Because the company carries out its own maintenance and repairs, vehicle downtime is kept to an absolute minimum ensuring maximum use of the vehicles available.
Asked why the company now uses Ford Transits exclusively, chairman and managing director Alan Thunder replied: -What else is there at the moment that will.. meet our -requirements?" ,
Each vehicle is kept for six years before it is replaced, and, on average, three vans are replaced every year. Every vehicle is purchased outright and not subject to contract hire or leasing agreements. These aspects have been thoroughly investigated but are not considered suitable for this operation.
Shift duty
Thirty part-time and full-time drivers are on shift duty from 3.45am to 5.30pm which ensures that deliveries can be made before and during the retailer's trading day.
Every retailer, served by the company, is responsible for a nominal charge on all deliveries made and the company absorbs the remainder of the cost.
The company has operated its own workshop since 1 948 and, today, it is run by a manager, two mechanics and one part-time assistant. Parts required for normal servicing of commercial vehicles and cars are kept in a well-stocked stores area. Stocking is made easier because of the limited number of different models run on the fleet.
Simple as ABC
Servicing of each vehicle is rigidly controlled to o maximum reliability of the Over the years, a se programme has been devis the company where each vi is given an A, B or C servi Before starting a jou every driver must carry I safety check; after that, 1 service check is carried c weekly intervals. The B si is scheduled every 3,500 when all running adjustr are checked and any nece repair is carried out. The e oil is also changed at mileage, while the filt, renewed at 6,000. intervals.
The C service is carrie every 12 months. Each s, steam cleaned and checket from top to bottom. Minor repairs are attended to an respraying, including conresprays, are carried out underside is not forgotten after steam cleaning checked and repainted.
Sub-contracted
Major body repairs sub-contracted to a local repair shop.
To cut the cost of expe sign sign writing on the vans especially after respraying, prepared self-adhesive signs are now being used with great success.
Besides being wholesalers of newspapers, magazines and periodicals, Thunder & Clayden have interests in 13 retail outlets within their trading area. They also wholesale paperbacks, children's books and specialist books. Christmas annuals and a large quantity of maps and guides covering the local area.
The wholesale stationery department, in Cleveland Road, is divided into 13 sections and handles a comprehensive range of view postcards, beach balls, buckets and spades, greeting cards, toys, bicycles, fancy goods and general paper stationery. In all, there are 6,000 different items sold by a team of company representatives regularly visiting retailers.
Mr Thunder attributes the company's success to -good staff selection and employee relations which enables us to give a reliable and efficient service to our customers 365 days of the year.
The business was started by Harry Thunder in May 1904, when he was granted an agency for the Daily Mail, Daily Mirror and a dozen or so periodicals. It was in a small shop near Central Station and all supplies to Bournemouth came by rail.
Delivery was made to the retailers by horse and cart and hhdcart. It wasn't until 1926 that the first van was bought.
In 1906, Mr Thunder took Albert Clayden into partnership and the firm then consisted of the two partners and two employees.
Specially built
Thunder & Clayden moved to new specially built premises at 276 Holdenhurst Road in 1936 and have remained there to this day.
During the war supplies of newspapers, magazines, periodicals and stationery were rationed and all supplies strictly controlled by quota. There were no overstocks or even any stock which had to be taken into account at the end of a financial year because the quotas were always sold before they ever arrived.
After the war, things started moving again and the company continued to prosper, expanding its delivery network and selling more and varied lines on the stationary side. Further property was purchased to accommodate the expanding business.
Pool system
A pool delivery system for the distribution of national morning newspapers was inaugurated in which Bournemouth's three newspaper wholesalers co-operated and it continues in a slightly modified form. The old practice of making up the orders of the daily papers at Central Station each morning was discontinued with the advent of what was termed train packing.
Supplies for each retailer were packed aboard the train during the journey from Waterloo to Bournemouth Central. On arrival, the orders were loaded into the vans and distributed to all retailers in the Bournemouth and Poole area.
With the advent of highspeed trains, however, there was not sufficient time to prepare all the orders on the train, so the older method had to be reverted to.
Significant years
Earlier, the company itself had undertaken a change, when, in 1957, the old partnership was dissolved. Subsequently, Thunder & Clayden was declared a limited company.