Hub of the matter • After a lapse of several
Page 49
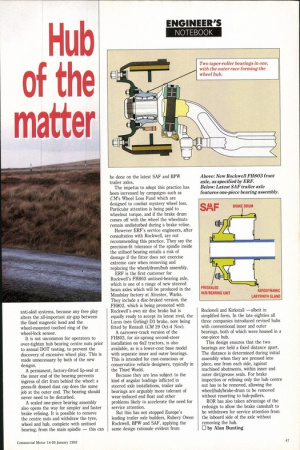
Page 48
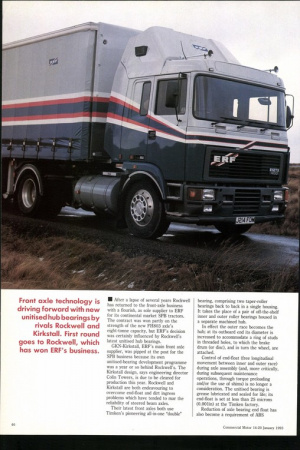
If you've noticed an error in this article please click here to report it so we can fix it.
years Rockwell has returned to the front-axle business with a flourish, as sole supplier to ERF for its continental market SPB tractors. The contract was won partly on the strength of the new FH803 axle's eight-tonne capacity, but ERF's decision was certainly influenced by Rockwell's latest unitised hub bearings.
GKN-Kirkstall, ERF's main front axle supplier, was pipped at the post for the SPB business because its own unitised-bearing development programme was a year or so behind Rockwell's. The Kirkstall design, says engineering director Colin Towers, is due to be cleared for production this year. Rockwell and Kirkstall are both endeavouring to overcome end-float and dirt ingress problems which have tended to mar the reliability of steered beam axles.
Their latest front axles both use Timken's pioneering all-in-one "double" bearing, comprising two taper-roller bearings back to back in a single housing. It takes the place of a pair of off-the-shelf inner and outer roller bearings housed in a separate machined hub.
In effect the outer race becomes the hub; at its outboard end its diameter is increased to accommodate a ring of studs in threaded holes, to which the brake drum (or disc), and in turn the wheel, are attached.
Control of end-float (free longitudinal movement between inner and outer race) during axle assembly (and, more critically, during subsequent maintenance operations, through torque preloading and/or the use of shims) is no longer a consideration. The unitised bearing is grease lubricated and sealed for life; its end-float is set at less than 25 microns (0.001in) at the Timken factory.
Reduction of axle bearing end float has also become a requirement of ABS anti-skid systems, because any free play alters the all-important air-gap between the fixed magnetic head and the wheel-mounted toothed ring of the wheel-lock sensor.
It is not uncommon for operators to over-tighten hub bearing centre nuts prior to annual DOT testing, to prevent the discovery of excessive wheel play. This is made unnecessary by both of the new designs.
A permanent, factory-fitted lip-seal at the inner end of the bearing prevents ingress of dirt from behind the wheel: a press-fit domed dust cap does the same job at the outer end. The bearing should never need to be disturbed.
A sealed one-piece bearing assembly also opens the way for simpler and faster brake relining. It is possible to remove the centre nuts and withdraw the tyre, wheel and hub, complete with unitised bearing, from the main spindle — this can be done on the latest SAF and BPW trailer axles.
The impetus to adopt this practice has been increased by campaigns such as CM's Wheel Loss Fund which are designed to combat mystery wheel loss. Particular attention is being paid to wheelnut torque, and if the brake drum comes off with the wheel the wheelnuts remain undisturbed during a brake reline.
However ERF's service engineers, after consultation with Rockwell, are not recommending this practice. They say the precision-fit tolerance of the spindle inside the utilised bearing entails a risk of damage if the fitter does not exercise extreme care when removing and replacing the wheel/drum/hub assembly.
ERF is the first customer for Rockwell's FH803 unitised-bearing axle, which is one of a range of new steered beam axles which will be produced in the Maudslay factory at Alcester, Warks. They include a disc-braked version, the FH802, which is being promoted with Rockwell's own air disc brake but is equally ready to accept its latest rival, the Lucas (née Girling) D3 brake, now being fitted by Renault (CM 29 Oct-4 Nov).
A narrower-track version of the FH803, for air-sprung second-steer installation on 6x2 tractors, is also available, as is a lower-cost base model with separate inner and outer bearings. This is intended for cost-conscious or conservative vehicle designers, typically in the Third World.
Because they are less subject to the kind of angular loadings inflicted in steered axle installations, trailer axle bearings are arguably more tolerant of wear-induced end float and other problems likely to accelerate the need for service attention.
But this has not stopped Europe's leading trailer axle builders, Rubery Owen Rockwell, BPW and SAF, applying the same design rationale evident from Rockwell and Kirkstall —albeit in simplified form. In the late eighties all three companies introduced revised hubs with conventional inner and outer bearings, both of which were housed in a one-piece hub.
This design ensures that the two bearings are held a fixed distance apart. The distance is determined during initial assembly when they are pressed into place, one from each side, against machined abutments, within inner and outer dirt/grease seals. For brake inspection or relining only the hub centre nut has to be removed, allowing the wheel/hub/brake-drum to be removed without resorting to hub-pullers.
ROR has also taken advantage of the redesign to allow the brake camshaft to be withdrawn for service attention from the inboard side of the axle without removing the hub.
by Alan Bunting