So you thought you knew all about York?
Page 22
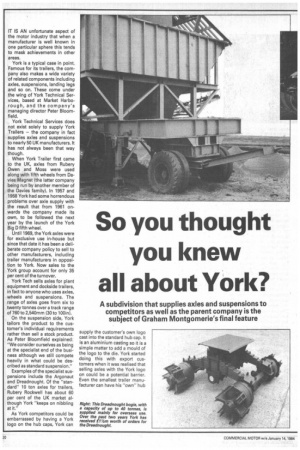
Page 23
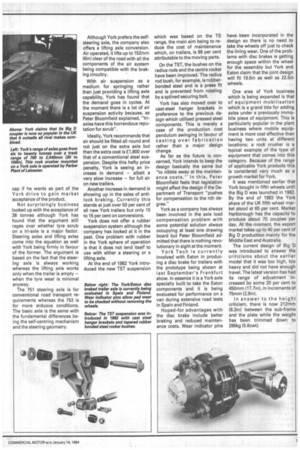
If you've noticed an error in this article please click here to report it so we can fix it.
A subdivision that supplies axles and suspensions to competitors as well as the parent company is the subject of Graham Montgomerie's final feature
IT IS AN unfortunate aspect of the motor industry that when a manufacturer is well known in one particular sphere this tends to mask achievements in other areas.
York is a typical case in point. Famous for its trailers, the cornpany also makes a wide variety of related components including axles, suspensions, landing legs and so on. These come under the wing of York Technical Services, based at Market Harborough, and the company's managing director Peter Bloomfield.
York Technical Services does not exist solely to supply York Trailers — the company in fact supplies axles and suspensions to nearly 50 UK manufacturers. It has not always been that way though.
When York Trailer first came to the UK, axles from Rubery Owen and Moss were used along with fifth wheels from Davies Magnet (the latter company being run by another member of the Davies family). In 1957 and 1958 York had some horrendous problems over axle supply with the result that from 1961 onwards the company made its own, to be followed the next year by the launch of the York Big D fifth wheel.
Until 1969, the York axles were for exclusive use in-house but since that date it has been a deliberate company policy to sell to other manufacturers, including trailer manufacturers in opposition to York. Now sales to the York group account for only 35 per cent of the turnover.
York Tech sells axles for plant equipment and dockside trailers, in fact to anyone who uses axles, wheels and suspensions. The range of axles goes from six to twenty tonnes over a track range of 760 to 2,540mm (30 to 100in).
On the suspension side, York tailors the product to the customer's individual requirements rather than sell a stock product. As Peter Bloomfield explained: "We consider ourselves as being at the specialist end of the business although we still compete heavily in what could be described as standard suspension."
Examples of the specialist suspensions include the Argonaut and Dreadnought. Of the "standard" 10 ton axles for trailers, Rubery Rockwell has about 60 per cent of the UK market although York "keeps on nibbling at it."
As York competitors could be embarrassed by having a York logo on the hub caps, York can supply the customer's own logo cast into the standard hub cap. It is an aluminium casting so it is a simple matter to add a mould of the logo to the die. York started doing this with export customers when it was realised that selling axles with the York logo on could be a potential barrier. Even the smallest trailer manufacturer can have his "own" hub cap if he wants as part of the York drive to gain market acceptance of the product.
Not surprisingly business looked up with the acceptance of 38 tonnes although York has found that the argument still rages over whether tyre scrub on a tri-axle is a major factor. Steering axles and lifting axles come into the equation as well with York being firmly in favour of the former. The argument is based on the fact that the steering axle is always working whereas the lifting axle works only when the trailer is empty — when the tyre wear is minimal anyway.
The 751 steering axle is for conventional road transport requirements whereas the 753 is for more arduous conditions. The basic axle is the same with the fundamental differences being the self-centring mechanism and the steering geometry. Although York prefers the selfsteering axle, the company also offers a lifting axle conversion. Air operated, it lifts up to 152mm (6in) clear of the road with all the components of the air system being compatible with the braking circuitry.
With air suspension as a medium for springing rather than just providing a lifting axle capability, York has found that the demand goes in cycles. At the moment there is a lot of air suspension activity because, as Peter Bloomfield explained, "triaxles have this horrendous reputation for scrub".
Ideally, York recommends that air should be fitted all round and not just on the extra axle but then the extra cost is £1,800 over that of a conventional steel suspension. Despite this hefty price penalty, York is seeing an increase in demand — albeit a very slow increase — for full air on new trailers.
Another increase in demand is showing up in the sales of antilock braking. Currently this stands at just over 50 per cent of all new York trailers but only 10 to 15 per cent on conversions.
York does not offer a rubber suspension system although the company has looked at it in the past. One problem with rubber in the York sphere of operation is that it does not lend itself to use with either a steering or a lifting axle.
At the end of 1982 York introduced the new TST suspension which was based on the TS range, the main aim being to reduce the cost of maintenance which, on trailers, is 99 per cent attributable to the moving parts.
On the TST, the bushes on the radius rods and the centre rocker have been improved. The radius rod bush, for example, is rubberbonded steel and is a press fit and is prevented from rotating by a splined securing bolt.
York has also moved over to cast-steel hanger brackets in preference to the previous design which utilised pressed steel components. This is merely a case of the production cost pendulum swinging in favour of casting over fabrication rather than a major design change.
As far as the future is concerned, York intends to keep the design basically the same but "to nibble away at the maintenance costs." In this, Peter Bloomfield feels that legislation might affect the design if the Department of Transport "pushes for compensation to the nth degree."
York as a company has always been involved in the axle load compensation problem with some potential solution always occupying at least one drawing board but Peter Bloomfield admitted that there is nothing revolutionary in sight at the moment.
York Tech is currently involved with Eaton in producing a disc brake for trailers with the prototype being shown at last September's Frankfurt show. In essence it is a York axle specially built to take the Eaton components and it is being evaluated for performance on a van during extensive road tests in Spain and Finland.
Hoped-for advantages with the disc brake include better braking and reduced maintenance costs. Wear indicator pins have been incorporated in the design so there is no need to take the wheels off just to check the lining wear. One of the problems with disc brakes is getting enough space within the wheel for the assembly but York and Eaton claim that the joint design will fit 19.5in as well as 22.5in wheels.
One area of York business which is being expanded is that of equipment mobilisation which is a grand title for adding axles under a previously immobile piece of equipment. This is particularly popular in the plant business where mobile equipment is more cost effective than having two units at different locations; a rock crusher is a typical example of the type of equipment that comes into this category. Because of the range of applicable York products this is considered very much as a growth market for York.
It was mentioned earlier that York bought in fifth wheels until the Big D was launched in 1962. By the end of 1983 the York share of the UK fifth wheel market stood at 65 per cent. Market Harborough has the capacity to produce about 70 couples per day. At the moment, the export market takes up to 40 per cent of Big D production mainly for the ' Middle East and Australia.
The current design of Big D was introduced to answer the criticisms about the earlier model that it was too high, too heavy and did not have enough travel. The latest version has had its range of adjustment increased by some 20 per cent to 450mm (17.7in), in increments of 75mm (2.9in).
In answer to the height criticism, there is now 212mm (8.3in) between the sub-frame and the plate while the weight has been trimmed down to 286kg (5.6cwt).