THE VAST POST
Page 40
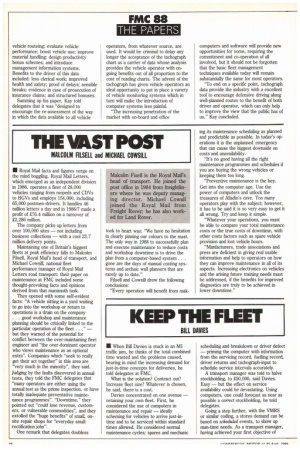
If you've noticed an error in this article please click here to report it so we can fix it.
MALCOLM RIAU and MICHAEL COWSILL
• Royal Mail facts and figures verge on the mind boggling. Royal Mail Letters, which emerged as an independent division in 1986, operates a fleet of 28,000 vehides ranging from mopeds and CDVs to HGVs and employs 154,000, including 65,000 postmen-drivers. It handles 46 million letters a day and in 1986/7 made a profit of £76.4 million on a turnover of £2,286 million.
The company picks up letters from over 100,000 sites — not including business collections — with a cool 23.7 million delivery points.
Maintaining one of Britain's biggest fleets at peak efficiency falls to Malcolm Filsell, Royal Mail's head of transport, and Michael Cowsill, national fleet performance manager of Royal Mail Letters road transport: their paper on maintenance at FMC included some thought-provoking facts and opinions derived from that mammoth task.
They opened with some self-evident facts: "A vehicle sitting in a yard waiting to go into the workshop or return to operations is a drain on the company . . . good workshop and maintenance planning should be critically linked to the particular operation of the fleet. . ." — but they warned of the potential for conflict between the over-maintaining fleet engineer and "the over-dominant operator who views maintenance as an optional extra". Companies which "seek to really get their act together" in this area are "very much in the minority", they said. Judging by the faults discovered in annual tests, they told the FMC delegates that "many operators are either using the annual test as the prime inspection, or have totally inadequate preventative maintenance programmes". "Downtime," they pointed out "could lose revenue, customers, or vulnerable commodities", and they extolled the "huge benefits" of small, onsite repair shops for "everyday small rectification jobs".
One remark that delegates doubless took to heart was: "We have no hesitation in dearly pinning our colours to the mast_ The only way in 1988 to successfully plan and execute maintenance to reduce costs and workshop downtime is to drive the plan from a computer-based system. . gone are the days of manual costing systems and archaic wall planners that are rarely up to date."
Filsell and Cowsill drew the following conclusions: "Every operation will benefit from mak ing its maintenance scheduling as planned and predictable as possible. In today's operations it is the unplanned emergency that can cause the biggest downside on costs and unavailability.
"It's no good having all the right maintenance programmes and schedules if you are buying the wrong vehicles or keeping them too long.
"Preventive maintenance is the key. Get into the computer age. Use the power of computers and unlock the treasures of Alladin's cave. Too many operators play with the subject; however, it has to be said it is so very easy to get it all wrong. Try and keep it simple.
"Whatever your operations, you must be able to compare your total maintenance costs or the true costs of downtime, with other costs factors such as spare vehicle provision and lost vehide hours.
"Manfacturers, trade associations and press are deficient in giving real usable information and help to operators on how they can improve maintenance in all of its aspects. Increasing electronics on vehicles and the arising future training needs must be addressed, if the benefits for improved diagnostics are truly to be achieved in lower downtime."