Chains for Power Transmission.*
Page 14
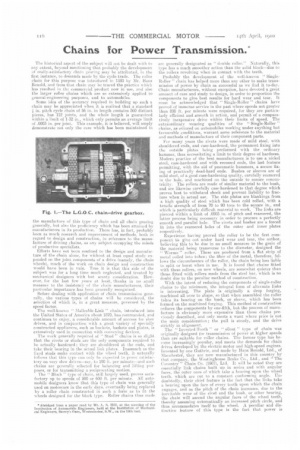
Page 15
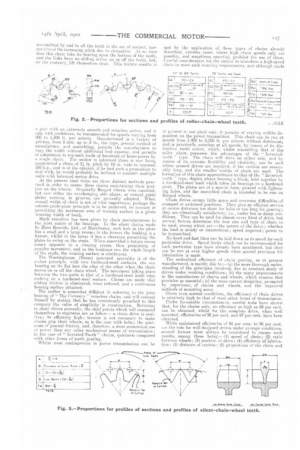
Page 16
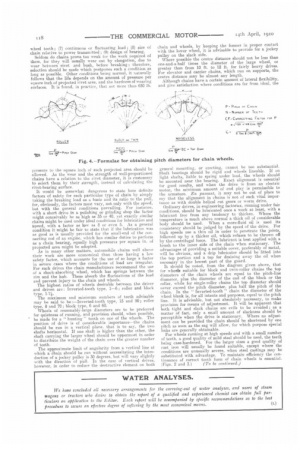
If you've noticed an error in this article please click here to report it so we can fix it.
The historical aspect of the subject will not be dealt with to any extent, beyond mentioning that probably the development of really-satisfactory chain gearing may be attributed, in the first instance, to demands made by the cycle trade. The roller chain for this purpose was introduced in 1880 by Mr. HILI1S Reuold, and from that chain may be traced the practice e hich has resulted in tho commercial product now in use, and also the larger roller chains which are so extensively applied to general-engineering purposes, and to automobiles.
Some idea of the accuracy required in building up such a chain may be appreciated when it is realized that a standard in. pitch cycle chain of 56 in. in length contains 560 distinct pieces, has 112 joints, and the whole length is guaranteed within a limit of 1-32 in., which only permits an average limit of .0003 in. per joint. This example, it is believed, will amply demonstrate not only the care which has been maintained in
the manufacture of this type of chain and all chain gearing generally, but also the proficiency which has been attained by manufacturers in its production. There has, in fact, probably been as much research and improvement of methods, both in regard to design and construction, in reference to the manufacture of driving chains, as any subject occupying the minds of productive specialists.
Efforts have not been confined to the design and manufacture of the chain alone, for without at least equal study expended on the joint, components of a drive (namely, the chain wheels), much of the work on chain design and construetinn would have been in vain. Trne it is that this side of the snbject was for a long time much neglected. and treated by mechanical designers with but scanty consideration. However, for the last few years at least, thanks in no small measure to the insistency of the chain manufacturers, their particular importance has been generally recognized. Before dealing with application of chain transmission generally, the various types of chains will be considered, the selection of which is, in a great measure, governed by the speed factor.
The well-known " Malleable-Link '' chain, introduced into the United States of America about 1870, has commanded, and continues to enjoy, a cousiderable amount of success for slow drives, and in conjunction with a great variety of specially constructed appliances, euch as buckets, baskets and plates, is extensively used in connection with conveying devices.
The work generally required of " Stud " chains is so _slight that the rivets or studs are the only components required to be actually hardened; they are shouldered at the ends, and take their bearing in the actual link plates. Inasmuch as the fixed studs make contact with the wheel teeth, it naturally fellows that this type can culy be expected to prove satisfactnry on very slow drives—say, to 100 ft. per minute—and such chains are generally selected for balancing and lifting purposes, or for transmitting a reciprocating motion. The " Block " type of chain, still largely used, proves satisfactory up to speeds of 500 or 500 ft. per minute. All automobile designers know that this type of chain was generally used on motorcars in the early days, eventually being replaced by a roller chain cunstructed in such a form as to fit the wheels designed for the block type. Roller chains thus made
are generally designated as " double roller." Naturally, this type has a much smoother action than the solid block—due to the rollers revolving when in contact with the teeth. Probably the development of the well-known " SingleRoller " chain has helped more than airy other to make transmission of power by chain as successful as we find it to-day. Chain manufacturers, without exception, have devoted a great amomit of care and study to design, in order to proportion the components to give best results for hard wear and tear. It must be acknowledged that " Single-Roller " chains have proved of immense service in the past where speeds not, greater than 800 ft. per minute were required, for they are particularly efficient and smooth in action, and permit of a comparatively inexpensive drive within their limits of speed. The extraordinary wearing qualities of the " Single-Roller " chains, as evinced on automobiles working under anything hut favourable conditions, warrant some reference to the material and methods of manufacture of their component parts.
Fer many years the rivets were made of mild steel, with shouldered ends, and case-hardened, the permanent fixing into the outside plates being performed with the ordinary hammer, thus necessitating a limit to their degree of hardness. Modern practice of the hest manufacturers is to use a nickel steel, case-hardened and with recessed ends, the last feature permitting, with the aid of pneumatic hammers, a secure
uf practically dead-hard ends. Bushes or sleeves are of mild steel, of a good case-hardening quality, carefully reamered in the hole, and machined on the outside to ensure concentricity. The rollers are made of similar material to the bush, and are likewise carefully case-hardened to that degree which proves best to withstand shock and prevent liability to fracture when in actual use. The side plates are blankings from a high quality of steel which has been cold rolled, with a tensile strength of from 70 to 90 tons to the square in., and which is particularly difficult material to work. The links are pierced within a limit of .0005 in. of pitch and reamered, the latter process being necessary in order to procure a perfectly smooth and parallel hole. The rivets and bushes are a forced fit into the reamered holes of the outer and inner plates respectively.
Experience having proved the roller to be the first component to give out under hard wear and tear, the author, believing this to be due in no small measure to the grain of the material being transverse to the diameter., designed the " Wormo " roller. These are produced from a flat strip of meted coiled into tubes; the fibre of the metal, therefore, follows the circumference of the roller, the chain being leas liable to split or burst when in use. It is found that chains fitted with these rollers, on new wheels, are somewhat quieter than those fitted with rollers made from the steel bar, which is no doubt due to the peculiar method of construction.
With the intent of reducing the components of single-roller chains to the. minimum, the integral form of alternate links is interesting. The plate is originally a drop forging, machined all over to shape, so that when assembled the roller takes its bearing on the bush, or sleeve, which has been formed on the machined forging. This method of construction reduces the components by one-fifth, but the process of manufacture is obviously more expensive than those chains previously described, and only meets a want where price is not the main consideration ; the pull is steady, and the drive strictly in alignment..
The "Inverted-Tooth " or " silent," type of chain was originally designed for transmission of power at higher speeds than are suitable for roller chains. The former type has become increasingly popular, and meets the demands for chain drives developed by the electric motor and high-speed engines. Invented by one Guthrie, and made by Hans Renold, Ltd., of fanchester, they are now manufactured in this country by that company. the Westinghouse Brake Co., Ltd., and " The Coventry ' Chain Co. (1907), Ltd. It will be noted they are essentially link chains built up in series and with angular faces, the outer ones of. which take a bearing upon the wheel teeth. which are cut to a constant conforming angle. Undoubtedly, their chief feature is the fact that the links take a bearing upon the face of every tooth upon which the chain engages, and as the pitch of the chain increases, due to the inevitable wear of the rivet and the bush, or other hearing, the chain will ascend the angular faces of the wheel teeth, thereby assuming automatically an increased pitch circle, and thus accommodates itself to the wheel. A peculiar and distinctive featnre of this type is the fact that power is
transmitted by and to all the teeth in the are of contact, irrespective of the increasing pitch due to elongation. At no time does this chain take its bearing upon the bottom of the teeth, and the links have no sliding action on or off the teeth, but, on the contrary, lift themselves clear. This feature results in
a gear with all extremely smooth and noiseless action, and it can, with confidence, be recommended for speeds varying from 800 to 1,300 It, per minute. 'Manufactured in a variety of pitches, from 8 mm. up to 3 in., the type. general method of manufacture, and assembling, permits the manufacturer to vary the width without additional tool expense, and permits of adaptation to transmit loads of hundreds of horse-power by iL single chain. The author is informed there is now being constructed a chain of 2;1 in. pitch by 18 in. wide to transmit. 350 h.p., and is of the opinion, if he had such a proposition to deal with, he would probably be inclined to consider multiple units with balanced spring (-Give.
At the. present time there are three distinct methods practised in order to ensure these chains maintaining their position on the wheels. Originally flanged wheels were essential, but now either the overhanging side plates, or central guide plates running in grooves, are generally adopted. When overall width of chain is not of vital importance, perhaps the outside-guide-plate principle is to he preferred. on account of permitting the maximum area of wearing surface in a given working width of tooth.
Much attention has been given by chain manufacturers to the _joint action of the hearings. In the silent chains made by Hans Renolds. Ltd., of Manchester. each hole in the plate has a small and a large recess ; in the former the bushing is a fixture, whilst in the latter it has a clearance permitting the plates to swing on the studs. When assembled a fixture recess comes opposite to a clearing recess, thus permitting of angular movement., and as the bushings run the whole length of the studs, the wearing surface is continuous.
The Westinghouse (Morse) patented speciality is of the rocker principle, with two hardened-steel surfaces, the one bearing on its flat face the edge of the other when the chain moves on or off the chain wheel. The movement taking place between the two parts is that of a hardened-steel knife edge rocking on a hardened-steel surface. Claims are made that sliding friction is eliminated, wear reduced, and a continuous bearing surface obtained. The author is somewhat diffident in referring to the joint bearing of " The Coventry " noiseless chains, and will content himself by stating that he has consistently preached to this company the value of simplicity in construction. Referring to chain drives generally, the chief points which will commend themselves to engineers are as follow :--a chain drive is positive; its efficiency high ; tension is not necessary to make chains grip their wheels, as is the case with belts ; the minimum of journal friction, and, therefore, a more economical use of power than any other mechanical means of transmission in the case of " Inverted-Tooth " chains, quietness compared with other forms of tooth gearing.
Whilst most. contingencies in power transmissions can be met by the application of those types of chains already described, extreme cases, where high chain speeds only are possible, and sometimes essential, prohibit the use of these. Careful consideration led the author to introduce a high-speed chain to meet such exacting requirements, and although made at present in one pitch only, it permits of varying widths dependent on the power transmitted. This chain can be run at speeds from 1,400 to 2,200 ft. per minute without detriment, and is practically noiseless at all speeds, by reason of its distinctive tooth action, which, whilst resembling that of the
roller chain, possesses the advantages of the Invertedtooth ' type. The chain will drive on either side, and by reason of its extreme flexibility and elasticity, can he used where crossed drives are required, if the centres are reasonably long, and the smaller widths of chain are used. Tho formation of this chain approximates to that of the " Invertedtooth " type, duplex plates forming a block, held together by a hardened-steel bush which takes its bearings on a hardened rivet. The plates are of a special form, pierced with lightening holes, and the assembled chain is intended to be run on flanged wheels.
Chain drives occupy little space and overcome difficulties of cramped or awkward positions. They give an efficient. service at centre distances too short for belts or too long for gearing ; they are climatically satisfactory, i.e., under hot or damp conditions. They can be used for almost every kind of drive, but several factors determine the best size and type of chain to be used, among which are :—the nature of the drive; whether the load is steady or intermittent; speed required; power to be transmitted.
No hard-and-fast lines can be laid down as to speed for each particular drive. Speed limits which can be recommended for each particular type have already been mentioned, but they can be run at even higher speeds when special provision for lubrication is made.
The undoubted efficiency of chain gearing, as at present manufactured, is mainly due to :—(a) the more thorough understanding of the principles involved, due to constant study of drives under working conditions; (b) the many improvements in the manufacture of chains and wheels, which ensures that precision so essential (e) the more correct designing, prompted by experience, of chains and wheels, and the unproved methods of mounting same. Given even normal conditions, the efficiency of chain drives is relatively high to that of most other forms of transmission. Under favourable circumstances, careful testa have shown that, for the chains only, an efficiency as high as 99 per cent, can be obtained, whilst for the complete drive when well mounted, efficiencies of 96 per cent. and 97 per cent. have been obtained.
While maintained efficiencies of 94 per cent. to 96 per cent. lire the rule for well-designed drives under average conditions, several factors must always be considered to ensure such results, among these being :—(1) speed of chain; (2) ratio between wheels ; (3) position of drive ; (4) efficiency of lubrication ; (5) distance of centres; (6) proportions of the chain and wheel teeth ; (7) continuous or fluctuating load ; (8) size of chain relative to power transmitted ; (9) design of bearing.
Seldom do chains prove too weak for the work required of them, for they will usually wear out by elongation, due to wear between rivet and bush, before breaking ; therefore, selection should be made which postpones such a condition as long as possible. Other conditions being normal, it naturally follows that the life depends on the amount of pressure per square inch of projected rivet area, and the hardness of e-earing surfaces. It is found, in practice, that not more than 650 lb.
pressure to the square inch of such projected area should be allowed. As the wear and the strength of well-proportioned chains have a relation to the rivet diameter, it is customary to select them by their strength, instead of calculating the rivet-bearing surface.
It would be somewhat dangerous to state here definite factors of safety for each particular type of chain by simply taking the breaking load as a basis and its ratio to the pull, for, obviously, the factors must vary, not only with the speed, but with the general conditions prevailing. For instance, with a short drive in a polishing or grinding shop the factor might conceivably be as high as 35 or 40. yet exactly similar chains might be used under ideal conditions for lubrication and tweed, with a factor as low as 8 or even 5. As a general condition it might be fair to state that if the lubrication was as good as is usually provided for the small-end of the connecting rod of an engine, which has similar duties to perform as a chain bearing, equally high pressures per square in. of projected area might be adopted. As in many other matters, automobile chains well above their work are more economical than those having a low safety factor, which accounts for the use of so large a factor in severe cases where the conditions of load are irregular. For such drives the chain manufacturers recommend the use of a shock-absorbing wheel, which has springs between the rim and the hub. These absorb the fluctuations of the load and prevent injury to the chain and wheels. The highest ratios of wheels desirable between the driver and driven are : Inverted-tooth type, 1-6; roller and block type, 1-7i. The maximum and minimum numbers of teeth advisable may be said to be —Inverted-toothtype, 15 and 90; roller type, 8 and 70; block type, 6 and 60. Wheels of reasonably-large diameters are to be preferred for quietness of running, and provision should, when possible, be made for a " hunting " tooth on one of the wheels. The position of drive is of considerable importance—the chains should be run in a vertical plane. that is to say, the two shafts horizontal. If one shaft is higher than the other, the shaft carrying the larger wheel should be uppermost in order to distribute the weight of the chain over the greater number of teeth.
The approximate limit of angularity from a vertical line at which a chain should be run without necessitating the introduction of a jockey pulley is 30 degrees. but will vary slightly with the direction of pull. In the. case of vertical drives. however, in order to reduce the destructive element on both chain and wheels, by keeping the former in proper contact with the lower wheel, it is advisable to provide for a jockey pulley on the slack side. Where possible the centre distance should not be less than one-and-a-half times the diameter of the large wheel, or greater than from 10 ft. to 12 ft. for fairly heavy drives. For elevator and carrier chains, which run on supports, the centre distance may be almost any length. Although chains have a certain amount of lateral flexibility, and give satisfaction where conditions are far from ideal, the
general mounting, or erecting, cannot be too substantial. Shaft bearings should be rigid and wheels lineable. If on light shafts, liable to spring under load, the wheels should be mounted near the bearing. Exact alignment is essential for good results, and when the drive is from an electric motor, the minimum amount of end play is permissible to the armature. En passant, it may not he out of place to say that the alignment in chains is not of such vital importance as with double helical cut gears or worm drive.
Ordinary drives, in engineering factories, running under fair conditions, should be lubricated once a week at least, with a lubricant free from any tendency to thicken. Where the temperature is much above normal a thick oil of considerable body should be used. When a more-fluid oil is used its consistency should be judged by the speed of the drive. For high speeds use a thin oil in order to penetrate the joints, followed up by a thicker oil, which refuses to be thrown off by the centrifugal force. The lubricant is best applied with a brush to the inner side of the chain when stationary. The advantages of providing a suitable cover, preferably of metal, will be obvious, and a drip lubricator should be fitted into the top portion and a tap for draining away the oil when necessary in the lowest part of the guard. It should be noted, from the diagram given above, that for wheels suitable for block and twin-roller chains the top diameters of the chain wheels are equal to the pitch-line diameter, plus the diameter of the end of the block or the roller, while for single-roller chains the top diameter should never exceed the pitch diameter, plus half the pitch of the chain. In the " Inverted-tooth " chain the diameter of the wheel blank is, for all intents and purposes, equal to the pitch line. It is advisable, but not absolutely necessary, to make provision for means of adjustment. It will be apparent that both tight and slack chains are evils to be avoided ; as a matter of fact, only a small amount of slackness should be perceptible when the drive is stationary. Where no adjustment can be provided the chain should be shortened by one pitch as soon as the sag will allow, for which purpose special links are generally obtainable. For wheels running at high speeds and with a small number of teeth, a good quality of mild steel should be used, the teeth being case-hardened. For the larger sizes a good quality of cast iron will usually be found suitable, except where the conditions are unusually severe, when steel castings may be substituted with advantage. To maintain efficiency the continuance of correct tooth form of chain wheels is essential.
(Figs. 2 and 3.) ( To be continued.)