Integration is the name of the game these days in axle and suspensions systems, as Sharon Clancy discovers.
Page 58
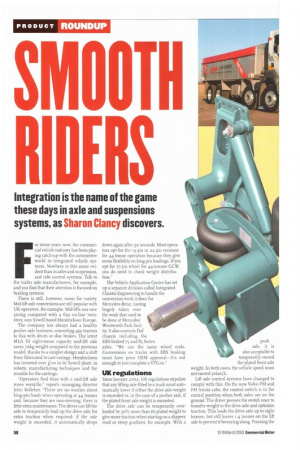
Page 59
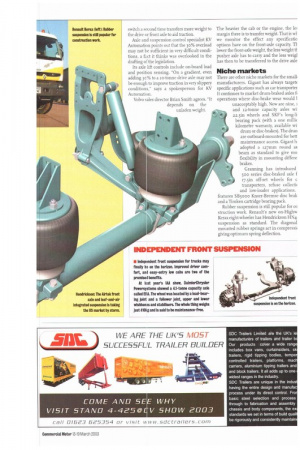
If you've noticed an error in this article please click here to report it so we can fix it.
For some years now, the commercial vehicle industry has been playing catch-up with the automotive world in integrated vehicle systems. Nowhere is this more evident than in axles and suspension, and ride control systems. Talk to the trailer axle manufacturers, for example, and you find that their attention is focused on braking systems.
There is still, however, room for variety. Mid-lift axle conversions are still popular with UK operators, for example. Mid-lifts can save 500kg compared with a 6X2 on-line twinsteer, says Sywell-based Hendrickson Europe.
The company has always had a healthy pusher axle business, converting 4x2 tractors to 6x.2 with drum or disc brakes. The latest MLA III eight-tonne capacity mid-lift axle saves 70kg weight compared to the previous model, thanks to a simpler design and a shift Iron fabricated to cast casings. Hendrickson has invested over Li rn in its Sywell plant, in robotic manufacturing techniques and the moulds for the castings.
"Operators find 6x2s with a mid-lift axle more versatile," reports managing director John Kelleher. "There are no worries about king-pin loads when operating at 44 tonnes and, because they are non-steering, there is little extra maintenance. The driver can lift the axle to temporarily load up the drive axle for extra traction when required: if the axle weight is exceeded, it automatically drops down again after 90 seconds. Most operators opt for the 19.5in or 22.5in versions for 44-tonne operation because they give some flexibility on king-pin loadings. If you opt for 17.5in wheel for 44-tonnes GCW, you do need to check weight distribution."
The Vehicle Application Centre has set up a separate division called Integrated Chassis Engineering to handle the conversion work it does for Mercedes-Benz, having largely taken over the work that used to be done at Mercedes' Wentworth Park facility. It also converts Daf chassis including the
EBS-braked 75 and 85 Series axles. We use the same wheel ends. Conversions on trucks with EBS braking must have prior OEM approval—it's not enough to just complete a VTGio."
UK regulations
Since January 2002, UK regulations stipulate that any lifting axle fitted to a truck must automatically lower if either the drive axle weight is exceeded or, in the case of a pusher axle, if the plated front axle weight is exceeded.
The drive axle can be temporarily overloaded by 30% more than its plated weight to give more traction when starting on a slippery road or steep gradient, for example. With a push axle, it is also acceptable to temporarily exceed the plated front axle weight. In both cases, the vehicle speed must not exceed 3okm/h.
Lift axle control systems have changed to comply with this. On the new Volvo FM and FH trucks cabs, the control switch is in the central position when both axles are on the ground. The driver presses the switch once to transfer weight to the drive axle and optimise traction. This loads the drive axle up to eight tonnes, but still leaves 1.4 tonnes on the lift axle to prevent it bouncing along. Pressing the switch a second time transfers more weight to the drive or front axle to aid traction.
Axle and suspension control specialist KY Automation points out that the 30% overload may not be sufficient in very difficult conditions, a fact it thinks was overlooked in the drafting orthe legislation.
Its axle lift controls include on-board load and position sensing. On a gradient. even adding 3c% to a ro-tonne drive axle may not be enough to improve traction in very slippery conditions," says a spokesperson for KV Automation.
Volvo sales director Brian Smith agrees. "it depends on the unladen weight.
• Indepondent front suspension for trucks may finally ba on the horizon. Improved driver comfort, an 1 easy-entry low cabs are two of the promised benefits, At Ittst year's IAA show, DalmlerChrysler Powersystems showed a 4.1-tonne capacity axle called EF A. The wheel was located by a load-bearing Joint and a follower Joint, upper and lower wishbon Is and stabilisers. The whole thing weighs Just 4101g and Is said to be maintenance-free.
The heavier the cab or the engine, the lei margin there is to transfer weight. That is wl we monitor the effect any specificatio options have on the front-axle capacity. TI lower the front-axle weight, the less weight tk pusher axle has to carry and the less weigl has then to be transferred to the drive axle
Niche markets
There are other niche markets for the small, manufacturers. Gigant has always target( specific applications such as car transporter It continues to market drum-braked axles f operations where disc-brake wear would I unacceptably high. New are nine, and 12-tonne capacity axles wk 22..5in wheels and SKF's long-li bearing pack (with a one mac kilometre warranty, available wi
drum or disc-brakes). The drun are outboard-mounted for bett maintenance access. Gigant h adopted a 12,7mm round as beam as standard to give mo flexibility in mounting differe brakes.
Granning has introduced 500 series disc-braked axle f 17.5in off-set wheels for c transporters, refuse collectic and low-loader applications.
features SB5000 Knorr-Bremse disc brak and a Timken cartridge bearing pack.
Rubber suspension is still popular for co struction work. Renault's new on-Highw Kerax eight-wheeler has Hendrickson HN.,t suspension as standard. The diagonal mounted rubber springs act in compressil giving optimum spring deflection.