AIR'S iE THING
Page 112
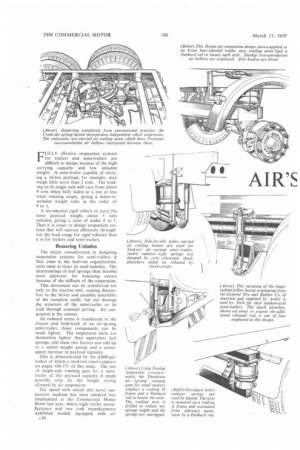
Page 113
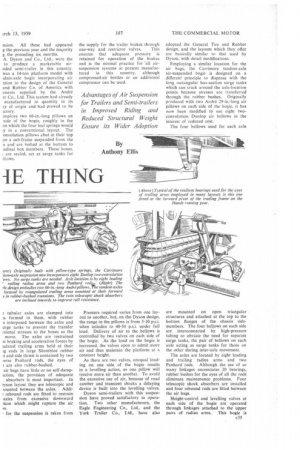
Page 114
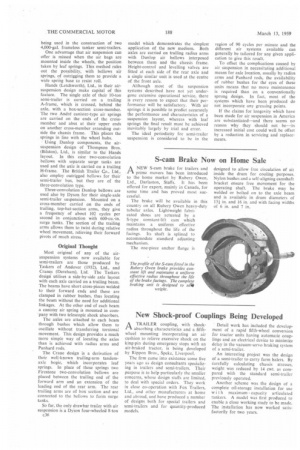
If you've noticed an error in this article please click here to report it so we can fix it.
FULLY effective suspension systems for trailers and semi-trailers are difficult to design because of the high carrying capacity and low unladen weight. A semi-trailer capable. of carrying a 14-ton payload, for example, may weigh little more than 2 tons. The loading on its single axle will vary from about 9 tons when fully laden to a ton or less when running empty, giving a laden-tounladen weight ratio in the order of 9 to 1.
A six-wheeled rigid vehicle to carry the same payload weighs about 5 tons unladen, giving a ratio of under 4 to 1. Thus it is easier to design suspension systems that will operate efficiently throughout the load range for rigid vehicles than it is for trailers and semi-trailers.
Bouncing Unladen
The major consideration in designing suspension systems for semi-trailers is that, even in the best-run organizations, units must at times be used unladen. The shortcomings of leaf springs then become most apparent, for bouncing occurs because of the stiffness of the suspension.
This movement can be transferred not only to the tractive unit, causing discomfort to the driver and possible instability of the complete outfit, but can damage the structure of the semi-trailer or its load through constant jarring. Air suspension is the answer.
As reduced stress is transferred to the chassis and bodywork of an air-sprung semi-trailer, these components can be made lighter. The suspension units are themselves lighter than equivalent leaf springs, and these two factors can add up to a useful weight saving and a consequent increase in payload capacity.
This is demonstrated by the 4,000-gal. tanker of which a road-test report appears on pages 168-171 of this issue. The use of single-axle running gear for a semitrailer of this payload capacity is made possible only by the weight saving allowed by air suspension.
The speed with which this novel suspension medium has been adopted was emphasized at the Commercial Motor Show last year, where eight trailer manufacturers and two tank manufacturers exhibited models equipped with air nsion. Alt these had appeared g the previous year and the majority g the preceding six morths.
A. Dyson and Co., Ltd., were the to produce a marketable airtided semi-trailer in this country. was a 14-ton platform model with idem-axle bogie incorporating air asion to the design of the General and Rubber Co. of America with onents supplied by the Andre er Co., Ltd. This system had already manufactured in quantity in its ry of origin and had proved to be tetory.
:mploys two 66-in.-long pillows on side of the bogie, roughly in the on which the four leaf springs would iy in a conventional layout. The onvolution pillows abut at their top on a sub-frame suspended from the s and are bolted at the bottom to udinal box members. These boxes, L are sealed, act as surge tanks for Wows.
! tubular axles are clamped into formed in them, with rubber s interposed between the axles and urge tanks to prevent the transfer rsional stresses to the boxes as the move. The axles are restrained st braking and acceleration forces by :ulated trailing arms held at their ig ends in large Silentbloc rubber :s and side thrust is contained by two rerse Panhard rods, the eyes of are also rubber-bushed.
air bags have little or no self-damptetion, the provision of adequate absorbers is most important. In lyson layout they are telescopic and lounted between the axles. Addii rebound rods are fitted to restrain axles from excessive downward ;tion which might rupture the air. vs.
• for the suspension is taken from
the supply for the trailer brakes through one-way and restrictor valves. This ensures that adequate pressure is retained for operation of the brakes and is the normal practice for 'all airsuspension systems at present manufactured in this country, although compressed-air bottles or an additional compressor can be used.
Pressure required varies from one layout to another, but, on the Dyson design, the range in the pillows is from 5-10 psi. when unladen to 40-50 p.s.i. under full load. Delivery of air to the bellows is controlled by two valves on each side of the bogie. As the load on the bogie is increased, the valves open to admit more air and thus maintain the platform at a constant height.
As there are two valves, unequal loading on one side of the bogie results in a levelling action, as one pillow will receive more air than another. To avoid the excessive use of air, because of road camber and transient shocks a delaying device is built into the levelling valves.
Dyson semi-trailers with this suspension have proved satisfactory in operation. Two other manufacturers, the Eagle Engineering Co., Ltd., and the York Trailer Co., Ltd., have also
adopted the General Tire and Rubber design, and the layouts which they offer are basically similar to that used by Dyson, with detail modifications.
Employing a similar location for the air bags, the Carrimore tandem-axle air-suspended bogie is designed on a different principle to dispense with the long rectangular box-section surge tanks which can crack around the axle-location points because stresses are transferred through the rubber bushes. Originally produced with two Andre 29-in.-long air pillows on each side of the bogie, it has now been modified to use eight twoconvolution Dunlop air bellows in the interest of reduced cost.
The four bellows used for each axle are mounted on open triangular structures and attached at the top to the bottom flanges of the chassis sidemembers. The four bellows on each side are interconnected by high-pressure tubing to obviate the need for separate surge tanks, the pair of bellows on each axle acting as surge tanks for those on the other during inter-axle movement.
The axles are located by eight leading and trailing radius arms and two Panhard rods. Although the use of so many linkages necessitates 20 bearings, rubber bushes for the eyes of all the rods eliminate maintenance problems. Four telescopic shock absorbers are installed and four rebound rods are fitted between the air bags.
Height-control and levelling valves at each side of the bogie are operated through linkages attached to the upper pairs of radius arms. This bogie is
being used in the construction of two 4,000-gal. frameless tanker semi-trailers.
One advantage that air suspension can offer is missed when the air bags are mounted inside the wheels, the position taken by leaf springs. This method rules out the possibility, with bellows air springs, of outrigging them to provide a wide spring base to resist roll.
Hands (Letchworth), Ltd., in their airsuspension design make capital of this feature. The single axle of their 10-ton semi-trailer is carried on a trailing A-frame, which is crossed, behind the axle, with a box-section cross-member. The two Andre canister-type air springs are carried on the ends of the crossmember and abut at their upper ends on another cross-member extending outside the chassis frame. This places the springs in line with the wheel hubs.
Using Dunlop components, the airsuspension design of Thompson Bros. (Bilston), Ltd., is similar to the Hands layout. In this 6se two-convolution bellows with separate surge tanks are used and the axle is carried on a trailing H-frame. The British Trailer Co., Ltd„ also employ outrigged bellows for their semi-trailer bus, but they are of the three-convolution type.
Three-convolution Dunlop bellows are used also by Dyson for their single-axle semi-trailer suspension. Mounted on a cross-member carried on the ends of trailing, top-hat-section arms, they give a frequency of about 102 cycles per second in conjunction with 600-cu.-in. surge tanks. The section of the trailing arms allows them to twist during relative wheel movement, relieving their forward pivots of much stress.
Original Thought
Most original of any of the airsuspension systems now available for semi-trailers are those produced by Taskers of Andover (1932), Ltd., and Cranes (Dereham), Ltd. The Taskers design utilises a side-by-side axle layout with each axle carried on a trailing beam. The beams have short cross-pieces welded to their forward ends and these are clamped in rubber bushes, thus locating the beam without the need for additional linkages. At the other end of each beam a canister air spring is mounted in company with two telescopic shock absorbers.
The axles arc attached to each beam through bushes which allow them to oscillate without transferring torsional movement. This design provides a much more simple way of locating the axles than is achieved with radius arms and Panhard rods.
The Crane design is a derivation of their well-known trailing-arm tandemaxle bogie, which incorporates leaf springs. In place of these springs two Firestone two-convolution bellows are placed between the trailing end of the forward arm and an extension of the leading end of the rear arm. The rear trailing arms are of box section and are connected to the bellows to form surge tanks.
So far, the only drawbar trailer with air suspension is a Dyson four-wheeled 8-ton c36 model which demonstrates the simplest application of the new medium. Both axles are carried on trailing radius arms with Dunlop air bellows interposed between them and the chassis frame. Height-control and levelling valves are fitted at each side of the rear axle and a single similar unit is used at the centre of the front axle.
Although most of the suspension systems described have not yet undergone extensive operational service, there is every reason to expect that their performance will be satisfactory. With air springs it is possible to predict accurately the performance and characteristics of a suspension layout, whereas with leaf springs the final result must be achieved inevitably largely by trial and error.
The ideal periodicity for semi-trailer suspension is considered to be in the region of 90 cycles per minute and the different air systems available can generally be tailored for any given application to give this result.
To offset the complications caused by air suspension in necessitating additional means for axle location, usually by radius arms and Panhard rods, the availability of rubber bushes for the eyes of these units means that no more maintenance is required than on a conventionally sprung design. In fact, most of the systems which have been produced do not incorporate any greasing points.
If the claims for longevity which have been made for air suspension in America are substantiated—and there seems no reason why they should not be—its increased initial cost could well, be offset by a reduction in servicing and replacements.