Safe filling and safe stopping
Page 52
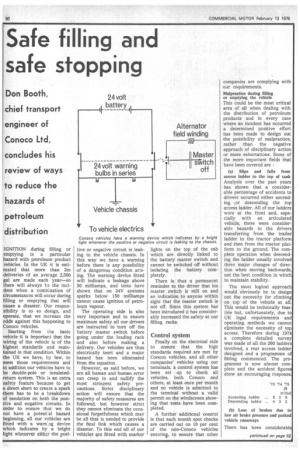
Page 55
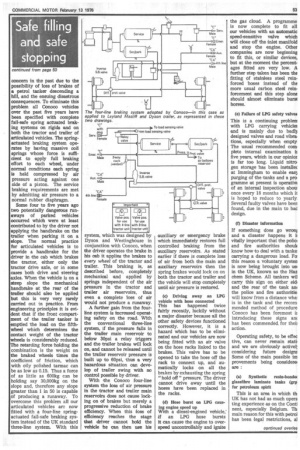
Page 56
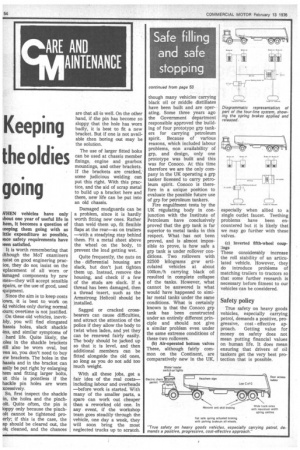
If you've noticed an error in this article please click here to report it so we can fix it.
Don Booth, ,chief transport engineer of Conoco Ltd, concludes his review of ways to reduce the hazards of petroleum distribution
IGNITION during filling or emptying is a particular 'hazard with petroleum product vehicles. In the UK it is estimated that more than 2m deliveries of an average 2,500 gal are made each year—so there will always be the incident when a comb:nation of circumstances will occur during filling or emptying that will cause a disaster. Our responsibility is to so design, and operate, that we increase the odds against this happening to Conoco vehicles.
Starting from the basic vehicle it is important that the wiring of the vehicle is of the highest standards and. maintained in that condition. Within the UK we have, by law, to meet those requirements and in addition our vehicles have to be double-pole or insulatedreturn system. This is an extra safety feature because to get a direct short to create a 'spark there has to be a breakdown of insulation on both the positive and 'negative circuits. In order to ensure that we do not have a potential hazard beginning, an our vehicles are fitted with a warriThig device which indicates by a bright light whenever either the posi tive or negative circuit is leaking to the vehicle chassis. In this way we have a warning before there is any possibility of a dangerous condition arising. The warning device fitted will indicate a leakage above 50 milliamps, and tests have shown that on 24V systems sparks below 150 minim-rips cannot cause ignition of petroleum vapour.
The operating side is also very important and to ensure maximum safety all our drivers are instructed to 'turn off the battery master switch before going under the loading rack and also before making a delivery. Our vehicles are thus electrically inert and a major hazard has been eliminated from the equation.
However, as said before, we are all human and human error can creep in and nullify the most stringent safety precautions. Strict disciplinary action will ensure that the majority of safety measures are followed, but 'however strict they cannot eliminate the occasional forgetfulness which may be all that is needed to provide the final link which causes a disaster. To this end all of our vehicles are fitted with marker lights on the top of the cab which are directly linked to the battery master switch and cannot be switched off without isolating the battery completely.
There is thus a permanent reminder to the driver that his master switch is still on and an indication to anyone within sight that the master switch is not off. Since this system has been introduced it has considerably increased the safety at our filling racks.
Control system
Finally on the electrical side to ensure that the high standards required are met by Conoco vehicles, and all other companies' vehicles using our terminals, a control system has been set up to check all vehicles, both Conoco and others, at least once per month and no vehicle is admitted to the terminal without a valid permit on the windscreen showing that tests have been completed.
A further additional control is that each month spot checks are carried out on 10 per cent of the non-Conoco vehicles entering, to ensure that other companies are complying with our requirements.
Malpractice during filling or emptying the vehicle This could be the most critical area of all when dealing with the distribution of petroleum products •and in every case where an incident has occurred a determined positive effort has been made to design out the possibility of malpractice, rather than the negative approach of disciplinary action or more exhortations. Some of the more important fields that have been covered are : (a) Slips and falls from access ladder to the top of tank Analysis over the past years has shown that a considerable percentage of accidents to drivers occurred either ascending Nor descending the top access ladder. All of our ladders were at the front and, especially with an articulated vehicle, there were considerable hazards to the drivers transferring from the trailer ladder to the tractor platform and then from the tractor platform to the ground. The complete operation when descending the ladder usually involved three major changes •of direction when moving backwards, not the best condition in which to maintain stability.
The most logical approach would obviously be to design out the necessity for climbing on top of the vehicle at all. This would be technically feasible but, unfortunately, due to UK legal requirements and operating methods we cannot eliminate the necessity of top access. Therefore during 1974 a complete detailed survey was made of all the 260 ladders involved, a rear access ladder designed and a programme of' fitting commenced. The programme is now almost complete and the accident figured show an encouraging response
(b) Loss of brakes due to low air brake pressure and parked vehicle runaways
There has been considerable concern in the past due to the possibility of loss of brakes of a petrol tanker descending a hill, and the ensuing disastrous consequences. To eliminate this problem all Conoco vehicles over the past five years have been specified with complete fail-safe spring actuated braking systems on rigids and on both the tractor and trailer of articulated vehicles. The springactuated braking system operates by having massive coil springs whose force is sufficient to apply full braking effort to each wheel, under normal conditions each -spring Is held compressed by air pressure acting against one side of a piston. The service braking requirements are met by admitting air pressure to a normal rubber diaphragm..
Some four to five years ago two potentially dangerous runaways of parked vehicles occurred Which were at least contributed to by the driver not applying the handbrake on the trailer when parking it on a slope. The normal practice for articulated vehicles is to provide a handbrake for the driver in the cab which brakes the tractor, either only the tractor drive axle, or in some cases both drive and steering axles. When the vehicle is on a steep slope the mechanical handbrake at the rear of the trailer should also be applied but this is very very rarely carried out in practice. From engineering principles it is evident that if the front compartment of the trailer tanker is emptied the load on the fifthWheel which determines the contact weight of the tractor wheels 'is considerably reduced. The retarding force holding the combination is the weight on the braked wheels times the coefficient of friction, which with oily polished tarmac can he as low as 0.15. Thus a force of as little as 600kg can be holding say 30,000kg on the slope and, therefore any slope greater than 1 in 50 is capable of producing a runaway. To 'overcome this problem all our articulated vehicles arc now fitted with a four-line springactuated fail-safe braking system instead of the UK standard three-line system. With this system, which was designed by Dyson and Westinghouse in conjunction with Conoco, when the driver operates the brake in his cab it 'applies the brakes to every wheel of the tractor and trailer. This braking is, as described before, completely mechanical and applied by springs independent of the air pressure in the tractor and trailer air reservoirs, thus even a complete 'loss of air would not produce a runaway.
A further gain from the fourline system is increased operating safety on the road. With the conventional three-line system, if the pressure falls in the trailer main reservoir to below 30psi a relay triggers and the trailer brakes will lock on, and cannot be released until the trailer reservoir pressure is built up to 60psi, thus a very hazardous situation can develop of trailer swing with no control possible by driver.
With the Conoco four-line system the loss of air pressure in the tractor and trailer main reservoirs does not cause locking on of brakes but merely a progressive reduction of brake efficiency. When this (loss of efficiency reaches the stage that driver cannot hold the vehicle he can then use his auxiliary or emergency brake which immediately restores full controlled braking from the auxiliary reservoirs. As stated earlier if there is complete loss of air from both the main and auxiliary reservoirs then the spring brakes would lock on on both the tractor and trailer and the vehicle will stop completely until air pressure is restored.
(c) Driving away an LPG vehicle with hose connected This has 'happened twice fairly recently, luckily without a major disaster because all the other safety devices functioned correctly. However, it is a hazard which has to he eliminated and our vehicles are now being fitted with an air valve an the hose racks linked to the brakes. This valve has to be opened to take the hose off the rack to connect up, and aumatically locks on all the brakes by exhausting the spring "hold off" pressure. The driver cannot drive away until the hoses have been replaced in the racks.
(d) Hose burst on LPG causing engine speed up
With a diesel-engined if an LPG hose bursts It can cause the engine to overspeed uncontrollably and ignite the gas cloud. A programme is now complete to fit all our vehicles with an automatic speed-sensitive valve which will close off the inlet manifold and stop the engine. Other companies are now beginning to fit this, or similar devices, but at the moment the percentages fitted are very low. A further step taken has been the fitting of stainless steel reinforced hoses instead of the more usual carbon steel reinforcement and this step alone should almost eliminate burs4 horses.
(e) Failure of LPG safety valves This is a continuing problem with LPG carrying vehicles and is mainly due to badly designed valves and road vibra• ticms, especially when empty. The usual recommended corn. Mete internal examination is five years, Which in our opinior is far too long. Liquid nitro gen storage has been installee at Immingham to enable eas3 purging of the tanks and a pro. gramme art present is operatiV4 of an internal inspection 'abaui once every 18 months which it is hoped to reduce to yearly, Several faulty valves have beer found, due in the main to bad design.
(f) Disaster information If something does go wrorn and a disaster happens it b vitally important that the polio and fire authorities -shout( know how to deal with a tanke carrying a dangerous load. Fa this reason a voluntary systen is now being brought into usi in the UK, known as the Haz them Scheme. All tankers wil carry this sign on either sic1.1 and the rear of the tank an the police and fire authoritie will know from a distance whai is in the tank and the recom. mended method of procedure Conoco has been foremost it introducing these signs am has been commended, for theh action.
Operating safety, to be effec tive, can never remain stati and we 'are obviously active]; considering future designs Some of the main possible im provements being considerei
are : (a) Synthetic resin-bondei glassfibre laminate tanks (grill; for petroleum spirit
This is an area in which th UK 'has not had as much opera ting experience as on the Conti rent, especially Belgium. Th main reason for this with petrol has been legal restrictions, al though many vehicles carrying black oil or middle distillates have been built and are operating. Some three years ago the Government department responsible approved the building of four prototype grp tankers for carrying petroleum spirit. Because of various reasons, which included labour problems, non availability of grp, and design, only one prototype was built and this was for Conoco. At this time therefore we are the only company in the UK operating a grp tanker licensed to carry petroleum spirit. Conoco is therefore in a unique position to evaluate the possible future use of grp for petroleum tankers.
Fire engulfment tests by the UK regulating body in conjunction with the Institute of Petroleum have conclusively proved that the grp tank is far superior to metal tanks in this respect. What has not been proved, and is almost impossible to prove, is how safe a grp tank is under rollover conditions. Two rollovers with 32500 kilograms gvw articulated vehicles at about 100km/h carrying black oil resulted in complete collapse of the tanks. However, what cannot be 'answered is what would have happened to similar metal tanks under the same conditions. What is certainly known is that the Conoco grp tank has been constructed under an entirely different principle and should not give a similar problem even under the same extreme conditions of these two rollovers.
(b) Air-operated bottom valves These, although fairly common on the Continent, are comparatively new in the UK, especially when allied to a single outlet faucet. Teething problems have been encountered but it is likely that we may go further with these valves.
(c) Inverted fifth-wheel coupIngs These considerably increase the roll stability of an articulated vehicle. However, they do introduce problems of matching trailers to tractors so that some further research is necessary before fitment to our vehicles can be considered.
Safety policy
True safety on heavy goods vehicles, especially carrying petrol, demands a positive, progressive, cost effective approach. Getting value for money on safety does not mean putting financial values on human life. It does mean ensuring that drivers of oil tankers get the very best protection that is possible.