New roll bars could trim off the pounds
Page 25
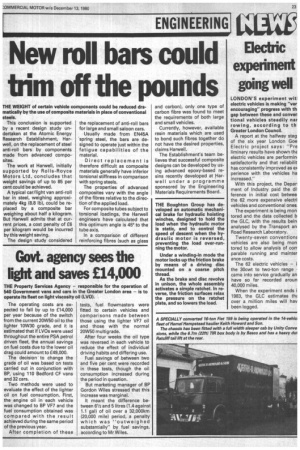
If you've noticed an error in this article please click here to report it so we can fix it.
THE WEIGHT of certain vehicle components could be reduced dramatically by the use of composite materials in place of conventional steels.
This conclusion is supported by a recent design study undertaken at the Atomic Energy Research Establishment, Harwell, on the replacement of steel anti-roll bars by components made from advanced composites.
The work at Harwell, initially supported by Rolls-Royce Motors Ltd, concludes that weight savings of up to 85 per cent could be achieved.
A typical car/light van anti-roll bar in steel, weighing approximately 4kg (8.8 lb), could be replaced by a composite bar weighing about half a kilogram. But Harwell admits that at current prices, a cost penalty of £6 per kilogram would be incurred by this weight saving.
The design study considered the replacement of anti-roll bars for large and small saloon cars.
Usually made from EN45A 'spring steel, the bars are designed to operate just within the fatigue capabilities of th e material.
Direct replacement is therefore difficult as composite materials generally have inferior torsional stiffness in comparison with spring steels.
The properties of advanced composites vary with the angle of the fibres relative to the direction of the applied load.
For composite tubes subject to torsional loadings, the Harwell engineers have calculated that this optimum angle is 45° to the tube axis.
In a comparison of different reinforcing fibres (such as glass and carbon), only one type of carbon fibre was found to meet the requirements of both large and small vehicles.
Currently, however, available resin materials which are used to bond such fibres together do not have the desired properties, claims Harwell.
The Establishment's team believes that successful composite designs can be developed by using advanced epoxy-based resins recently developed at Herwell under a programme sponsored by the Engineering Materials Requirements Board.