BRAKING THE LA\4 COULD BE COSTLY
Page 43
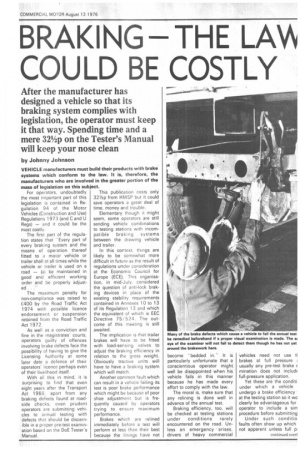
Page 44
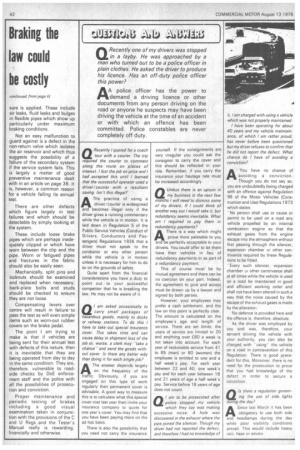
If you've noticed an error in this article please click here to report it so we can fix it.
After the manufacturer has designed a vehicle so that its braking system complies with legislation, the operator must keep it that way. Spending time and a mere 321/2p on the Tester's Manual will keep your nose clean
by Johnny Johnson
VEHICLE manufacturers must build their products with brake systems which conform to the law. It is, therefore, the manufacturers who are involved in the greater portion of the mass of legislation on this subject.
For operators, undoubtedly the most important part of this legislation is contained in Regulation 94 of the Motor Vehicles (Construction and Use) Regulations 1973 (and C and U Regs) — and it could be the most costly.
The first part of the regulation states that "Every part of every braking system and the means of operation thereof fitted to a motor vehicle or trailer shall at all times while the vehicle or trailer is used on a road — (a) be maintained in good and efficient working order and be properly adjusted . . ."
The maximum penalty for non-compliance was raised to E400 by the Road Traffic Act 1974 with possible licence endorsement or suspension retained from the Road Traffic Act 1972.
As well as a conviction and fine in the magistrates' courts, operators guilty of offences involving brake defects face the possibility of having to give the Licensing Authority at some later date a defence of their operators licence perhaps even of their livelihood itself.
With all this in mind, it is surprising to find that even eight years after the Transport Act 1968, apart from any braking defects found at roadside checks, even prudent operators are submitting vehicles to annual testing with defects that should be discernible in a proper pre-test examination based on the DoE Tester's Manual. This publication costs only 321/2p from HMSP but it could save operators a great deal of time, money and trouble.
Elementary though it might seem, some operators are still sending vehicle combinations to testing stations with incompatible braking systems between the drawing vehicle and trailer.
In this context, things are likely to be somewhat more difficult in future as the result of regulations under consideration at the Economic Council for Europe (ECE). This organisation, in mid-July, considered the question of anti-lock braking devices in place of the existing stability requirements contained in Annexes 10 to 13 of its Regulation 13 and which the equivalent of which is EEC Directive 75/524. The outcome of this meeting is still awaited.
The implication is that trailer brakes will have to be fitted with load-sensing valves to adjust the braking efficiency in relation to the gross weight. Obviously tractive units will have to have a braking system which will match.
Another common fault which can result in a vehicle failing its test is poor brake performance which might be because of poor shoe adjustment but is frequently caused by operators trying to ensure maximum performance.
Brakes which are relined immediately before a test will perform at less than their best because th.e linings have not become "bedded in.'. It is particularly unfortunate that a conscientious operator might: well be disappointed when his vehicle fails in this manner because he has made every effort to comply with the law.
The moral is, make sure that any relining is done well in advance of the annual test.
Braking efficiency, too, will be checked at testing stations under conditions rarely encountered on the road. Unless an emergency arises, drivers of heavy commercial
vehicles need not use tl brakes at full pressure ; usually any pre-test brake E mination does not includ( full-pressure application.
Yet these are the conditi under which a vehicle undergo a brake efficiency at the testing station so it we clearly be advantageous for operator to include a sim procedure before submitting
Under such conditio faults often show up which not apparent unless full pi
sure is applied. These include air leaks, fluid leaks and bulges in flexible pipes which show up particularly under maximum braking conditions.
Not an easy malfunction to guard against is a defect in the non-return valve which isolates the air reservoir and which thus suggests the possibility of a failure of the secondary system if the service system fails. This is largely a matter of good preventive maintenance dealt with in an article on page 36. It is, however, a common reason for a vehicle failing its annual test.
There are other defects which figure largely in test failures and which should be detectable by simply looking at the system.
These. include loose brake pipes which are perhaps inadequately clipped or which have worn between the clip and the pipe. Worn or fatigued pipes and fractures in the fabric should also be easily seen.
Mechanically, split pins and locknuts should be examined and replaced when necessary, back-plate bolts and studs should be checked to ensure they are not loose.
Compensating levers over centre will result in failure to pass the test as will even simple items such as worn-out rubber covers on the brake pedal.
The point I am trying to make is that if vehicles are being sent for their annual test with defects of this nature, then it is inevitable that they are being operated from day to day in the same condition. They are, therefore, vulnerable to roadside checks by DoE enforcement staff and the police with all the possibilities of prosecution and conviction.
Proper maintenance and periodic testing of brakes including a good visual examination taken in conjunction with the provisions of the C and U Regs .and the Tester's Manual really is rewarding, financially and otherwise.