Enhancing the Value of
Page 32
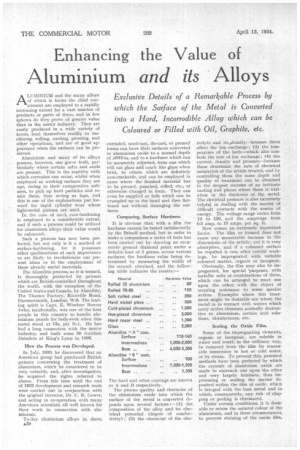
Page 33
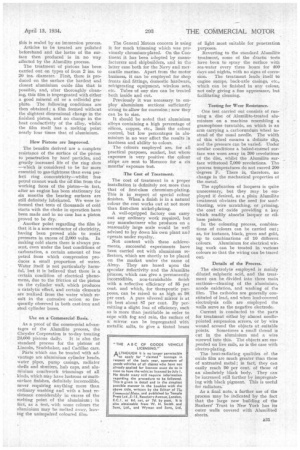
If you've noticed an error in this article please click here to report it so we can fix it.
Aluminium and its Alloys
Exclusive Details of a Remarkable Process by which the Surface of the Metal is Converted into a Hard, Incorrodible Alloy which can be Coloured or Filled with Oil, Graphite, etc.
ALUMINIUM and the many alloys of which it forms the chief constituent are employed to a rapidly increasing extent for a vast number of products or parts of these, and in few spheres do they prove of greater value than in the motor industry. They are easily produced in a wide variety of forms, -lend themselves readily to machining, rolling, casting, pressing, and other operations, and are of good appearance when the surfaces can be preserved.
Aluminium and many of its alloys possess, however, one grave fault, particularly where certain salts and acids are present. This is the rapidity with which corrosion can occur, whilst when employed as working surfaces they are apt, owing to their comparative softness, to pick up hard particles and retain these, thus acting as laps, and this is one of the explanations put forward for rapid cylinder wear where light-metal pistons are used.
In the case of steel, case-hardening is employed to a considerable extent, and if such a process could be utilized for aluminium alloys their value would be enhanced.
Such a process has now been perfected, but not only is it a method of surface-hardening, for it possesses other qualifications of such importance as are likely to revolutionize our present ideas as to the employment of these already useful materials.
The Alumilite process, as it is termed, is thoroughly protected by patents which are British-controlled throughout the world, with the exception of the United States and Canada, by Alumilite, The Thames Factory, Rainville Road., Hammersmith, London, W.6. The leading spirit is Capt. E. Windsor Bowen (who, incidentally, was one of the first people in this country to handle aluminium panels for bodywork when this metal stood at 15s. per lb.). He has had a long connection with the motor industry, and built some 50 Gottlieb Daimlers at King's Lynn in 1896.
How the Process was Developed.
In July, 1930, he discovered that an American group had purchased British patents concerning the treatment of aluminium, which he considered to he very valuable, and, after investigation, he acquired the rights referred to above. From this time until the end of 1932 development and research work were carried out in conjunction with the qriginal inventor, Dr. C. R. Gower, and acting in co-operation with many American scientists, all well known for their work in connection with aluminium.
To-day aluminium alloys in sheet, A30 extruded, sand-cast, die-cast, or pressed forms can have their surfaces converted in aluminium oxide to a normal depth of .0015-in. and to a hardness which can be accurately adjusted, from one which will cut glass and crack like glass when bent, to others which are definitely non-crackalele, and can be employed in cases where the ,finished material has to be pressed, punched, rolled, etc., or otherwise changed in form. They can even be supplied as foils which can be crumpled up in the hand and then flattened out without damaging the surfaces.
Comparing Surface Hardness.
It is obvious that with a film the hardness cannot be 'tested satisfactorily by the Brinell method, but in order to make a comparison a series of tests has been carried out by drawing an accurately ground diamond point under a definite load of.3 grams. across various surfaces, the hardness value being determined by measuring the width of the scratch obtained, and the following table indicates the results:—
The hard and other coatings are known as A and 13 respectively.
The precise quality and character of the aluminium oxide into which the surface of the metal is converted depends upon several factors :—(1) the composition of the alloy and its electrical potential (degree of conductivity) ; (2) the character of the elec
trolyte and its odensity—because these affect the ion exchange ; (3) the temperature of the bath—which also controls the rate of ion exchange ; (4) the current, density and pressure—because these determine the sate of electrical saturation of the article treated, and by controlling them the same depth and quality of treatment can be obtained in the deepest recesses of an intricate casting and places where there is variation in the thickness of the metal. The electrical pressure is also extremely helpful in dealing with the matter of difficult contacts with the source of energy. The voltage range varies from 12 to 129, and the amperage from 0.5 amp. to 15 amps. per sq. ft.
Now comes an extremely important factor. The film so formed does not cause any measurable increase in the dimensions of the article ; yet it is very absorptive, and if a coloured surface be required it can, after 'careful washings, be impregnated with suitable coloured matter, organic or inorganic.
Obviously, the film may also be impregnated, for special 'purposes, with metallic salts or combinations of these, which can be arranged to react one upon the other, with the object of securing resistance to some specific action. Examples where this treatment might be desirable are where the metal is in contact with waters which carry active elements normally destructive to aluminium, certain acid solutions, disinfectants, etc.
Sealing the Oxide Film.
Some of the impregnating elements, organic or inorganic, are soluble in water and could, in the ordinary way, he removed from the film by reasonable immersion in hot or cold water, or by steam. To prevent this, patented methods have been perfected by which the crystals of aluminium oxide are made to encroach one upon the other and very largely laminate, thus imprisoning or sealing the matter deposited within the film of oxide, which is integral with the base metal and in which, consequently, any risk of chipping or peeling is eliminated.
Under certain conditions, it is desirable to retain the natural colour of the aluminium, and in these circumstances, to prevent staining of the oxide film. this is sealed by an immersion process.
Articles to be treated are polished beforehand and the lustre of the surface then produced is in no way affected by the Alumilite process.
The treatment of pistons has been carried out on types of from 2 ins. to 20 ins. diameter. First, there is produced on the surface the hardest and closest aluminium oxide film that is possible, and, after thoroughly cleaning, this film is impregnated with either a good mineral oil or a colloidal graphite. The following conditions are then obtained; a film formed without the slightest dimensional change in the finished piston, and no change in the heat conductivity of the alloy, whilst the film itself has a melting point nearly lour times that of aluminium.
How Pistons are Improved.
The benefits derived are a complete resistance of the surface of the piston to penetration by hard particles, and greatly increased life of the ring slots —which is considered to be far more essential to gas-tightness than even perfect ring concentricity—whilst free petrol cannot wash the oil film from the working faces of the piston—in fact, after an engine has been stationary for six months the bearing surfaces are still definitely lubricated. We were informed that tests of thousands of cold starts with the choke in operation have been made and in no case has a piston proved to be dry.
Another point regarding the film is that it is a non-conductor of electricity, having been proved able to resist pressures in excess of 2,000 volts. In making cold starts there is always present, even under the best conditions of carburation, a certain amount of free petrol from which compression produces a small proportion of water. Water itself is not particularly harmful, but it is believed that there is a certain condition of electrical phenomena, due to the friction of the piston on the cylinder wall, which produces a catalytic effect, and certain elements are realized from the water which resuit in the corrosive action so frequently observed in both cast-iron and steel cylinder bores.
Use on a Commercial Basis. .
As a proof of the commercial advantages of the Alumilite process, the Chrysler Corporation is to-day treating 24;000 pistons daily. It is also the standard process for the pistons of Lincoln, Studebaker, and Cadillac cars.
Parts which can he treated with advantage are aluminium cylinder heads, water pipes, pump casings, radiator shells and shutters, hub caps, and aluminium coachwork trimmings of all kinds, which may have lustrous or mattsurface finishes, definitely incorrodible, never requiring anything more than ordinary washing and with a heat resistance considerably in excess of the melting point of the aluminium ; in fact, as a test, with some colours the aluminium may be melted away, leaving the unimpaired coloured film. The General Motors concern is using it for much trimming which was previously chromium-plated. On the Continent it has been adopted by manufacturers and shipbuilders, and in the latter case both for the Navy and mercantile marine. Apart from the motor business, it can be employed for shop fronts a-nd fittings, domestic hardware, refrigerating equipment, wireless sets, etc. Tubes of any size can be treated both inside and out.
Previously it was necessary to employ aluminium sections sufficiently strong to allow for Corrosion; now they can be to size.
It should be noted that aluminium alloys containing a high percentage of silicon, copper, etc., limit the colour control, but low percentages in aluminium in no way affect the results in hardness and ability to colour.
The colours employed are, for all practical purposes, sunfast, but where exposure is very positive the colour strips are sent to Morocco for a six months' exposure test.
The Cost of Treatment.
The cost of treatment in a proper installation is definitely not more than that of first-class chromium-plating. This is in .respect of special colour finishes. When a finish is in a natural colour the cost works out at not more than first-class nickel-plating.
A well-equipped factory can carry Out any ordinary work required, but any manufacturer who produces on a reasonably large scale would be well advised to lay down his own plant and operate under royalty.
Not content with these achievements, successful experiments have been carried out with aluminium reflectors, which are shortly to be placed on the market under the name of Alray. They are based upon the specular reflectivity and the Alumilite process, which can give a permanently incorrodible, non-tarnishable finish with a reflective efficiency of Si per cent. and which, for therapeutic purposes, can be raised to as high as 98 per cent. A pure silvered mirror is at its best about 87 per cent. By permitting a slight loss of efficiency, such as is more than justifiable in order to cope with fog and rain, the surface of a mirror can he impregnated with metallic salts, to give a tinted beam
of light most suitable for penetration purposes.
Reverting to the standard Alumilite treatment, some of the drastic tests have been to spray the surface with sea-water every three hours for 400 days and nights, with no signs of corro
sion. The treatment lends itself to engine sumps, back-axle casings, etc., which can be finished in any colour, not only giving a fine appearance, but facilitating cleaning.
Testing for Wear Resistance.
One test carried out consists of running a disc of Alumilite-treated aluminium on a machine resembling a gramophone turntable, on which is an arm carrying a carborundum wheel instead of the usual needle. The width of this wheel ensures a definite slip, and the pressure can be varied. Under similar conditions a baked-enamel surface was worn away in 300 revolutions of the disc, whilst the Alumilite surface withstood 7,000 revolutions. Ths process temperatures do not exceed 200 'degrees F. There is, therefore, no change in the mechanical properties of the, metal.
The application of lacquers is quite unnecessary, but they may be employed if desired, as a plain Alumilitt treatment obviates the need for sandblasting, wire scratching, or priming, the coat of oxide providing a key which readily absorbs lacquer or oilbase paints.
In the colouring process, combinations of colours can be carried out ; as, for instance, black, green and gold, up to combinations of 10 different colours. Aluminium for electrical wiring work can be treated in various colours so that the wiring can be traced out.
Details of the Process.
The electrolyte employed is mainly diluted sulphuric acid, and the treatment can be divided into three main sections—cleaning of the aluminium, anode oxidation, and washing of the film. The cathodes are generally constituted of lead, and when lead-covered electrolysis cells are employed the walls serve as the negative electrode.
Current is conducted to the parts for treatment either by almost needlepointed suspension screws, or by wire wound around the objects at .suitable points. Sometimes a small thread is cut in the aluminium and a wire screwed into this. The objects are suspended on live rails, as is the case with electro-pIating.
The heat-radiating qualities of the oxide film are much greater than those of untreated metal ; in fact, they can easily reach 90 per cent. of those of an absolutely black body. They can be increased still farther by impregnating with black pigment. This is useful for radiators.
As a final note, a further use of the process may be indicated by the fact that the large new building of the Bankers' Trust in New York has its outer walls covered with Alumilited sheets.