LOW LOADER LOW BO
Page 100
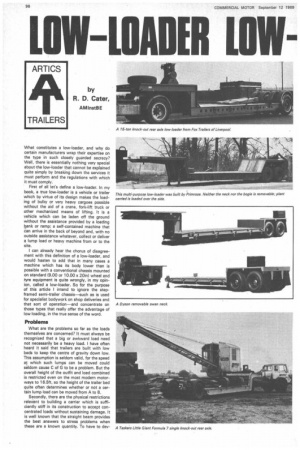
Page 101
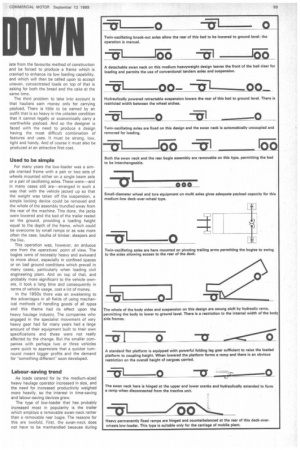
Page 102
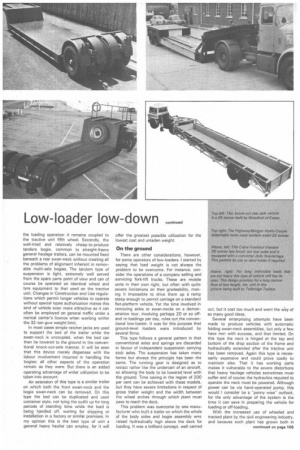
Page 107
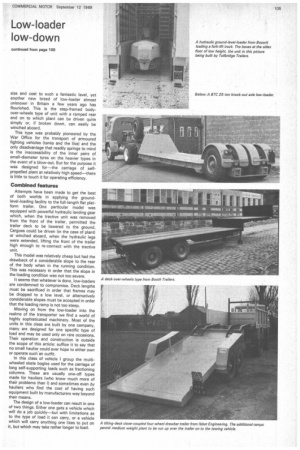
If you've noticed an error in this article please click here to report it so we can fix it.
by R. D. Cater,
AMInstBE What constitutes a low-loader, and why do certain manufacturers wrap their expertise on the type in such closely guarded secrecy? Well, there is essentially nothing very special about the low-loader that cannot be explained quite simply by breaking down the services it must perform and the regulations with which it must comply.
First of all let's define a low-loader. In my book, a true low-loader is a vehicle or trailer which by virtue of its design makes the loading of bulky or very heavy cargoes possible without the aid of a crane, fork-lift truck or other mechanized means of lifting. It is a vehicle which can be laden off the ground without the assistance provided by a loading bank or ramp; a self-contained machine that can arrive in the back of beyond and, with no outside assistance whatever, collect or deliver a lump load or heavy machine from or to the site.
I can already hear the chorus of disagreement with this definition of a low-loader, and would hasten to add that in many cases a machine which has its body lower than is possible with a conventional chassis mounted on standard (9.00 or 10.00 x 20in) wheel and tyre equipment is quite wrongly, in my opinion, called a low-loader. So for the purpose of this article I intend to ignore the stepframed semi-trailer chassis—such as is used for specialist bodywork on shop deliveries and that sort of operation—and concentrate on those types that really offer the advantage of low loading, in the true sense of the word.
Problems
What are the problems so far as the loads themselves are concerned? It must always be recognized that a big or awkward load need not necessarily be a heavy load. I have often heard it said that trailers are built with low beds to keep the centre of gravity down low. This assumption is seldom valid, for the speed at which such lumps can be moved could seldom cause C of G to be a problem. But the overall height of the outfit and load combined is restricted even on the most modern motorways to 16.5ft, so the height of the trailer bed quite often determines whether or not a certain lump load can be moved from A to B.
Secondly, there are the physical restrictions relevant to building a carrier which is sufficiently stiff in its construction to accept concentrated loads without sustaining damage. It is well known that the straight beam provides the best answers to stress problems when these are a known quantity. To have to dev late from the favourite method of construction and be forced to produce a frame which is cranked to enhance its low loading capability, and which will then be called upon to accept uneven, concentrated loads on top of that is asking for both the bread and the cake at the same time.
The third problem to take into account is that hauliers earn money only for carrying payload, There is little to be earned by an outfit that is so heavy in the unladen condition that it cannot legally or economically carry a worthwhile payload. And so the designer is faced with the need to produce a design having the most difficult combination of features and uses. It must be strong, low, light and handy. And of course it must also be produced at an attractive first cost.
Used to be simple
For many years the low-loader was a simple cranked frame with a pair or two sets of wheels mounted either on a single beam axle or a pair of oscillating axles. These were—and in many cases still are—arranged in such a way that with the vehicle jacked up so that the weight was taken off the suspension, a simple locking device could be removed and the whole of the assembly trundled away from the rear of the machine, This done, the jacks were lowered and the bed of the trailer rested on the ground, providing a loading height equal to the depth of the frame, which could be overcome by small ramps or as was more often the case, baulks of timber, sleepers and the like. This operation was, however, an arduous one from the operatives' point of view. The bogies were of necessity heavy and awkward to move about, especially in confined spaces or on bad ground conditions which prevail in many cases, particularly when loading civil engineering plant. And on top of that, and probably more significant to the vehicle owners, it took a long time and consequently in terms of vehicle usage, cost a lot of money.
In the 1950s there was an awakening to the advantages in all fields of using mechanical methods of handling goods of all types and this theme had its effect upon the heavy haulage industry. The companies who engaged in the specialist movement of very heavy gear had for many years had a large amount of their equipment built to their own specifications and these were not really affected by the change. But the smaller companies with perhaps two or three vehicles were quick to appreciate that a quicker turnround meant bigger profits and the demand for -something different" soon developed.
Labour-saving trend
As loads catered for by the medium-sized heavy haulage operator increased in size, arid the need for increased productivity weighed more heavily, so the interest in time-saving and labour-saving devices grew, The type of low-loader that has probably increased most in popularity is the trailer which employs a removable swan-neck rather than a removable rear bogie. The reasons for this are twofold. First, the swan-neck does not have to be manhandled because during
the loading operation it remains coupled to the tractive unit fifth wheel. Secondly, the well-tried and relatively cheap-to-produce tandem bogie, common to straight-frame general haulage trailers, can be mounted fixed beneath a rear swan-neck without creating all the problems of alignment inherent in removable multi-axle bogies. The tandem type of suspension is light, extremely well served from the spare parts point of view and can of course be operated on identical wheel and tyre equipment to that used on the tractive unit. Changes in Construction and Use regulations which permit longer vehicles to operate without special types authorization makes this kind of vehicle even more attractive as it can often be employed on general traffic under a normal carrier's licence when working within .the 32-ton-gvw weight limit.
In most cases simple ratchet jacks are used to support the bed of the trailer while the swan-neck is uncoupled, when the bed can then be lowered to the ground in the conventional knock-out-axle manner. It will be seen that this device merely dispenses with the labour involvement incurred in handling the bogies; all other aspects of the operation remain as they were. But there is an added operating advantage of wider utilization to be taken into account.
An extension of this type is a similar trailer on which both the front swan-neck and the bogie swan-neck can be removed. On this type the bed can be duplicated and used container style, not tying the outfit up for long periods of standing time while the load is being handled off, waiting for shipping or installation in a factory or similar premises. In my opinion this is the best type of unit a general heavy haulier can employ, for it will offer the greatest possible utilization for the lowest cost and unladen weight.
On the ground
There are other considerations, however, for some operators of low-loaders. I started by saying that load weight is not always the problem to be overcome. For instance, consider the operations of a company selling and servicing fork-lift trucks. These are mobile units in their own right, but often with quite severe limitations on their gradeability, making it impossible to drive them up a ramp steep enough to permit carriage on a standard flat-platform vehicle. Yet the time involved in removing axles or swan-necks on a demonstration tour, involving perhaps 20 or so offand re-loadings per day, rules out the conventional low-loader. It was for this purpose that ground-level loaders were introduced by several firms.
This type follows a general pattern in that conventional axles and springs are discarded in favour of independent suspension carrying stub axles. The suspension has taken many forms but always the principle has been the same. The running gear is designed as to retract rather like the undercart of an aircraft, so allowing the body to be lowered level with the ground. Time saving in the region of 200 per cent can be achieved with these models, but they have severe limitations in respect of gross trailer weight and the width between the wheel arches through which plant must pass to reach the deck.
This problem was overcome by one manufacturer who built a trailer on which the whole of the body sides and bogie assembly was raised hydraulically high above the deck for loading. It was a brilliant concept, well carried Out, but it cost too much and went the way of so many good ideas.
Several enterprising attempts have been made to produce vehicles with automatic folding swan-neck assemblies, but only a few have met with success, and that limited. On this type the neck is hinged at the top and bottom of the drop section of the frame and hydraulically extended after the tractive unit has been removed. Again this type is necessarily expensive and could prove costly to maintain also. That it has working parts makes it vulnerable to the severe distortions that heavy haulage vehicles sometimes must suffer and of course the hydraulics required to operate the neck must be powered. Although power can be via hand-operated pump, this would I consider be a "penny wise" outlook, for the only advantage of the system is the time it can save. in preparing the vehicle for loading or off-loading.
With the increased use of wheeled and tracked plant by the civil engineering industry, and because such plant has grown both in continued on page 105 size and cost to such a fantastic level, yet another new breed of low-loader almost unknown in Britain a few years ago has flourished. This is the step-framed bodyover-wheels type of unit with a ramped rear end on to which plant can be driven quite simply or, if broken down, can easily be winched aboard.
This type was probably pioneered by the War Office for the transport of armoured fighting vehicles (tanks and the like) and the only disadvantage that readily springs to mind is the inaccessibility of the inner pairs of small-diameter tyres on the heavier types in the event of a blow-out. But for the purpose it was designed for—the carriage of selfpropelled plant at relatively high speed—there is little to touch it for operating efficiency.
Combined features
Attempts have been made to get the best of both worlds in applying the groundlevel-loading facility to the full-length flat platform trailer. One particular model was equipped with powerful hydraulic landing gear which, when the tractive unit was removed from the front of the trailer, permitted the trailer deck to be lowered to the ground. Cargoes could be driven (in the case of plant) or winched aboard, when the hydraulic legs were extended, lifting the front of the trailer high enough to re-connect with the tractive unit.
This model was relatively cheap but had the drawback of a considerable slope to the rear of the body when in the running condition. This was necessary in order that the slope in the loading condition was not too severe.
It seems that whatever is done, low-loaders are condemned to compromise. Deck lengths must be sacrificed in order that frames may be dropped to a low level, or alternatively considerable slopes must be accepted in order that the loading ramp is not too steep.
Moving on from the low-loader into the realms of the transporter we find a world of highly sophisticated machinery. Most of the units in this class are built by one company, many are designed for one specific type of load and may be used only on rare occasions. Their operation and construction is outside the scope of this article; suffice it to say that no small haulier. could ever hope to either own or operate such an outfit.
In this class of vehicle I group the multiwheeled skate bogies used for the carriage of long self-supporting loads such as fractioning columns. These are usually one-off types made for hauliers (who know much more of
their problems than I) and sometimes even by hauliers who find the cost of having such equipment built by manufacturers way beyond their means.
The design of a low-loader can result in one of two things. Either one gets a vehicle which will do a job quickly—but with limitations as to the type of load it can carry, or a vehicle which will carry anything one likes to put on it, but which may take rather longer to load.