STOPPING
Page 46
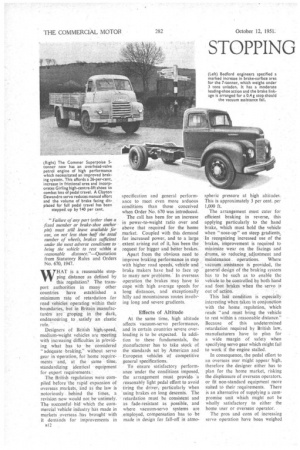
Page 47
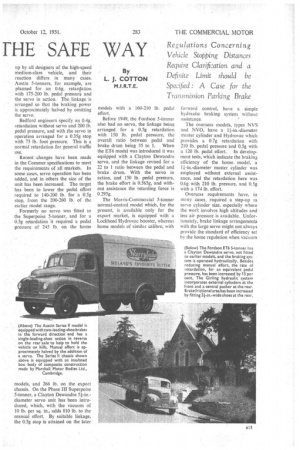
Page 48
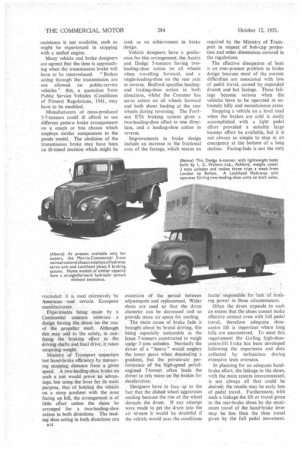
Page 49
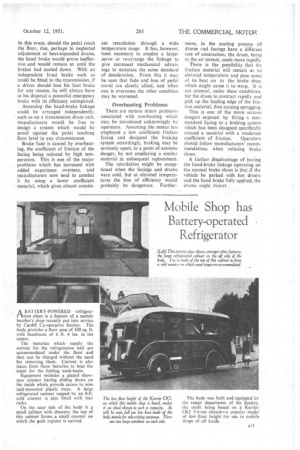
If you've noticed an error in this article please click here to report it so we can fix it.
rHE SAFE WAY Regulations Concerning Vehicle Stopping Distances Require Clarification and a Definite Limit should be Specified: A Case for • the Transmission Parking Brake.
By L. J. COTTON M.I.R.T.E.
"Failure of any part (other than a fixed member or brake-shoe anchor pin) must still leave available for use, on not less than half the total number of wheels, brakes sufficient under the most adverse conditions to bring the vehicle to rest within a reasonable distance."—Quotation from Statutory Rules and Orders No. 670, 1947.
WHAT is a reasonable stopping distance as defined by this regulation? The transport authorities in many other countries have established a minimum rate of retardation for road vehicles operating within their boundaries, but in Britain manufacturers are groping in the dark, endeavouring to satisfy an elastic
rule. ' • Designers of British high-speed, medium-weight vehicles are meeting with increasing difficulties .in providing, what has to be considered "adequate braking," without servo gear in operation, for home requirements . and, at the same time, standardizing identical equipment for export requirements..
The British regulations were compiled before the rapid expansion of overseas markets, and aS the law is• notoriously behind the times, a revision now would not be untimely. The successful bid which the commercial vehicle industry has made in markets overseas .has broughtwith it demands for improvements in
specification and general performance to meet even more arduous conditions than those conceived when Order No. 670 was introduced.
The call has been for an increase in power-to-weight ratio over and above that required for the home market. Coupled with this demand for increased power, and to a large extent arising out of it, has been the request for bigger and better brakes.
Apart from the obvious need to improve braking performance in step with higher road speeds, vehicle and brake makers have had to face up to many new problems. In overseas operation the brakes may have to cope with high average speeds for long distances, and exceptionally hilly and mountainous routes involving long and severe gradients.
Effects of Altitude At the same time, high altitude affects vacuum-servo performance, and in certain countries severe overloading is to be expected. In addition to these fundamentals, the manufacturer has to take stock of the standards set by American and European vehicles of competitive general specifications.
To ensure satisfactory performance under the conditions imposed, the arrangement must provide. 'a reasonably light pedal effort to avoid tiring the driver, particularly when using brakes on long descents. The retardation must be consistent and as fade-resistant as possible, and where vacuum-servo systems are employed, compensation has to be made in design for fall-off in atmo
spheric pressure at high altitudes. This is approximately 3 per cent. per 1,000 ft.
The arrangement must cater for efficient braking in reverse, this applying particularly to the hand brake, which must hold the vehicle when "nose-up" on steep gradients. In recognizing increased use of the brakes, improvement is required to minimize wear on the facings and drums, so reducing adjustment and maintenance operations. Where vacuum assistance is provided, the general design of the braking system has to be such as to enable the vehicle to be controlled by both hand and foot brakes when the servo is out of action.
This last condition is especially interesting when taken in conjunction with the home regulation, which reads "and must bring the vehicle to rest within a reasonable distance." Because of this undetermined retardation required by British law, manufacturers have to plan for a wide margin of safety when specifying servo gear which might fail to work if the engine stalled.
In consequence, the pedal effort to an overseas user might appear high, therefore the designer either has to plan for the home market, risking the displeasure of overseas operators. or fit non-standard equipment more suited to their requirements. There is an alternative of supplying a compromise unit which might not be wholly satisfactory to either the home user or overseas operator.
The pros and cons of increasing servo operation have been weighed up by all designers of the high-speed medium-class vehicle, and their reaction differs in many cases. Austin 5-tonners, for example, are planned for an 0.6g. retardation With 175-200 lb. pedal pressure and the servo in action. The linkage is arranged so that the braking power is approximately halved by omitting the servo.
Bedford engineers specify an 0.4g. retardation without servo and 200 lb. pedal pressure, and with the servo in operation arranged for a 0.35g stop with 75 lb. foot pressure. This is a normal retardation for general traffic use.
Recent changes have been made in the Commer specifications to meet the requirements of all markets. In some cases, servo operation has been added, and in others the size of the unit has been increased. The target has been to lower the pedal effort required to 140-200 lb. for a 0.5g stop, from the .200-260 lb. of the earlier model range.
Formerly no servo was fitted to the Superpoise 5-touter, and for a 0.5g retardation it required a pedal pressure of 245 lb. on the home
models, and 266 lb. on the export chassis. On the Phase III Superpoise 5-tonner, a Clayton Dewandre 5k-in.diameter servo unit has been introduced, which, with the vacuum of 10 lb. per sq. in., adds 810 lb. to the manual effort. By suitable linkage, the 0.5g stop is attained on the later
models with a 160-210 lb. pedal effort.
Before 1949, the Fordson 5-tonner also had no servo, the linkage being arranged for a 0.5g retardation with 150 lb. pedal pressure, the overall ratio between pedal and brake drum being 35 to 1. When the ET6 model was introduced it was equipped with a Clayton Dewandre servo, and the linkage revised for a 22 to 1 ratio between the pedal and brake drum. With the servo in action, and 150 lb. pedal pressure, the brake effort is 0.565g, and without assistance the retarding force is 0.295g.
The Morris-Commercial 5-tonner normal-control model which, for the present, is available only for the export market, is equipped with a Lockheed Hydrovac booster, whereas home models of similar calibre, with forward control, have a simple hydraulic braking system without assistance.
The overseas models, types NVS and NVO, have a 1l-in.-diameter master cylinder and Hydrovac which provides a 0.7g retardation with 210 lb. pedal pressure. and 0.5g with
a 120 lb. pedal effort. In development tests, which indicate the braking efficiency of the home. model, a 11-in.-diatneter master cylinder was employed without external assistance, and the retardation here was 0.6g with 210 lb. pressure, and 0.5g with a 174 lb. effort.
Overseas requirements have, in many cases, required a step-up m servo cylinder size, especially where the work involves high altitudes and less air pressure is available. Unfortunately, brake linkage arrangements with the large servo might not always provide the standard of efficiency set by the home regulation when vacuum assistance is not available, such as might be experienced in stopping with a stalled engine.
Many vehicle and brake designers are agreed that the time is approaching when the transmission brake will have to be reintroduced. "Brakes acting through the transmission are not allowed on public-service vehicles ". this, a quotation from Public Service Vehicles (Conditions of Fitness) Regulations, 1941, may have to be modified.
Manufacturers of mass-produced 5-7-tonners could ill afford to use different pattern brake arrangements on a coach or bus chassis which employs similar components to the goods model. The abolition of the transmission brake may have been an ill-timed decision which might be rescinded: it is used eXtensively by American • and 'certain European manufacturers.
Expel iments being made by a Continental concern embrace a design having the drum on the rear of the propeller shaft. Although this may add to the safety, in confining the braking effort .to the driving shafts and final drive: it raises unspriing weight.
Ministry of Transport inspectors test hand-brake efficiency by measuring stopping distance from a given speed. A two-leading-shoe brake on such a test would prove an advantage, but using the lever for its main purpose, that of holding the vehicle on a steep gradient with the nose facing up hill, the arrangement is of little effect unless the shoes be arranged for a two-leading-shoe action in both directions. The leading shoe acting in both directions can 4 rank as an achievement in brake design.
Vehicle designers have a preference for this arrangement, the Austin and Dodge 5-tonners having twoleading-shoe action on all wheels when travelling forward, and a single-leading-shoe on the rear axle in reverse. Bedford specifies leadingand trailing-shoe action in both directions, whilst the Commer has servo action on all wheels forward and both shoes leading at the rear wheels during reversing. The Fordson ET6 braking system gives a two-leading-shoe effect in one direction, and a leading-shoe action in reverse.
Improvements in brake design include an increase in the frictional area of the facings, which means an extension of the period between adjustments and replacement. Wider shoes are used so that the drum diameter can be decreased and so provide more air space for cooling.
The main cause of brake fade is brought about by brutal driving, this being especially noticeable in the latest 7-tonners constructed to weigh under 3 tons unladen. Normally the driver of a " heavy " would employ the lower gears when descending a gradient, but the private-car performance of the high-speed petrol. engined 7-tonner often leads the driver to rely more on the brakes for deceleration.
Designers have to face up to the fact that the dished wheel aggravates cooling because the rim of the wheel shrouds the drum. If any attempt were made to get the drum into the air stream it would be doubtful if the vehicle would pass the conditions required by the Ministry of Transport in respect of hub-cap projection and other dimensions covered in the regulations.
The effective dissipation of heat is an ever-present problem in brake design because most of the current difficulties are associated with loss of pedal travel, caused by expanded drum', and hot facings. These failings become serious when the vehicles have to be operated in extremely hilly and mountainous areas.
Stopping a vehicle on a level road when the brakes are cold is easily accomplished with a light pedal effort provided a suitably large booster effort be available, but it is not always so simple to stop in an emergency at the bottom of a tong decline. Facing-fade is not the only
factor' responsible for--lack'df. braking power in these circumstances.
Often the drum expands to such an extent that the shoes cannot make effective contact even with full pedal travel, therefore adequate shoecentre lift is important where long hills are encountered. To meet this requirement the Girling high-shoecentre-lift hake has been developed following the experience and data collected by technicians during extensive tests overseas.
In planning for an adequate handbrake effort, the linkage to the shoes, with the main system interconnected, is not always all that could be desired; the results may be early loss of pedal travel. Furthermore, with such a linkage the lift or travel given to the rear-brake shoes by the maxi: mum travel of the hand-brake lever may be less than the shoe travel given by .the full pedal movement. • In this event, should the pedal reach the floor, due, perhaps to neglected adjustment or heat-expanded drums, the hand brake would prove ineffective and would remain so until the brakes had cooled down. With an independent hand brake such as could be fitted to the transmission, if a driver should lose his foot •brake for any reason, he will always have at his disposal a powerful emergency brake with its efficiency unimpaired.
Assuming the hand-brake linkage could be arranged independently, ' such as on a transmission drum unit, manufacturers would be free to design •a system which, would be proof against the Pedal reaching
• floor level in any circumstances. Brake fade is caused by overheat-, ing, the coefficient of friction of the facing being reduced by high temperature. This is one of the major problems which has increased with added experience overseas, and manufacturers now tend to combat it by using a lower coefficient material, which gives almost consist
ent retardation through a wide temperature range It has, however, been necessary to employ a larger servo or re-arrange the linkage to give increased mechanical advantage to maintain the same standard of deceleration. From this it may be seen that fade and loss of pedal travel are closely allied, and when one is overcome the other condition may be worsened.
overheating Problems
There are certain minor problems associated with overheating which may be introduced unknowingly by operators. Assuming the maker has employed a low coefficient friction facing and designed the braking system accordingly, braking may be seriously upset, to a point of extreme danger, by not employing a similar material in subsequent replacement.
The retardation might be exceptional when the facings and drums were cold, but at elevated temperatures the loss of efficiency would probably be dangerous. Further
more, in the. cooling process all drums 2nd facings have a differem rate of contraction, the drum, being in the air stream, cools more rapidly There is the possibility that the friction material will remain at an elevated temperature and pass some of its beat on to the brake shoe, which might cause it to warp. It is not unusual, under these conditions, for the drum to contract rapidly and pick up the leading edge of the friction material, thus causing spragging.
This is one of the more serious dangers exposed by fitting a nonstandard facing to a braking system which has been designed specifically around a material with a moderate
coefficient of friction. Operators should follow manufacturers' recommendations when 'refacing brake shoes. , A further disadvantage of having the hand-brake linkage operating on the normal brake shoes is that if the vehicle be parked. with hot drums and the hand brake fully applied; the drums might distort.