FRICTION MATERIALS
Page 44
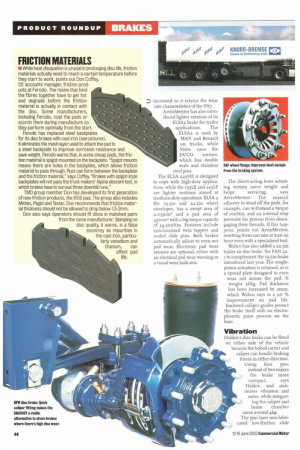
If you've noticed an error in this article please click here to report it so we can fix it.
• While heat dissipation is crucial in prolonging disc life, friction materials actually need to reach a certain temperature before they start to work, points out Don Coffey, OE accounts manager, friction prod ucts at Ferodo. The resins that bind the fibres together have to get hot and degrade before the friction material is actually in contact with the disc. Some manufacturers, including Ferodo, coat the pads or scorch them during manufacture so they perform optimally from the start.
Ferodo has replaced steel backplates for its disc brakes with cast iron (see pictures). It eliminates the mesh layer used to attach the pad to a steel backplate to improve corrosion resistance and save weight. Ferodo warns that, in some cheap pads, the friction material is spigot-mounted on the backplate. "Spigot mounts means there are holes in the backplate, which allows friction material to pass through. Rust can form between the backplate and the friction material," says Coffey. "Brakes with spigot-style backplates will not pass the truck makers' Alpine descent test, in which brakes have to survive three downhill runs."
TMD group member Don has developed its first generation of new friction products, the 13100 pad. The group also includes Mintex, Pagid and Textar. Don recommends that friction material thickness should not be allowed to drop below 1.5-2mm.
Don also says operators should fit discs in matched pairs from the same manufacturer. Skimping on disc quality, it warns, is a false economy as impurities in the cast iron, particularly vanadium and titanium, can affect pad life.